Contributed by Alan Astbury, Simulation Methods Developer, Trelleborg Sealing Solutions
To achieve optimal efficiency, fluid power applications and their sealing components need good friction characteristics and long life to reduce maintenance. Engineering simulations and the experts to interpret them can result in better sealing and material recommendations, leading to faster prototyping, predictive maintenance and a more efficient fluid power system for original equipment manufacturers (OEMs). In this Q&A, we will explain how engineering simulations can help OEMs succeed in an environment where the demands for efficiency are increasing.
Q: How can engineering simulations help predict the lifetime of a seal?
A: At the start of a project, customers want to know the practicality of a sealing design including how long it will function. Engineering simulations are the most effective way to answer questions about the durability of seals. Testing if a system’s component will work is generally easy but understanding how long it will last traditionally requires long-term testing. However, this kind of testing is often impractical. Simulation can cut down the time needed to prove a component’s lifetime.
Q: What specific types of simulations predict seal lifetime?
A: One valuable Finite Element Analysis (FEA) simulation that an OEM’s sealing partner can perform looks at the reduction of a seal’s contact pressure over time in a system to predict when maintenance will be required. In this simulation, experts determine the compression set a seal will experience under specified loading and temperature conditions. Information gained can be extrapolated over decades in a matter of hours to determine a seal’s lifetime.
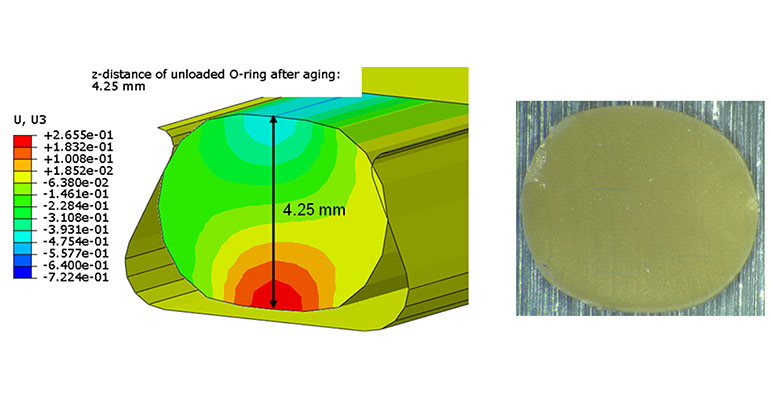
Another method is non-parametric optimization. During the design phase of a seal, this simulation can determine where stress can be reduced on the seal under loading conditions.
These techniques and simulations enable sealing manufacturers to design a seal with optimized characteristics and provide guidance to OEMs on how to meet material, temperature and pressure specifications that will maximize the life of a seal. Being able to predict a seal’s lifetime offers a higher return on investment for OEMs because it allows for planned maintenance rather than unplanned line stops or in-field stoppages that are expensive to resolve.
Q: Heat from friction on a seal is a concern affecting efficiency. This is particularly important in rotary applications where the seal continuously maintains contact with the same region of the shaft. What are some engineering simulations that can help predict frictional heat?
A: Using coupled thermal-mechanical analysis simulation, experts can predict the heat generated by a seal from friction and the effect this will have on a seal’s performance. Additionally, this analysis can show where different amounts of heat are generated. For example, the heat produced at the seal’s edge can be many times greater than the temperature of the surrounding fluid. Making sure the material selected is suitable for the temperature range caused by frictional heat helps ensure long seal life.
In addition, when a seal heats up, it typically becomes softer leading to a different loading profile on the hardware. By analyzing the seal’s heat generation and how this changes its mechanical properties, experts can determine the best sealing profile for a given application.
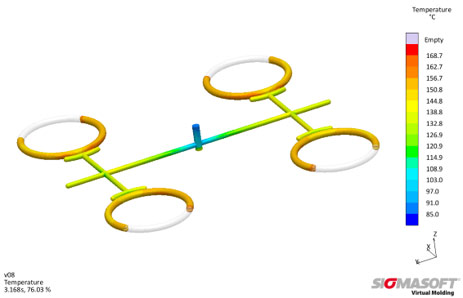
Q: What about simulations for elastomer-specific seal designs?
A: There are two main simulations that offer valuable information for elastomer-specific seal designs: injection molding simulations and non-linear viscoelastic performance simulations.
Using injection molding simulation, experts can analyze the manufacturing process of the material including how the material flows into the mold and if it fills all the cavities. It can also determine how much the elastomer will shrink once it is removed from the mold and predict the final shape of the product. To achieve the greatest seal efficiency, experts can optimize temperatures and injection pressures during this simulation.
Non-linear viscoelastic performance simulations measure an elastomer’s speed of mechanical response over both long and short durations. Using a dynamic mechanical analyzer set at different temperatures and frequencies, experts can combine the data produced with standard tensile and compression testing to see how elastomers cope with shock loading conditions in both static and dynamic states. This information can also indicate if a sealing system is likely to leak due to a reduction in the sealing force.
Trelleborg Sealing Solutions
www.trelleborg.com/seals
Filed Under: Components Oil Coolers, Featured, Sealing, Sealing & Contamination Control Tips, Seals