Global heavy equipment manufacturer Komatsu America Corp., Rolling Meadows, Ill., announced that the FrontRunner Autonomous Haulage System (AHS) has achieved the unprecedented milestone of more than two billion tons of surface material moved in driveless operation. According to company officials, the FrontRunner system has now hauled more than all other commercial mining autonomous haulage systems combined.
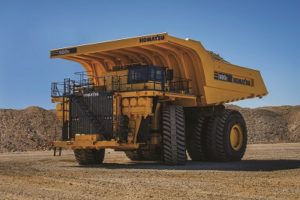
Komatsu’s 400-ton capacity 980E-4 mining truck is a workhorse in autonomous hauling operations.
Since its first commercial deployment in 2008 at CODELCO’s Gabriela Mistral (Gaby) copper mine in Chile, the FrontRunner AHS has experienced exponential growth in cumulative production, breaking the one billion tons mark in 2016 and the 1.5 billion tons mark in late 2017. This has been accomplished with more than 130 trucks in operation to date. An additional 150 trucks will deploy to the Canadian oil sands over the next seven years.
One of the keys to success has been the simple and efficient hydraulics used in ultra-class vehicles such as the 400-ton capacity 980E-4 haul truck. The rear-dump mining vehicle includes an 18-cylinder, 3,500-hp engine and ac-electric drive, and reportedly provides an optimal match in large-scale mining applications with big bucket shovels (55 to 99 yd3) — loading out in three to five passes, depending on bucket size and material density.
The hydraulic system is a proven and reliable design with fewer parts than other OEMs, said Komatsu officials. The system uses a single 250 gal (947 l) tank, providing one common source of fluid for steering, braking and hoisting. In-line, replaceable filtration elements provide protection from hydraulic system contamination, making the system easier to service.
An accumulator-assisted circuit with twin double-acting cylinders provides constant-rate steering. Secondary steering is automatically supplied by the accumulators. Two 3-stage dual-acting outboard cylinders, with internal cushion valves and over-center dampening, hoist the bed and dump loads.
The system includes dual, in-line high pressure pumps in a single package. Hoist and brake cooling are handled by a tandem gear pump with output of 246 gpm (931 lpm) at 1,900 rpm and 2,750 psi. A pressure-compensating piston pump with output of 65 gpm (246 lpm) at 1,900 rpm and 3,000 psi serves steering and brake functions.
To keep downtime to a minimum, Komatsu developed a sub-frame pump module that can be removed and replaced as a single unit. This reduces change-out time and allows easy access to the hydraulic pump module.
Working closely with customers, FrontRunner AHS’s ten-year zero-harm and productivity record, and unmatched ability to accommodate an array of mining environments, has let the company accelerate the pace of AHS deployment, said Komatsu officials. Today’s FrontRunner system operates around the clock hauling copper, iron and oil sands, at seven sites, across three continents. “The ongoing investment in technology and equipment by major mining companies in Chile, Australia and Canada underscores their belief in the value of autonomous haulage,” said Anthony Cook, Vice President Autonomous and Communications Solutions at Modular Mining Systems, a subsidiary of Komatsu.
“AHS continues to play an increasingly crucial role in effective mine management as more and more operations transition from manned to unmanned fleets,” said Dan Funcannon, VP/GM, Large Mining Truck Division, Komatsu America. “As the demand for autonomous systems grows, Komatsu will continue raising the bar in an effort to help mines provide safer working environments, maximize production, and reduce operating costs.”
To underscore the company’s commitment to progress, Komatsu plans to enhance the AHS’ mixed-operation functions, enabling manned trucks of any make to interoperate with Komatsu AHS trucks in a blended operation. Komatsu is also working with industry stakeholders towards standardization of interoperability between Komatsu and non-Komatsu autonomous vehicles, to improve safety and efficiency at customer operations.
Komatsu America
www.komatsuamerica.com
Filed Under: Mobile Hydraulic Tips