Richard Meyerhoefer • Regional Applications Specialist • Delta Computer Systems
Even the roughest seas are no match for the power density, speed and accuracy of hydraulics.
For more than a century, large ships have used stabilizing fins to smooth out their ride through rolling seas. The force that fins produce is related to the angle of the fin and the speed of the vessel through the water (Figure 1). Fin systems are typically moved by hydraulics (Figure 2) and require active control. They are designed to use the speed of the sea water (while the ship is under way) to generate stabilizing force. This same force must be overcome by the hydraulics if the fin is to change direction.
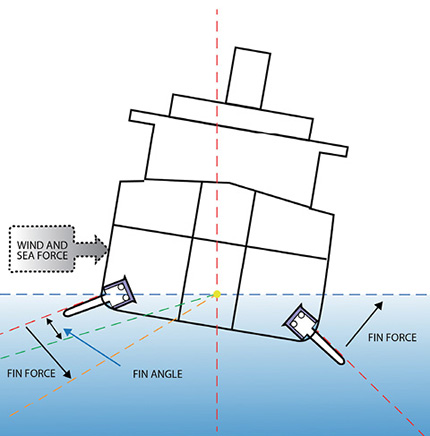
Figure 1. The force that stabilizer fins apply to act against the rolling effect of the sea is related to the fin angle and increases as the speed of the vessel increases.
The traditional way of controlling these devices is to use rotating distributors, small electric motors that produce sinusoidal electric drive to operate variable-delivery hydraulic pumps. The pumps connect to cylinders, which move the fins in a cyclic motion. More recently, PLCs have been employed to drive proportional hydraulic valves. Typically, the fin controls have been designed and supplied by the manufacturer of the fin, but one control system integrator, Pinfabb SRL of Genoa, Italy, has made a business of retrofitting new fin control systems to improve the performance of older fins’ controls. Pinfabb was the first company in the world to implement digital stabilizer control technology back in 1994, and today is the only company producing stabilizer controls that reduce ships’ energy consumption by saving fuel.
Problems with controlling stabilizer fins
Controlling the fins can be a difficult task, due to the following factors:
• Though the two fins that are typically used on a ship are controlled independently—with two different hydraulic power units—their motion must be synchronized to keep the ship stabilized. Otherwise, the comfort on board could deteriorate, and safety could be compromised as well.
• The stabilizer fins are large and heavy pieces of equipment (6 to 15 tons each, depending on ship size), but to stabilize the ship as it rolls in the sea, they need to move very accurately and quickly—up to 15 to 20° per second.
• The stabilizing fins are typically not balanced. If the hydraulic unit that operates a fin is switched off, the fin will fall to the maximum downward angle. This is an important factor to consider in calibrating the fin position for the controller.
• Finally, consider the fact that the fins must be able to be extended outside the ship during navigation in rolling seas, but stowed so as not to create drag at other times. If there is a problem with a fin that makes it unable to retract, the ship will be unable to dock at the next port and the smooth sailing of the vessel may otherwise be affected.
Finding a motion controller
These stabilization control issues are well understood by Pinfabb’s experienced engineering team. The company has been upgrading open-loop fin controls with closed-loop electronic controllers for years, and began looking for a better control system that offered higher performance and more precise operation.
The Pinfabb engineers first tried using PLCs to control variable speed hydraulic pumps, but found that this method couldn’t move the fins fast enough—or with adequate precision to meet their energy-saving design goals. Then Pinfabb CTO Matt Fabbricotti tried some board-level computers as controllers for the hydraulics, but he wasn’t fully satisfied by these. Fabbricotti looked for a reliable controller with some special capabilities for electrohydraulic controls. Discussions with his local hydraulics distributor brought him to the RMC-75E from Delta Computer Systems. As the Delta controller can control two motion axes simultaneously, only one motion controller unit was required to handle the positioning of both fins.
Fabbricotti installed the controller directly on one of his customers’ ships and was quickly able to get it working. “This was the moment when I decided to implement the RMC-75E motion controller on all our products,” he said. “Its ease of use, reliability and the easy way that the motion of the axes can be plotted and adjusted using Delta’s software, together with the large amount of control settings that are supported by the controller, made me fall in love with this product.”
In the Pinfabb system, the RMC75E can get its position feedback for the stabilizing fins from different sources. Because the system the company installs is a retrofit to whatever fin controls were previously in place, the sensors that are used can vary depending on what type of mechanical connection to the fins the Pinfabb designers can achieve. Often, position information comes from potentiometers connected with the rotational movement (up and down) of the fin, but sometimes rotary encoders and linear transducers are used.
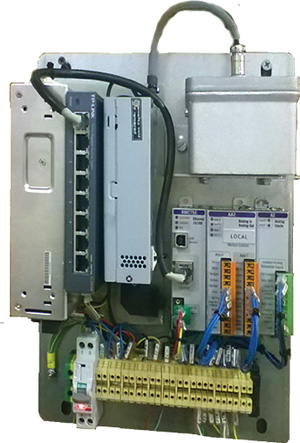
Figure 3. The Pinfabb ship stabilizer control panel, showing the RMC75E motion controller. Also shown, from the left, are the 24-Vdc power supply (used to power the RMC75 and the proportional valves), an Ethernet switch (used to connect the RMC75 and the automation panels with the industrial PC), and a 12-Vdc and 5-Vdc power supply (used to power the fin angle feedback and acceleration sensors). Above the RMC is the angular acceleration sensor that is used to monitor the ship’s movement.
The role of the PC
The motion controller (Figure 3) connects to an industrial PC that evaluates the data regarding the ship motion. The Pinfabb PC uses this data to optimize the fin angle in a way that permits the ship to lose less energy as it travels compared to using traditional fin control. The PC computes the most optimum angle of attack that the fins must have, and then sends motion instructions to the RMC through Ethernet. In turn, the motion controller rotates the fin by activating a proportional valve that operates a cylinder, called the tilting cylinder, which moves the fin up and down, changing its angle. In some cases (depending on the manufacturer of the fin system), rotation is done using a hydraulic vane motor, which is mounted inside the fin and acts like a bi-directional rotating piston.
Pinfabb’s industrial PC (which contains an Intel i7 processor, 16 GB RAM and 128-GB solid-state disk) is also connected to hydraulic pressure and fluid level sensors, which it uses to monitor the plant and inform the operators of any alarms or malfunctions. The PC also manages the rigging in and out of the fins. When the fins are not used by the crew, they are kept inside two pockets made in the hull, so that they do not affect the hydrodynamic performance of the vessel. When the stabilizing fins are needed, the PC issues the command to rotate them into position. Precise angular positioning of the fins by the RMC75 at 0° is critically important to support the retraction operation, as the hole in the hull leaves a clearance of just 6° (±3°) for the fin as it is stowed.
Compensating for problems with aging hydraulics
The mark of a good retrofit is to leave as much of the underlying mechanical structure intact as possible. This can save a lot of cost versus buying and installing new mechanical components. To enable such cost savings, the RMC controller’s closed-loop control algorithms can compensate for hydraulic systems that show signs of wear. For example, the older fin hydraulics that Pinfabb’s new controls must operate are typically more challenging to control than newer hydraulic components in maintaining the fin at the zero angle. Additionally, there could be some oil leakage from inside an older fin piston that could affect the positioning of the fin.
“With RMC, we were able to control fins that have some serious problems (like leakages) without the owner needing to spend money restoring the mechanical side,” said Fabricotti. “The RMC is fast and can be really well adjusted to optimize the piston movements.”
The RMC75E controller is programmed and the motion is tuned using Delta’s software package called RMCTools. “Programming the RMC is very easy and intuitive,” said Fabricotti. “We used Delta’s Plot Manager software to produce motion plots that show us how the fins are moving and how we could make them move better.”
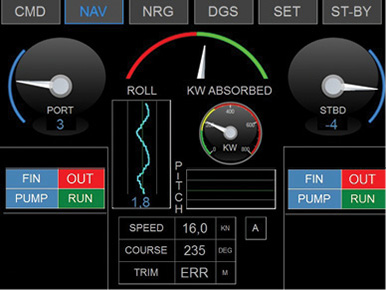
Figure 4. The Pinfabb PC displays fin angles and how well the
stabilizer system is working on a screen on the ship’s bridge and in the ship’s engine control room.
Energy savings and reliability
While providing a smoother ride for passengers and cargo, the use of stabilizers also reduces the ship cruise speed, which costs energy. In particular, the ship can be slowed and energy can be wasted when the fins are set at too great an angle or when they are moved at the wrong times. The key to minimizing the energy penalty is operating the stabilizing fins precisely and smoothly in all conditions and at all speeds.
The Pinfabb team has measured the energy required to propel a ship using conventional fin controls, and with the new closed-loop electrohydraulic motion controller in place. The results show that the energy required to move the ship at a given speed is significantly less with the system incorporating the RMC75E. “And, just as important, the new control system has proven to be highly reliable,” said Fabbricotti. “We work in an environment that is very stressful, so it is important for us and for our customers to have confidence in the motion controller used.”
Delta Computer Systems
deltamotion.com
Filed Under: Fluid Power World Magazine Articles