As interest in climate-change mitigation continues to grow around the world, many industry and technology leaders say that the efficiency of manufacturing processes must improve. One target is to replace conventional drives with highly efficient electrically powered systems. For years, manufacturers of energy-saving electromechanical drives have been trying to displace hydraulic drives from applications requiring linear movements, despite the fact that energy-efficient solutions often failed because the initial price was too high and the cost of energy was too low.
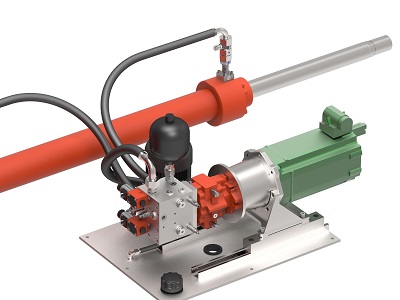
The Bucher Hydraulics HELAX hydraulic linear drive includes a servomotor, inverter, AX pump and cylinder. Efficiency matches or exceeds that of electromechanical axes with significantly higher force output.
And even with the current focus on climate problems, electromechanical drives with lower energy consumption often come up against technological limits, especially when high forces are required in a small space. In a recent white paper, author Michael Pyper of Bucher Hydraulics explained how a new system design based on the company’s AX technology is proving how hydraulic drive technology can meet high-efficiency demands.
Hydraulics catches up
Hydraulic cylinders are the obvious choice for generating linear movements with high forces, said Pyper. But one disadvantage in conventional systems: movement is controlled by valves that suffer high throttling losses and, therefore, high energy losses. Energy efficiency is further limited by hydraulic power units. These large systems usually have a centralized design, and energy then has to be distributed over long distances. And while established systems cannot be beaten on price as far as the initial costs are concerned, over the course of their service life, they result in total energy costs that can far exceed the original investment.
For some years now, manufacturers of energy-saving electromechanical drives have been trying to displace hydraulic drives from applications that require linear movements, he explained. So far, however, direct electric drives without gear units have only been available in isolated cases and with limited performance. As appealing as a direct drive may be to the designer, electric drives without any gearing are inherently very large, because many applications require high forces even at low speeds.
Basically, each electromechanical drive is driven by its own electric motor. In traditional hydraulic systems, on the other hand, an electric motor plus hydraulic pump drives several cylinders via control valves. This explains why electromechanical drive technology requires a considerably higher investment. And for high forces, which hydraulic cylinders provide easily, mechanical linear drives are much more complex and heavy.
Decentralized hydraulic linear drives
An energy efficiency strategy put forward by the German government calls for highly efficient decentralized drives that are networked and function as overall systems. This requires new subsystems and system approaches, said Pyper. Using this principle, throttling losses from the control valves can be completely prevented if each individual hydraulic cylinder is driven by its own electric motor and pump. This eliminates the root cause of the low efficiency of traditional hydraulics.
And compared to the rigid arrangement of electric motor, gear unit and spindle of an electromechanical linear drive, the components of the hydraulic linear drive can be arranged flexibly in machines and systems. The design engineer can fully exploit the compact dimensions of a hydraulic cylinder, mount the electric motor and pump in a suitable nearby location, and easily incorporate many other features of conventional hydraulics such as overload protection, heat dissipation, damping or emergency stop functions.
The critical component in applications of this type is often the pump, because its reliability is not optimal at every operating point. This is especially true with high forces and low speeds, or when reversing. When conventional hydraulic pumps were developed 50 years ago, said Pyper, designers did not have these particular operating modes in mind, but the pumps are still being used in these modes today. This is why, in a linear drive subsystem, conventional hydraulic pumps generate high power losses.
Using the innovative AX pumps, Bucher Hydraulics has now developed highly efficient, decentralized linear drives — called HELAX (hydraulic electric linear axis) — specifically to meet this need. With no throttling valves, they work with speed-controlled servomotors and AX pumps in a closed circuit. Their performance is comparable with, or even better than, mechanical linear drives while retaining the well-known advantages of the hydraulic cylinder in the areas of power, speed, robustness and reliability.
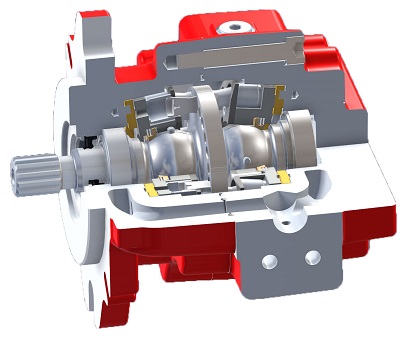
Cutaway view of the AX pump
High accuracy and force
The 24-piston AX pump is ideal for variable-speed applications, said Pyper. It features low pulsation, low noise, four-quadrant performance and a minimum speed of only a few rpm. With efficiency of up to 94%, power loss of the AX matches that of electric motors and gear units.
And thanks to on-board electronics and specific software, the hydraulic linear drive can be commissioned with only a knowledge of electrical drive technology. No special hydraulics know-how is needed. Motion-control signals are transmitted via CAN bus, for example, which the software then converts into movement commands. Users do not have to get involved with the detailed characteristics of the hydraulic system; they can fully concentrate on the function of their application. The hydraulic linear drive can therefore be integrated into a system like any electric drive.
Overall efficiency of the HELAX drive system, consisting of inverter, servomotor, AX pump and cylinder, reaches up to 82%. When recovering potential energy from lowering and braking processes, an efficiency of as much as 84% is possible.
Tests have also confirmed high positioning accuracy, even with large forces. For example, Bucher Hydraulics engineers developed a HELAX motion-control system to demonstrate such performance. The setup uses no valve technology whatsoever to make a 1.2-ton slide oscillate and completely balance an inverted pendulum at top dead center.
The direct drive is only possible thanks to the new AX pumps, which were specially developed for variable-speed applications. Their reliability at all operating points — especially at high force and low speed, and when reversing — ensures that they can take advantage of the full performance envelope of the linear drive.
Simple networking
The electric servomotor of the hydraulic linear drive connects to a dc grid. This provides for energy networking, as energy fed back from one drive can be immediately used by another. Or it can temporarily store energy in systems such as batteries and provide peak power for short periods — without burdening the power supply with high and costly current spikes.
With regard to Industry 4.0 digitalization and networking concepts, the system can be monitored with just a few sensors and drive controller data that are already available. This opens the door to efficiency-boosting energy management, condition monitoring and, last but not least, predictive maintenance. Thus, it meets far more than just the current requirements for high energy efficiency.
Decentralized linear drives can provide an ideal system for meeting more-stringent industrial efficiency requirements, such as Germany’s Energy Efficiency Strategy 2050, explained Pyper. The AX pumps guarantee reliable operation with high performance and low power loss, while at the same time all of the well-known advantages of the hydraulic cylinder are retained. This means, he said, that manufacturers of machines that require high forces have at their disposal an excellent subsystem for solving their linear drive tasks.
Bucher Hydraulics
www.bucherhydraulics.com
Filed Under: Cylinders & Actuators, News, Pumps & Motors