Pneumatic and automation systems from Festo, Esslingen, Germany played a key role in the development of a high-speed band saw line by USNR. With headquarters in Woodland, Wash., USNR is reportedly the world’s largest supplier of equipment and related systems for the wood-processing industry.
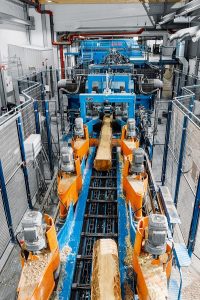
Logs pass through each station of the modular system with minimal distance in between. (Photos courtesy Festo AG & Co. KG)
The modular band-saw line includes Festo’s flexible function terminals CPX/VTSA in critical locations for actuating pneumatic and hydraulic systems, and it is currently operating at the Sävar Såg sawmill of Swedish lumber supplier Norra Timber.
“Given the tough competition in the timber industry, it is crucial to invest in advanced technology in order to increase productivity and therefore yields,” said Johan Fredriksson, project manager at Norra Timber. “With our new automated saw, we achieve a speed of 150 meters per minute. This makes it the fastest band saw line in the world,” he explained.
One highlight of the high-tech sawmill is a computer tomograph upstream of the band saw line. This assesses the quality of the logs and enables an optimal cutting pattern. It also protects the system by detecting foreign matter such as rocks that could damage the saw blades.
“Up to now, we could only use 50% of a log for sawn boards. With the new band saw line, we have increased the timber yield per log by 6%, said Fredriksson. The rest of the log is turned into wood shavings used by the pulp and paper industry as well as sawdust and bark for the sawmill’s own combined heat and power station to generate heat for the kilns.
“The new band saw line from USNR is superior to other sawing technologies because it generates relatively little sawdust and wood shavings thanks to its fine and precise cuts,” he said. A further benefit that boosts productivity is closer spacing between logs along the conveyor section — allowing the high cutting speed to be used to full capacity, due to the band saw line’s construction based on individual modules.
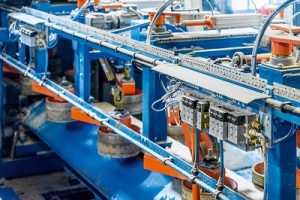
Robust CPX/VTSA terminals support different fieldbus modules such as PROFINET, EtherNet/IP, Modbus and DeviceNet.
A modular design also was critical in reducing commissioning time of the band saw line from six weeks to four, said Fredriksson. Reducers, log turners, conveyor lines and band saws are independent units that are assembled at USNR’s Swedish subsidiary in Söderhamn, including all automation systems, before being installed as complete modules at Norra Timber.
“The automation platform CPX and the function-integrated valve terminals CPX/VTSA that actuate all drives – no matter whether pneumatic, servopneumatic or hydraulic – also play a major role in our modular design,” remarked Jonas Ljung, design manager at USNR.
Festo’s CPX automation platform lets users seamlessly integrate pneumatic and electric controls via fieldbus or Ethernet networks, and it performs functions such as remote I/O, comprehensive diagnostics, condition monitoring, and motion control for electric and servopneumatic drives. In the USNR system, it combines with the powerful VTSA valve terminal platform that houses standard valves in a range of sizes, with integrated safety functions.
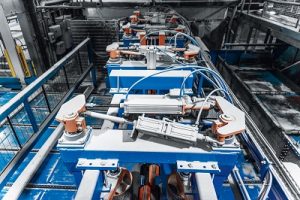
Standard DNC and ADN cylinders handle transporting, clamping and centering operations and stand up to dust and wood shavings.
The robust valve terminals with protection to IP65 can handle dust, sawdust and wood shavings and are operated with different pressure zones. They actuate a large number of type DNC and ADN pneumatic cylinders that carry out positioning, clamping, centering and transport functions. Hydraulic drives also receive electrical signals via the CPX.
If dimensions of the logs vary, which requires changes to clamping and centering positions, pneumatic cylinders are actuated using the servopneumatic module CMAX via the CPX/VTSA. The DNC-type pneumatic cylinders used for this are additionally equipped with displacement encoders to ensure precise positioning.
The CPX fieldbus module connects to process-level controls. “Here in Sweden we mostly use the PROFINET module or Modbus from Schneider Electric for other customers in Europe. In the U.S. and Canada, however, the band-saw line can be supplied with the EtherNet/IP module or the DeviceNet module on the CPX,” said Ljung when describing the high flexibility of the function-integrated valve terminals.
Likewise, the flexible function terminals CPX/VTSA, interchangeable fieldbus modules and a large number of standards-based cylinders let the sawmill modules be adapted to individual customer requirements around the globe.
Control-cabinet assembly is not necessary with the CPX/VTSA because of rugged construction and high protection class. This feature, along with fieldbus technology, reduces the time for installation and commissioning by 65%. There is less need for wiring, because there are also 80% fewer connection points. “As well as these hard facts, what’s also important for us is that Festo has been our partner in automation technology for more than 10 years and their automation experts are always on hand with service and advice – worldwide,” said Ljung.
Festo
www.festo.com/cpx
Norra Timber
www.norratimber.com
USNR
www.usnr.com
Filed Under: News