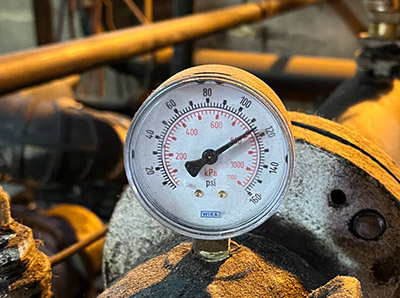
A wood products company called in a compressed air auditor to have a look at its compressed air system. System reliability was poor, and the staff was having issues with the main compressor, a 200-hp air cooled screw compressor that carried most of the plant load.
This compressor was rated at 100 psi, but recently they found that the plant pressure needed to be increased to provide enough pressure to some critical air demands at the far end of the plant. The main compressor, once reliable, had started to trip out on motor overcurrent, causing expensive unplanned production outages.
The air auditor placed measurement instruments on the system and observed the plant pressure profile. Plant pressure was running at about 100 psi, but due to pressure differential across an air dryer, the pressure at the discharge of the compressors was averaging 108 psi. This was a concern because all the compressors were rated at only 100 psi.
Careful inspection of the main compressor showed a significant issue. The air cooler of the unit was installed remotely about 30 feet away on an outside wall to take advantage of the cool air coming in from outdoors. However, rather than connecting the cooler with 3-in. piping, similar to what was on the compressor discharge, the installers decided to use 2-in. size. This mistake was causing a 6-psi pressure drop between the compressor screw element and the outlet of the cooler. In all, the compressor was running at 14 psi higher than its rating.
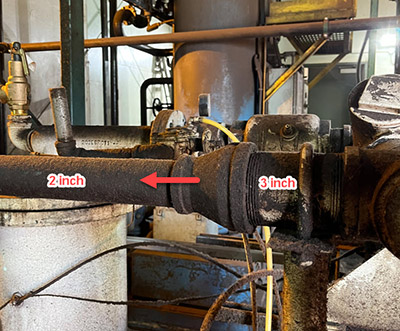
The auditor explained that every 2-psi increase in pressure over the rating of the compressor causes 1% more power to be consumed by the compressor motor. Operating at higher pressure was causing more amps to be drawn by the motor, and due to this, it was running hot. There was 7% more power being consumed by this compressor, causing motor overload.
Recommendations included reducing compressor setpoint to lower levels, upgrading the piping, and maintaining the filters on the air dryer. Once the corrections were made, the reliability improved, and the compressor consumed less energy — a double win!
Filed Under: Components Oil Coolers, Compressed Air Technologies, Pneumatic Tips