Environmental regulations for road vehicles are becoming increasingly stringent, and one way to reduce CO2 emissions may be to eliminate mechanical V-belts or power take-offs from future commercial vehicles. Energy-efficient electrohydraulic systems, such as the latest Smart PowerPacks from Bucher Hydraulics, provide a viable alternative.
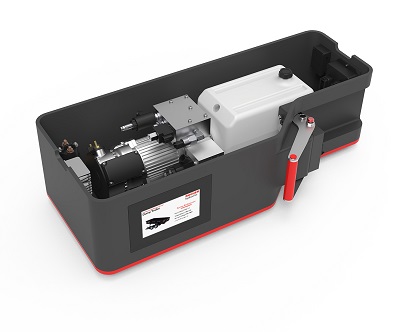
Last year, the EU adopted a European Climate Law with the aim of reaching net zero greenhouse gas emissions (GHG) in the EU by 2050. The law sets an intermediate target of reducing GHG by at least 55% by 2030 compared to 1990 levels. This falls in line with actions taken in 2019 by the EU Parliament to reduce CO2 emissions from heavy commercial vehicles by 30% compared with 2005 levels, and to meet this level by 2030. The first 15% must be achieved by 2025, in just three years. Otherwise, financial penalties will be imposed. The actual amounts have not yet been determined, but they are likely to be painful.
Currently, only over-road trucks are affected. Vehicles such as garbage collection and municipal vehicles, or trucks with loading cranes, are initially exempt from the regulation. But the EU Commission is currently discussing how to expand the rules in this area. In view of increasingly dramatic climate changes, the regulations are likely to be noticeably strict. A study detailing energy savings in fluid power by the German Federal Environment Agency evaluated construction and agricultural machinery, and the lessons learned also apply to these industrial vehicles. Among the recommendations, demand-based control of auxiliary actuators is particularly promising.
Eliminating PTOs
If EU regulations regarding CO2 emissions are actually extended to other commercial vehicles, manufacturers of auxiliary units would be particularly affected. These auxiliary units include cooling water pumps and air-conditioning compressors, but also add-on equipment for municipal work functions or loading cranes. In conventional PTOs (power take-offs), hydraulic pumps are connected to the truck engine mechanically via a gearbox, a PTO shaft or a V-belt, and run continuously. In rare cases, they can be disconnected by couplings. Because truck add-on equipment is particularly cost sensitive, these units generally rely on the most basic technology, with power losses of 50 to 75%. Incidentally, that’s the reason why truck-mounted loading cranes are often equipped with large oil coolers.
Diesel engines for trucks are optimized for driving at 80 km/h (50 mph) on the highway, where they operate efficiently at low speed and high load. To generate the high flow rate required in stationary use — for example, lifting loads — engine speed is increased. This is not only noisy, but also inefficient, as the engine then works at an unfavorable operating point with poor combustion and high specific fuel consumption.
To reduce fuel consumption and emissions, vehicle manufacturers are removing power-take offs from their next-generation products. Compressors, fans, steering and hydraulic pumps will be driven electrically using the “power-on-demand” principle, with no direct connection to the engine.
Smart PowerPack
Electrification of hydraulic power take-offs enables the use of power only when it is needed. However, the hydraulic system must become more efficient to prevent costly power losses. Bucher Hydraulics has developed the new Smart PowerPacks for utility vehicles with precisely this goal.
The package is configured to match the pressure and flow requirements of an application. The modular system includes various Bucher pumps, driven by durable brushless electric motors and inverters from the company’s Mobile Drives unit. A “smart” hydraulic block generates information on the actual flow demand and integrates the pressure relief function. The system’s inverters calculate the speed set point internally, which keeps installation costs low.
Digital controls set system parameters based on application sensor feedback, and an integrated pressure sensor adjusts pump operation for maximum efficiency (negative bypass control). Thermal sensing protects systems from overheating. Thus, the unit is able to sense the application it is connected to and modify its operating parameters and user interface accordingly. Communication is via Bluetooth, CANbus or direct-wired control options, and information is displayed on the operator’s touchscreen.
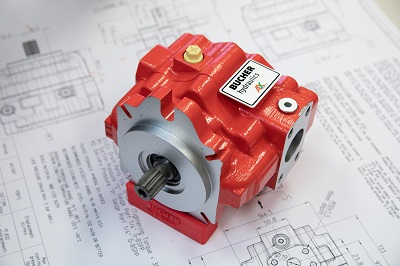
A key component for higher performance is the AX pump. It has 24 pistons and is specially designed for variable-speed applications. The large number of pistons minimizes pulsations. A wide speed range from 0 to 3,600 rpm allows for the full performance of the electric drive. The minimum speed limit of conventional pumps does not apply to the AX pump, which can operate from zero speed without any breakaway effect. With an overall efficiency between 92 and 94%, it far exceeds the values of conventional pump systems, according to Bucher officials
The Smart PowerPack is available in various sizes. For example, The “L” version operates with high voltage, >400 Vdc and power ratings of 10 to 60 kW. Maximum operating flow is from 80 to 140 lpm (21 to 37 gpm) and pressure from 265 to 330 bar (3,840 to 4,790 psi), depending on the model. The low-voltage “S” version is rated for <60 Vdc and <6 kW. Maximum operating flow is 14.4 lpm (3.8 gpm) and pressure is 230 bar (3,300 psi). The integrated tank holds 5 l (1.3 gal).
The Smart PowerPack unit is suitable for virtually all commercially available hydraulic control systems. Benefits include:
• Lower diesel consumption thanks to decoupled PTO.
• In electrified machines, better use of battery capacity thanks to demand-based flow supply.
• Reduction of cooling requirements.
• Significantly quieter operation.
In addition to the AX pump for high performance, the modular system also includes external and internal gear pumps, thus covering a wide range of applications. As many body manufacturers and retrofitters do not yet have experience with such electrohydraulic drives, Bucher Hydraulics offers ample design support.
Bucher Hydraulics
www.bucherhydraulics.com
Filed Under: Mobile Hydraulic Tips