Let’s square off in a squared circle to discuss why dynamic seals are never square. I suppose one could manufacture a square seal, but perhaps that would be more of a gasket. Either way, we’re pitting static seals against dynamic seals to see who comes out on top, and you may find yourself surprised by the victor.
As you’ve probably figured out, static seals remain stationary while dynamic seals move (or are exposed to movement). Static seals find themselves used to seal two components or two areas, such as cylinder barrel end seals, pump flanges seals or spool-valve end-cap seals. Static seals are manufactured from most rubber and plastic materials, ranging from soft Buna Nitrile to hard Teflon. Like all choices in the fluid power world, seals should be chosen specifically for the application.
Viton is excellent for high-temperature applications or those with specifically dangerous fluids such as phosphate ester but is limited in high-pressure capacity. Conversely, Teflon provides superior high-pressure resistance due to its extrusion resistance but sometimes requires replacing every time the part is opened up or serviced.
Static seals will perform handily up to 30,000 psi (2,070 bar) without failure with the correct seal compound, pocket design and tolerances. Some seal material, such as NBR, pretty much turns to jelly as pressure forces the material into every micron of surface area behind it. As a result, and so long as the extrusion gaps (Figure 1) are minimal, the seal cannot squirm its way between two surfaces. The higher the pressure or, the bigger the gap, the more likely extrusion is to occur in static applications.
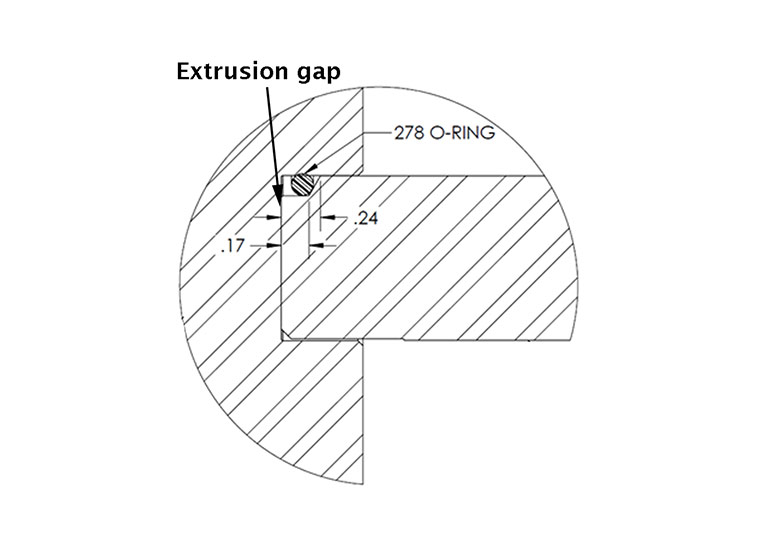
Dynamic seals require much more forethought because they count on much more than well-engineering cavities to operate effectively. Pressure-related extrusion combines with friction to create unique problems with dynamic seals. Even under low pressure, a dynamic seal could still extrude because the velocity-related friction tucks the seal through the extrusion gap, which is why dynamic seals are rated by maximum velocity.
Interference-fit seals, such as loaded T-seal, O-rings or other exotic designs, offer fantastic pressure and load-holding capacity. Still, because the seal is larger than the diameter sealed against, friction limits velocity. An O-ring with two backup washers may allow only 1.5-3.0 ft/sec velocity, and even many U-cup seals aren’t much better because they’re also loaded out the outer edge.
With dynamic seals, there is no magic bullet – leak-free seals carry the high-friction penalty, while high-velocity designs must yield some sealing capacity in favor of low-friction. PFTE crown seals with loaded energizers give designers 12 ft/sec or more. But the ultimate in velocity comes from no sealing at all. Cast iron piston rings or a combination using PTFE wear rings support the piston, but you could move the piston rod assembly freely by hand, and it offers no load-holding capacity whatsoever. Just brute force and high flow allow these cylinders to traverse as quickly as desired (within reason).
After the bell rings, who wins this bout? I’m sure you’ve figured out that the judges have called a draw. Static and dynamic seals both provide legitimate options for differing applications, and most hydraulic components employ both.
Filed Under: Components Oil Coolers, Engineering Basics, Sealing, Sealing & Contamination Control Tips