Mobile machines have to meet widely differing requirements. To get to a job site, they need good off-road capability. While they are working, however, high rigidity and stability are essential. Add to that are increasingly demanding safety and environmental regulations. Swing-axle cylinders are built to fulfill all these requirements.
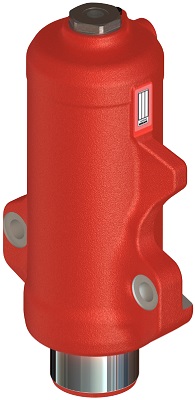
According to engineers at Bucher Hydraulics, Erding, Germany, swing-axle cylinders (SACs) are based on the principle of the plunger cylinder in which the rod serves as the piston. When open (axle unlocked), they enable a vehicle to drive over uneven ground. The undercarriage can then to a great extent follow irregularities in the terrain without individual wheels lifting up and off the ground. When closed, they lock the axle and thus ensure high rigidity during working operations.
The cylinders are designed for secondary pressures up to 600 bar (8,700 psi) and require minimal installation space. As safety components they are responsible for the stability of the mobile machine, as a malfunction can result in the machine toppling over, with disastrous consequences.
Swing axles are usually attached to the machine undercarriage, while the hydraulic power supply is housed in the rotatable superstructure. This means that the oil supply/return lines for the cylinders, as well as control signals for the valves, are routed through a swivel joint.
Bucher Hydraulics specialists simplified this SAC design in the RH series. Instead of the customary two separate lines, the developers combined pressure and control functions in one line (check valve with hydraulic release, i.e. pilot operated). The key feature: the valves open or close the flow path, depending on the pressure level. A defined pressure closes the valve. To put it another way: the oil flow fills the cylinders while pressure switches the valves. This is significantly more energy efficient than the two-line circuit. Eliminating one line also halves the pipework costs and requires only one connection through the swivel joint. The RH series can be controlled with just one inexpensive 3/2 valve.
Valving in the SAC usually consists of a pilot-operated check valve that traps the oil in the cylinder. When control pressure exceeds a certain value, a suitable area ratio within the valve lets it open against the pressure inside the cylinder. The swing axle is therefore able to move thanks to an exchange of oil between the cylinders.
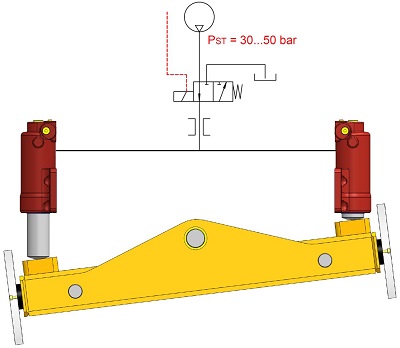
Some other systems on the market open the valve abruptly when the limit value is exceeded. This behavior carries the risk that a heavily loaded cylinder can suddenly give way, causing the machine to tilt or even topple over.
Another major safety issue is hose- or pipe-burst. Under no circumstances may it cause instability of the machine. It follows, therefore, that pressurized oil must be prevented from exiting the cylinder, or be restricted to a very slow flow rate. The type RH swing-axle cylinder ensures a high standard of safety thanks to the integral shut-off/lock valve.
Throttling for safety
The newly developed DRH (throttle check valve, pilot operated) complements the Bucher Hydraulics SAC range. In essence, it has a check valve with an additional flow-control function. The valve sits in a cartridge that’s mounted axially in the cylinder and includes the port for the hydraulic line.
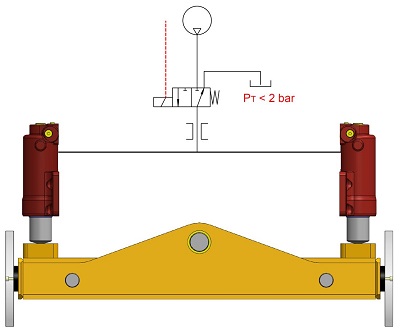
Inside the cylinder, the check valve is series-connected with a flow-control valve that throttles the outflowing oil. This throttling improves travel comfort and guarantees a safe switchover from swing mode to work mode.
Another concern is that oil compressibility and other effects can result in a settling of the machine. This creates a few millimeters of clearance between the cylinder rod and the axle pad on the unloaded side, which can lead to increased wear if the load changes.
With the DRH valve, the swing axle in locked mode can be recharged with only one line by applying a specific tank preload pressure. This forces oil into the unloaded cylinder and the piston rod then rests firmly on the axle without any gap. For the machine operator, this means stiffer and more controllable machine behavior. The integrated throttle check valve dampens any pressure peaks in the control line when the swing-axle cylinder is unlocked, thus preventing possible damage.
The valve is extremely compact and requires little installation space in the SAC body, which is a machined casting. In the event of a pipe- or hose-burst, the valve automatically closes in the locked position. It improves stability thanks to recharging in locked position and to extremely low leakage, and limiting the flow rate of the outflowing oil improves travel performance. It also features a high (25:1).opening pilot ratio. And the modular design uses a standard cylinder and screw-in cartridge valves with DIN or UNF threads, which reduces inventories and improves serviceability.
Electrified future
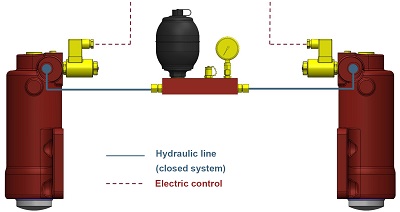
E-mobility is also making inroads into mobile machinery. At present only smaller machines use electric drives, but the trend is clear, said company officials. One way Bucher Hydraulics is addressing this need by developing the type RM cylinder. Basically, it is a closed hydraulic system, where oil just shuttles between the two cylinders. In this case, an electrically actuated valve performs the control function. The only external connection the system needs is one electrical line through the swivel joint.
Because kinematic effects may cause small stroke differences, a small oil accumulator, which also provides constant pressure, compensates for these actions. This ensures the same machine stability as with the DRH cylinder.
Among the advantages of the self-contained RM swing-axle system, no hydraulic control line to the undercarriage is required and there is no loss of pilot control oil. The cylinders are preloaded to a specific pressure, and piston rods always rest on axle pad. The system recharges itself in the locked condition. This ensures rigid and safe operation and simple control.
Bucher Hydraulics
www.bucherhydraulics.com
Filed Under: Mobile Hydraulic Tips