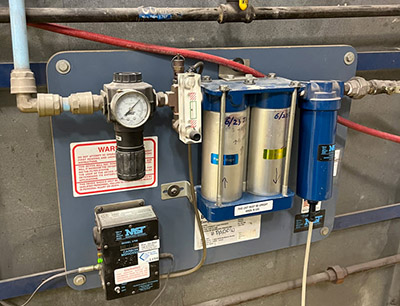
A metal process plant has two breathing air purifiers installed on site for the protection of its personnel. These units are installed to ensure hazardous Carbon Monoxide is kept out of breathing air. Recently, the two systems were evaluated by a compressed air auditor.
When paint fumes or metal particles are in the ambient air due to grinding and polishing, the staff are required to wear compressed air supplied breathing hoods to prevent them from inhaling these irritants. The trouble with compressed air supplied breathing air is that it is impossible to ensure the air the compressors ingest is free from hazardous gases.
For example, the exhaust from a service truck idling near the compressor room cooling air intake could allow carbon monoxide to enter the compressor intake and pass to the breathing devices. For this reason, regulations require breathing air to be monitored for the presence of carbon monoxide.
Many companies go further in protecting the workers, making sure the breathing air is well filtered to ensure it is clean of compressor lubricants, dust, and poisonous gases. In this plant two types exist, one using oversized carbon beds (Fig. 1) , the other using a special purifier with a catalyst that would crack any carbon monoxide into non-toxic carbon dioxide if any were present in the breathing air supply (Fig. 2). When one compares the operating costs of the two systems, the results are striking.
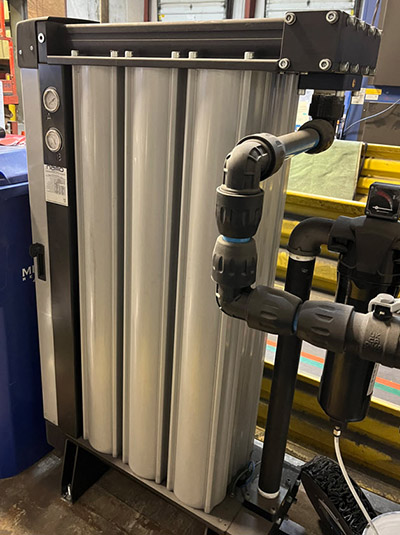
The system in Fig. 1 uses no compressed air for its operation, so the compressed air costs are almost nothing. The other system uses about 65 cfm constant flow of compressed air that continues to use air — even if nobody is using breathing air. This compressed air demand costs $8,500 per year in equivalent compressed air costs.
The auditor checked the use of breathing air and found the utilization rate on this system was less than 1%.
Fortunately, an option to save operating costs can be purchased to control the purge flow, with an expected reduction in flow of 95%. This $3,500 option will quickly pay for itself in less than a year.
It pays to check out your compressed air system end uses!
Filed Under: Components Oil Coolers, Compressed Air Technologies, Pneumatic Tips