By Josh Cosford, Contributing Editor
When buying a cylinder repair kit, you generally expect to open a plastic bag filled with O-rings, rod seals, end seals and other synthetic rubber bits used to freshen up an old air or hydraulic cylinder. Often, we call such an assembly of parts a seal kit, which completely forsakes a family member necessary for the function and reliability of every cylinder: the wear rings.
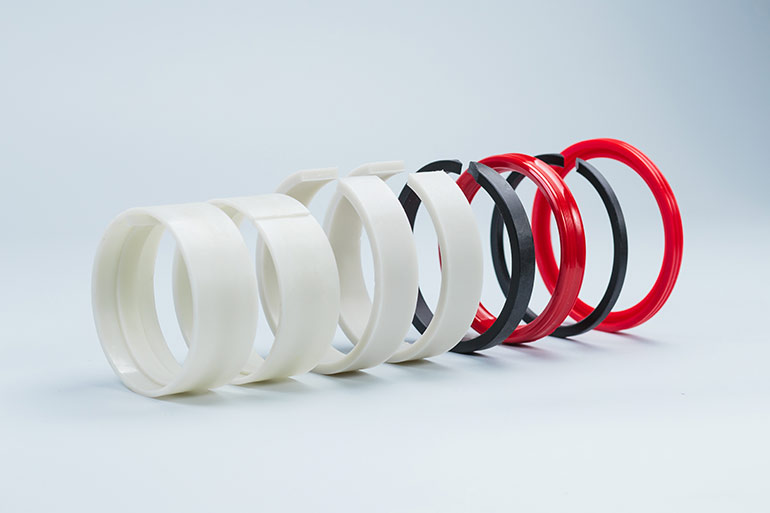
These strips or stubby-cut, flat circles answer to many names: guide bearings, wear strips, wear bands and bushings. Regardless of nomenclature, these strips are essential to the function and reliability of any air or hydraulic cylinder. The wear ring helps to guide and support both the piston and the rod, keeping it aligned axially while acting as a low-friction sacrificial surface.
The piston almost always employs a wear ring, which is the point of contact between the piston assembly and the barrel wall. As the cylinder strokes, the wear ring guides the piston through the barrel and helps support any radial loads created from the attachment end of the rod. Wear rings are highly resistant to compressive forces and should always sit proud of the machined groove they call home. You want your wear ring to fail long before your piston or barrel inside surface.
Some cylinder manufacturers also install wear rings to help guide and support the rod. Rather than reside on the OD, such as with a piston, these will slot into the ID of the head or gland, holding the rod centered as it strokes. Piston rod wear rings offer an inexpensive solution compared to bronze bushings, although they don’t offer quite as much load-bearing support. Piston rod wear rings are a must for special applications, such as a stainless-steel gland for specific applications.
Manufacturers offer wear rings in a plethora of materials for customizable support solutions. Nylon and phenolic materials are stalwarts in our industry, offering an economical and robust choice for many applications. However, their usable temperature and velocity range don’t match the designs of newer materials.
The bronze-filled PTFE material provides superior high-velocity performance across an insane temperature range, although it provides little compressive strength compared to other materials. If your application is side-load prone, modern material technology offers better solutions, such as synthetic fabric thermoset resin. This material offers superior compressive strength, although it gives up some high-velocity performance.
The big daddy of wear ring technology is the multi-layer compound bushing some manufacturers offer. An example of such an animal is the steel-bodied, bronze-lined and PTFE/Lead overlain bushing that offers the trifecta of performance every cylinder deserves — high-temperature range, high velocity and extreme compressive strength.
Wear rings come as long coils of strip material, preformed rings, or two-piece sets. With the bulk strip material, you simply cut the size as required to fit your piston or rod and save the rest for later. These coils are perfect for shops repairing all makes of cylinders while avoiding excessive stock for multiple bore sizes. Wear rings are frequently scarf cut (cut on a bias angle), making it easier to insert pistons into barrels or rods through the gland.
Any way you slice it (pun intended), wear rings get no respect for their role in ensuring cylinders operate at their highest performance potential and longest operating life.
Filed Under: Components Oil Coolers, Engineering Basics, Sealing, Sealing & Contamination Control Tips, Technologies