Contributed by Nathan Irvine – Product Specialist, Drives & Sensors, Aventics Corp.
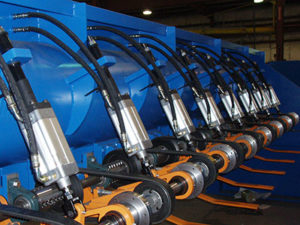
Using ideal cushioning technology from Aventics, medium-duty aluminum cylinders are often specified in high-speed/high-load applications, lasting longer and improving production throughput.
For high-speed equipment in applications such as timber processing, heavy-duty steel pneumatic cylinders were often specified because of cycle speeds and harsh operating conditions. However, using ideal cushioning technology from Aventics, medium-duty aluminum cylinders are often specified in high-speed/high-load applications, lasting longer and improving production throughput. At the same time, the user benefits from reduced maintenance and cost of replacement parts. (It should be noted that in many applications, only pneumatic cylinders with excellent mechanical cushioning adjustment and impact bumpers can truly achieve ideal cushioning.)

Ideal cushioning is a method of decelerating the load as the piston reaches the end of its stroke inside the cylinder. As a result, the end-of-stroke bounce or end-cap slamming is eliminated, which is a main culprit of cylinder wear, speed and noise.
Ideal cushioning is a method of decelerating the pneumatic piston as it reaches the end of its stroke inside the cylinder. As a result, the end-of-stroke bounce, or end-cap slamming, is eliminated, which is often a main culprit of cylinder wear, longer cycle time and noise. The piston velocity reaches its maximum along the way, and is exactly zero by the time it reaches the end cap. By reducing the piston velocity to zero speed at precisely the end of travel, the cylinder incurs less stress. Vibration in the machine is also reduced and the total cycle time is improved, sometimes boosting machine speed by as much as 30%.
For ideal cushioning to work properly, the piston velocity must be adjusted correctly during commissioning. Since the velocity of the piston in a cylinder may be difficult to detect by eye, technicians often used an electronic velocity time meter (VTM) that was attached to the outside of the cylinder tube. The VTM allowed the true velocity of the piston to be determined quickly and easily, even for all sequences in a cylinder cycle.
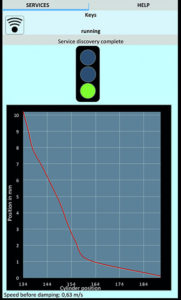
Aventics has introduced a new Cushioning Adjustment Tool (CAT) to help installers set up ideal cushioning parameters using an LED display and advanced visualization in an optional smartphone app that clearly shows which way the cushioning needs to be adjusted.
The cushioning adjustment was then completed using a simple screwdriver, where the free outlet flow was adjusted so the piston stopped right at the end cap with zero speed. Cylinder pistons could then be adjusted one at a time with the first one used as a standard to conform to a maximum speed for a given pressure and cylinder load.
Tool for cushioning adjustment
Adding to its wide range of engineering and assembly tools, Aventics has introduced a new Cushioning Adjustment Tool (CAT) to improve on the VTM concept and help installers set up ideal cushioning parameters using an LED display and visualization with an optional smartphone app that clearly shows which way the cushioning needs to be adjusted. The smartphone app also displays the piston speed just before cushioning begins, plus the cushioning characteristics as a plot of piston position versus time. This allows users to fully benefit from the characteristics of the AVENTICS cylinders in the system, as the need for additional adjustment becomes a thing of the past.
The diagnostic tool attaches easily to the cylinder. The CAT detects if and how the cushioning setting must be changed by evaluating the position and speed of the piston using magnetic sensors. The device only measures 2.2 by 3.3 in. and can be removed once everything has been set correctly. An integrated battery that can be recharged via a micro USB connection supplies the power. The associated app is compatible with Android smartphones using a Bluetooth connection, with the iOS application coming soon.
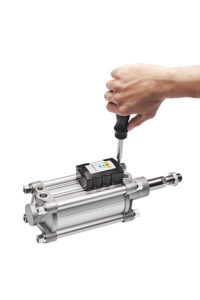
In the past, you often needed experience, a special touch and a lot of patience to correctly adjust the cushioning for pneumatic cylinders. Now you simply adjust the cushioning according to the LED.
After the sensor is attached to the cylinder and switched on, all functions can be read from the three-color LED display showing red, yellow and green, or from your smart phone. In the past, you often needed experience, a special touch and a lot of patience to correctly adjust the cushioning for pneumatic cylinders. Now you simply adjust the cushioning according to the LED cues. Dialing in the cylinder cushioning is still handled the same way using a basic screwdriver, but the new Cushioning Adjustment Tool makes the adjustment easier, faster and more precise for trouble-free operation, quiet running, and high cycle frequencies in pneumatic systems.
Aventics Corp.
www.aventics.com/us/IdealCushioning
Filed Under: Pneumatic Tips