Much has been made of connectivity, the Internet of Things and Industry 4.0. For many businesses, condition monitoring offers the greatest potential for this rapidly expanding technology. But the real value comes when condition monitoring evolves into predictive maintenance, according to engineers at Bosch Rexroth.
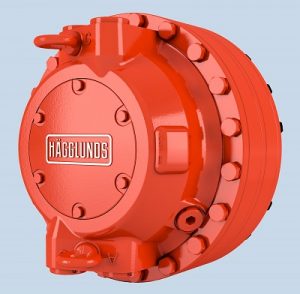
Bosch Rexroth’s Hägglunds CMp is a predictive-maintenance tool for use with the company’s direct drive systems.
In simple condition monitoring, sensors track equipment performance and alert the user to any changes in operating parameters, such as the speed, temperature and pressure in a hydraulic motor running a conveyor or winch. Systems can be built with relatively few sensors and a minimal amount of standalone hardware, at a cost far less than that of an unplanned halt in production.
Sensor data, however, can be used for much more than alerts. Analyzed properly, it can help determine when a machine is at risk of breaking down — so that corrective maintenance can be planned in advance. Predictive maintenance has many advantages: reduced need for on-site spare parts, fewer demands on service personnel, lower energy consumption and far more reliable production.
So why aren’t we seeing more of it? For many customers, the main obstacle on the path to these benefits is the security of the data and the manner in which it will be used. Customers worry that sensitive information might be lost or find its way into the wrong hands. These are valid and serious concerns, noted Bosch Rexroth officials. The customer and supplier must agree on how to regulate, share and use the data, and sufficient technical safeguards must be in place to protect the customer.
While security issues can be resolved by teaming with responsible suppliers, another complex task is to actually bring value to the customer. Sensors are inexpensive and simple to install. The difficulty lies in turning the gathered data into useful information.
In itself, condition monitoring does little more than supply customers with data, which is often difficult to interpret. This is not a solution, but rather an additional headache. For customers to get the reliability and predictability they seek, data must first be filtered and analyzed by experts. Instead of data, customers want regular reports and clear insights that help them take the service actions needed.
Machine health index
Successful predictive maintenance requires an integration of technology and human expertise, where algorithms supply the basis for smarter decisions. Case in point is Bosch Rexroth’s predictive maintenance solution for Hägglunds direct-drive systems, Hägglunds CMp, which supports a rapidly expanding group of customers worldwide.
Hägglunds CMp establishes a secure link to the customer’s drive system, where sensors are installed throughout. Bosch Rexroth’s internal firewalls protect all information that connects transmitted data with the customer, who has access via a gated cloud interface. During transmission, the data itself is meaningless, because the raw numbers cannot be paired with a sensor’s location.
Evaluation is performed by an analysis tool called ODiN, which Hägglunds CMp uses to interpret the sensor readings. During an initial machine learning phase, ODiN creates a health index that provides an accurate picture of the drive system’s normal state. It is this health index – not the individual sensor signals – that makes the difference for customers when combined with Bosch Rexroth expertise.
The health index is used to assess and regularly report on the condition of the customer’s drive system. Should drive operations deviate from the health index, Bosch Rexroth experts interpret the cause and determine what service actions might be needed to keep the system running.
Instead of simply receiving an alarm, the customer gets a concrete recommendation for actions to be taken. The information provided is not abstract data, but rather clear information that the customer can put into use.
“It’s the combination of health index and expert analysis that makes our solution work for the customer,” said Mattias Ljungdahl, application manager, Hägglunds Inside Intelligence at Bosch Rexroth. “With the health index, our analysts can not only see the trends, but also understand and predict the drive behavior for the customer. And because our algorithm is constantly learning, the solution gets better the more it works with an application.”
A clear advantage of Hägglunds CMp is its integration with Bosch Rexroth’s total service offering, said Wolfram Ulrich, vice president sales & service, Hägglunds Products at Bosch Rexroth, because customers buy not just knowledge, but also the ability to act. “The connectivity Bosch Rexroth offers is paired with fast, professional reaction by technicians with deep knowledge.”
Ljungdahl expanded on this idea, pointing out that service becomes faster, simpler and more effective when the supplier has detailed knowledge of the customer’s drive system. It is not only the alarms that make a difference, but also the regular reports that form a long-term basis for understanding.
“The solution increases the efficiency of our own service organization,” Ljungdahl explained. “When our service technicians go to a customer with Hägglunds CMp, it’s not just the problem they know before they get there. They’re familiar with the machine and how the application works normally, which makes it easier for them to get things working properly.”
Striving for optimization
Higher efficiency is also the goal of many customers who increasingly focus on lifecycle costs and productivity. Being able to plan and take corrective actions prior to failure is one aspect, because it means that maintenance can be budgeted more effectively. But another is achieving more with the existing drive equipment.
“Besides helping customers predict and avoid unplanned operating stops, we can use Hägglunds CMp to help them optimize their systems for better efficiency,” said Ljungdahl. In other words, Bosch Rexroth experts can use the health index to see not only potential failures, but also potential improvements. As Ljungdahl noted, “The high flexibility within Hägglunds hydraulic drive systems lets us adjust the motors and pumps to better match their actual use, or even reconfigure the drive for new power, torque or speed characteristics.”
Such optimization is a clear focus as the service moves forward. “The Hägglunds CMp technology gives us an opportunity to go beyond predictive maintenance, to actually optimize the operation of the installed system within its application,” said Ulrich. “The more we can understand how a system is operated, the more we can suggest in terms of energy-saving and productivity improvements, for example.”
In a more distant future, Ulrich sees the possibility of an entirely different business model for Hägglunds drive systems. “Today we use Hägglunds CMp mainly to secure reliability and lower the operating costs of our drives,” he explained. “But as our connectivity and analyses become more refined, we may be able to shift our focus further. Instead of hardware, our customers might buy performance in terms of torque and speed.”
Nonetheless, the success of Hägglunds CMp will remain rooted in its integration of technical and human components. “The value is not the data, but in the ability to interpret the data and use it to act,” said Ljungdahl. “Predictive maintenance is not about sensors or even algorithms. It’s about boosting the customer’s reliability and profitability through insights and expertise.”
Bosch Rexroth
www.boschrexroth-us.com
Filed Under: News, Pumps & Motors