Engineers take a novel, low-risk approach to marine propulsion with a hydraulic hybrid design.
Much like the trend in mobile-equipment markets over the last decade, shipbuilders and their suppliers have made steady, incremental improvements in terms of vessel performance, fuel efficiency and lower emissions. Many in the marine industry are now pushing the next wave of innovation with more-complex but “greener” systems like diesel-electric hybrids and battery-based power plants. Yet, at the same time, owning and operating (O and O) costs are still the key drivers for the customer’s bottom line.
“It’s a bit of a balancing act,” explained Nathan Kelly, Product Development Manager with Caterpillar Marine, headquartered in Hamburg, Germany. “Many factors relate to cost—everything from upfront price, up-time and fuel efficiency to maintenance costs and, ultimately, the resale value. And in the back of everyone’s mind are safety and regulatory issues like emissions. With change comes risk. We have to make sure that the latest technology being implemented into the market is not only shiny and fancy and new, it actually benefits customers’ O and O cost and it’s done so in a safe and compliant way.”
As a result, engineers at Cat Marine are taking a novel approach to addressing users’ demands for higher performance and efficiency—while mitigating the risk. The company recently announced a collaboration with Sanmar Shipyards in Istanbul, Turkey to build an innovative tugboat with a hydraulic hybrid propulsion system. Called the Cat Marine Advanced Variable Drive (AVD), the patented system reportedly leverages Caterpillar’s extensive know-how in integrated power systems initially developed for mining and construction applications. Sanmar, with 40+ years of experience and the largest tug builder in Turkey, is recognized as a market leader at the forefront of the tug building industry.
Hydraulic hybrid propulsion
The AVD system provides significant improvements in both fuel efficiency and vessel performance through a hydromechanical propulsion system, said Kelly. Like many tugboats, the Sanmar design has two main engines mounted side-by-side and driving twin propellers. But it also includes two hydraulic motors and an auxiliary engine.
In a conventional tugboat, each diesel engine turns a driveshaft and powers a single output, the propeller. Throttle setting determines engine speed and operating performance. The AVD, in contrast, is a fully integrated propulsion system, according to Kelly. “Each drivetrain has two inputs—a diesel engine and a hydraulic motor—still with one output, the propeller. Combining the two input powers into a single output is the heart of the AVD.”
The engine and hydraulic motor connect to the shaft and propeller via a planetary gear set, and that allows gear ratios to be freely selected to achieve the required output. This lets the AVD operate the engine at its most efficient point independent of propeller speed—while supplementing power hydraulically. The result is excellent vessel response and performance, along with significant fuel cost savings.
Operating modes
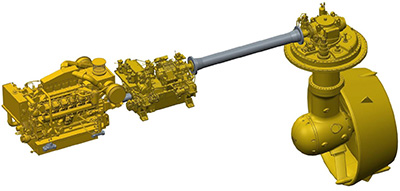
Cat Marine’s Advanced Variable Drive powers the propeller driveshaft via the main engine and a hydraulic motor.
The hydraulic motor is part of a hydrostatic system where the hydraulic pump runs off either the main engine or a smaller auxiliary engine. And clutch engagement of the drives to the gear set gives users the option of powering the system with either the diesel engine, the hydraulic motor or both—and lets the AVD run in one of three operating modes.
In the first, called the “work” mode, the main diesel engine is on, seamlessly clutched in, and provides power to the planetary gear. At the same time, the engine turns a hydraulic pump which supplies the hydraulic motor and aids in driving the planetary gear. This is a parallel-path propulsion system with both the engine and hydraulic motor, through the planetary gears, providing power out to the propeller, noted Kelly.
This hydromechanical-propulsion option permits the most efficient combination of engine and hydraulic system operations, and can accommodate most working maneuvers. “The benefit in doing this is you can optimize your engine speed to whatever is the most optimal efficiency. So you can run your engine as needed, and then you power the planetary gear with the engine as well as the hydraulic motor,” he said.
In the second mode, called the “transit” mode, the main engines are shut off and unclutched, and the auxiliary engine powers the hydraulic motors for both shafts. The hydraulic system provides adequate propulsion for most low-level maneuvers, and running just a single, smaller engine reduces emissions, lowers maintenance costs, and allows for greater operational efficiency.
“This enables you to do any transit or lower load operation for the vessel which, on a tug, we estimate is a very large percentage of its operating time, upwards of 80%. So for 80% of the operating time of the tug, you could satisfy that need with a single, smaller auxiliary engine,” said Kelly.
The third mode, called “boost” mode, involves running both the main engines and the auxiliary engine. This provides full power from the main diesel engines, and supplemental power from the hydraulic motors via the auxiliary engine. This is used for bollard pull (the zero-speed pulling capability of a tug), maximum vessel speed and other high-power demands.
AVD benefits
“The AVD is a very versatile product,” added Kelly. It enables a lot of the performance enhancements that are necessary to improve fuel efficiency, emissions, smoke and noise, as well as vessel maneuverability and response—all the things that customers care about when they’re thinking about new technology.
And for customers hesitant to embrace cutting-edge technology due to the inherent risk, the AVD is a well-tested system that has been used on Caterpillar mining equipment for about five years. “We have a good reference point in terms of the actual efficiency benefits that it provides,” along with the underlying design and development process and overall track record in the field, he said. “The AVD system is a proven technology that we’re now implementing into marine applications to satisfy customer innovation demands. There’s a lot of interest in hybrid systems and batteries and electric-drive systems. This is a bit of a different approach to that same problem.”
As mentioned previously, the AVD allows propeller speed independent of engine speed to optimize engine efficiency, leading to fuel savings of 15 to 20%. Basically, it offers all the benefits of a variable-speed diesel-electric propulsion (DEP) system with a much smaller footprint and price, said Kelly. Many larger offshore vessels have moved to electric systems for the inherent efficiency benefits. “But those systems are very large and expensive. The AVD accomplishes the same goal, and it’s smaller and lower cost than a DEP system. Hydraulic motors are a fraction of the cost and size of electric motors, and the hydrostatic circuit is much more economical than the power electronics needed for an electric system,” he emphasized.
Main engines can be downsized in most applications with supplemental power provided by the auxiliary engine. For example, the Sanmar AVD system will use Cat 3512 engines. A conventional tug with the same capabilities would require Cat 3516-size engines, which measure about 2.5 ft longer and with displacements about 20% higher.
For the same total installed power, the AVD system enables a more efficient installation with smaller main engines, and an auxiliary engine that would see more-optimal use. Plus, the secondary engine doubles as a firefighting-pump engine, which adds to the versatility of the system, said Kelly. In contrast, many conventional vessels require a dedicated firefighting-pump engine that is generally underutilized.
The AVD system is also flexible and can accommodate either diesel, natural gas or gas-turbine engines as prime movers, to provide various levels of engine load capabilities and speeds. And because auxiliary engines can accommodate low load or transit operations, that greatly extends the time between overhauls and reduces service costs on main engines. Finally, the system provides inherently high levels of propulsion redundancy.
A look at subsystems
The Sanmar tug’s two Cat 3512 main engines are sizable, V-12, 58-liter units that measure about 8.5 ft long with 7-ft height and width. Each generates about 2,000 hp. The single auxiliary engine is a Cat C32. While smaller than the main engines, it’s still a large V-12 with a 32-liter displacement generating about 1,500 hp.
The variable displacement, axial-piston pumps and motors that make up the hydrostatic drive system are designs proven from years of experience in construction and mining applications. They’re quiet, efficient and, in this application, run at low to medium pressures.
However, the overall power requirements are significantly greater. “A 70-ton bollard pull tugboat is on a much larger magnitude of power than on some of the mining equipment. So the size and design of the system is new and, in addition, there are two propulsion systems with two propeller shafts. But the actual technology behind the AVD concept is unchanged,” he said.
Kelly hesitated to specify the exact sizes of the hydraulic components, stating “It’s a very scalable solution.” Previously when a design required a certain bollard pull, engineers weighed various engine options from the different manufacturers in order to precisely size them to the application, he explained. Now, designers can specify a smaller main engine and then scale the hydrostatic system as needed to meet maximum power requirements. For this specific system, the hydraulic power is approximately 500 kW (670 hp) per shaft. But the hydrostatic output can be easily scaled up or down as needed to meet requirements of a wide range of vessel types, applications, and power levels, he said.
Bridge controls will include a push-button display for selecting the operating mode. In addition, a firefighting-pump option provides propulsion via the main engines, similar to the work mode, while the auxiliary engine powers the firefighting pump. The entire AVD system of engines, thrusters, gearboxes, pumps, motors, electronic controllers and bridge controls are part of a Cat-branded package and serviced through Caterpillar’s dealer network.
Sanmar specifics
The Sanmar hydraulic-hybrid under construction is a RAmparts 2400SX harbor tug designed by Robert Allan Ltd., rated for 70-ton metric bollard pull and carrying a FiFi 1 firefighting designation. (Such a system can spray about 10,500 gpm of water more than the length of a football field.)
In addition to improved performance, lower noise and lower emissions, some of the real benefits of the AVD are the size and the cost, compared to a conventional electric battery-powered hybrid system. Thus, Cat Marine has initially targeted tugs, which have small, compact engine rooms. In addition, the harbor tug operating profile makes the AVD a good fit, said Kelly. Compared to a conventional tug with equivalent bollard pull, the return on investment (ROI) is estimated at three years or less based on projected fuel and operating cost savings.
However, because it’s scalable, the system could easily be integrated into larger or smaller vessels in the future, he said. “From a strategic standpoint, we’re really looking at the AVD system as an alternative to some of the other hybrid solutions, like battery-powered hybrid systems. On the other hand, the benefits in terms of O and O cost and efficiency increase when you get to very high load profiles and more cyclical operations. So we feel like there are other applications, dredge for example, with high load factors and different cyclical operations, that could really benefit from this system as well.”
Caterpillar Marine
www.cat.com/marine
Filed Under: Fluid Power World Magazine Articles, Pumps & Motors, Slider