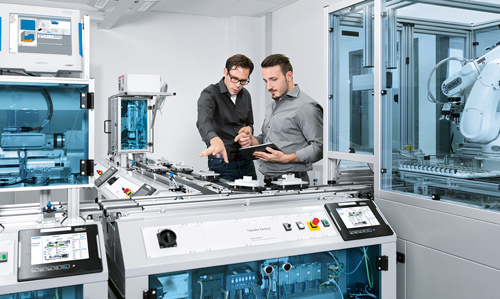
Festo Didactic’s two-year Mechatronics Program helps employers develop skills that are missing in the workforce today by combining theoretical education, hands-on and on the job training.
A few weeks ago, I wrote about the need for a revolution in this country in post-secondary education, particularly related to STEM education. We should not be pushing all of our people into four-year colleges, especially because many don’t really want to go that route and struggle to graduate in that time, coming out with backbreaking debt. But they, and their parents, are brainwashed that is what is best for them. And this has put a stigma on technical or vocational training in this country.
In my predictive column of where technology is heading in 2026, I wrote about how we need a return to the apprenticeship style of education. And I was delighted when I heard two weeks ago that Festo Didactic has launched a pilot program at its new Mason, Ohio assembly plant, in what it hopes will be come a nationwide apprenticeship program. Here Carolin McCaffrey, Head of Direct Sales for Festo Didactic, told us how they had to convince parents this might be a good option for their children. And in this apprenticeship, not only do the students get paid to learn, they are having their studies at the local community college paid for by the manufacturers.
But parents needed convincing? Those expensive, four-year colleges have everyone fooled.
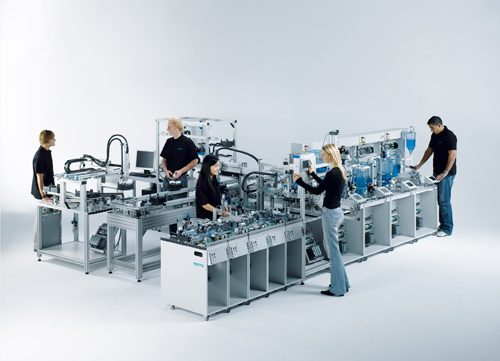
The Festo Learning Center is a unique part of the program. The Center is designed to meet international standards for production facilities and labs. It provides the apprentices a training facility where they can work with instructors on Festo workstations that simulate a work environment and corresponds to their classroom curriculum.
With 11 apprentices in the program, Festo Didactic is looking to educate these students to become what it calls mid-skilled employees, where they will come out with two years of training and an Associates degree in Mechatronics. The students spend one intensive day studying at Sinclair Community College, then one day at the Festo Learning Center in Mason, and three days with their respective manufacturing employer.
Although Festo is sponsoring the most apprentices, four other employers are on board with this program—Art Metal Group, Clippard Instruments, MQ Automation and Nestlé. And although Clippard and Festo are competitors in the pneumatics field, Clippard approached Festo because they saw a need and value in the program, McCaffrey said. And from previous conversations with Clippard President John Campbell, I know the company works closely with high schools and technical schools to find employees and train them.
The apprenticeship program is modeled after similar programs from Germany, McCaffrey said, but rather than the four-year model, they compressed the training into a two-year package. It combines theoretical education, hands-on training, and on-the-job training. So while they are earning a degree, they are gaining advanced manufacturing experience.
McCaffrey said Festo saw a need for this type of training because, for example, in the state of Ohio, there are 30,000 unfilled positions but 130,000 people looking for work. This is a way to bridge that gap.
The students are training for careers as maintenance technicians, automation specialists, service technicians, and manufacturing technicians. The apprentices are able to take what they learn in class, practice it at the Festo Learning Center, and then use that new knowledge and skill in a real-life work environment. “In terms of educational modality, the apprenticeship model couldn’t be a better fit for manufacturing,” says Vice President for Regional Centers at Sinclair Community College Scott Markland.
The Festo Learning Center is a unique part of the program. The Center is designed to meet international standards for production facilities and labs. It provides the apprentices a training facility where they can work with instructors on high-end Festo workstations that simulate a work environment and corresponds to their classroom curriculum.
And also important, “We stress cross-training so they can produce several varieties of cylinders, for example,” McCaffrey said. “There’s always direct communication to the shop floor, and they use the same components in training as the shop floor. Seventy percent of our training is hands-on.”
The students are led by a dedicated training manager, which is “part of the DNA in European companies but is a new idea for American companies,” McCaffrey added.
And not only do students learn how to operate the technology, they also need to learn to write, present and communicate effectively. “We are teaching them technical and soft skills,” she said.
In a quick chat with one of the apprentices, Chris Cunningham, I heard what I consider one of the most important things necessary in a career—passion.
“A lot of what we’ve done has been the electrical boards and lean manufacturing,” Cunningham said. “Everything is hands-on. It’s a lot of fun.”
Having fun in this hands-on manner is the best way to keep potential employees engaged in a career. Of the many classes I took for my four-year Bachelor of Science degree in Journalism, I can only count two classes that acted as real news assignments that taught me how to do my job. The rest of my training came from internships that led to freelance assignments. It was those first articles that showed me I chose the right field.
Working together to bridge the skills gap
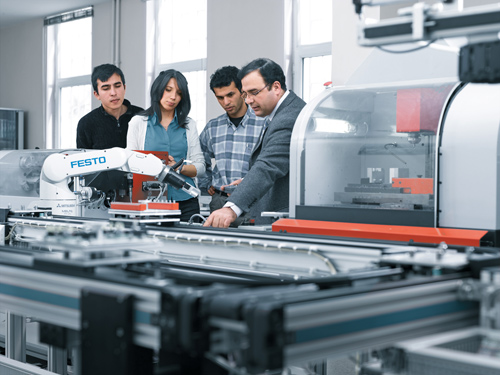
The program uses the German apprenticeship model of dual education, where apprentices learn in a classroom and maintain a steady job.
According to a press release, as advanced manufacturing and Industry 4.0 grow in the area, employers are increasingly looking for mechanical aptitude, skills in automation, the ability to read code and program machines, and electrical skills as well as problem solving and critical thinking skills. “Technology is evolving quickly,” says Jennifer Paine, Site Management Lead at Nestlé. “For us this is about a commitment to our employees, to train them in the skills they need and to advance their skill set to make our company more competitive.”
That’s what inspired the five partners to form the Mechatronics Apprenticeship Program Partners collaborative. The partners worked together to identify the needs of employers and adapt an existing curriculum at Sinclair Community College accordingly.
For one apprentice it’s about recognizing what is happening in the rest of the world and getting a jumpstart on his competition. “This is the future of maintenance tech. The more I talk to people in this field the more I see how it is big over in Europe and it’s coming this way. You get in on the ground floor and you’ll be set,” says Nathan Gledhill, a mechatronics apprentice and Nestlé employee.
Festo hopes to grow this program next year both locally in Cincinnati and eventually, nationwide, said McCaffrey. At least one new company will be joining the Mechatronics Apprenticeship. We learned on a tour that Storopack, a provider of packaging materials and packaging systems also in Cincinnati, plans to bring at least one employee and perhaps more, into the program next year. With many new employees having less than two years’ experience at Storopack, they need to gain more hands-on technical training, said Daniel Wachter, President of Storopack North America.
To become a Mechatronics Apprenticeship Program partner or for more information Corinne Haley by email at corinne.haley@festo.com. or by telephone at 848-777-2009.
Festo Didactic
www.festo-didactic.com
Filed Under: News, Pneumatic Tips