Looking for ways to further reduce your compressed air demand? Consider investigating air cylinder actuation.
Often times, air cylinders in production machinery only require significant force during a single power stroke, but still use full line pressure to return the cylinder to resting position. Let’s compare the air consumption for double acting versus a spring return cylinder.
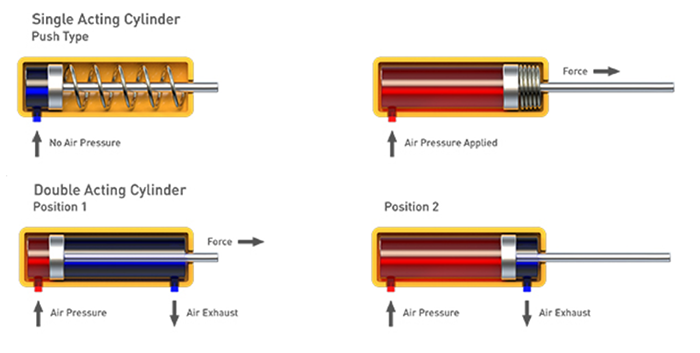
Consider an example double acting air cylinder with an internal swept volume of one cubic foot. To move the cylinder from resting position (at 0 psig) to the end of the stroke and fill it to 100 psi would consume about 6.9 cubic feet of compressed air. To move it back to resting position the compressed air for the power stroke is blown off through an exhaust, and the other side of the cylinder pressurized to 100 psi to return it, consuming another 6.9 cubic feet of compressed air (minus the volume of the rod).
Use of the same volume cylinder with spring return would reduce the compressed air consumption by about 50% because no compressed air would be required for the retract stroke.
Some other ways to reduce cylinder consumption:
- Reduce power stroke pressure – Often, the power stroke will not need 100 psi. Every 14.5 psi reduction reduces one volume of compressed air for the stroke, so using a reduced regulated pressure can save compressed air.
- Use reduced retract pressure – If spring return is not possible, reducing the retract stroke pressure will reduce the compressed air consumption per stroke by one volume for every 14.5 psi. Often very little force is required to retract cylinders.
- Use gravity – Sometimes cylinders lift against gravity, the force of gravity can sometimes be used to provide the force for the retract stroke.
Filed Under: Cylinders & Actuators, Pneumatic Tips