The 2022 Maha Fluid Power Conference was held last week at Purdue University. Katharina Schmitz, Director of the Institute for Fluid Power Drives and Systems (IFAS) at Germany’s RTWH Aachen University presented the opening keynote, “Sustainable Construction – New Challenges for Mobile Machinery.” Here are some of Dr. Schmitz’s key comments and takeaways that are of particular interest to the fluid power community.
Climate change is unquestionable. We’ve seen rising temperatures, unprecedented floods, the prospect of an ice-free arctic and the loss of coral reefs worldwide. Most scientists agree increasing levels of greenhouse gases are the culprit, and that curtailing emissions in the future is critical to limit the damage. The EU, for example, looks to achieve carbon neutrality by 2050.
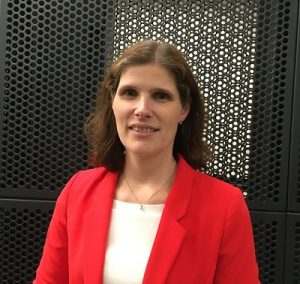
Katharina Schmitz, Director of the Institute for Fluid Power Drives and Systems (IFAS) at Germany’s RTWH Aachen University.
The building and construction industry is a significant contributor of GHG emissions and reducing emissions can have a huge impact on the global picture. Fluid power can significantly contribute to this goal.
Let’s focus on three points. Number one is the resources that are needed to produce and manufacture fluid power components and systems. Number two is to increase energy efficiency of our fluid power systems in operation. And third, to reduce the energy consumption of the whole machine or overall process.
We can talk about sustainable components, energy efficiency and digitalization. We can have smart fluid power components and systems to help us attain better energy efficiency of systems and machines and, with connected machines, help to reduce the energy consumption of the whole process. Here is bit more detail, along with some ideas from our institute on how to contribute to more-sustainable fluid power systems.
Number one, we need to think about the manufacturing of fluid power components and how the process contributes to greenhouse gas emissions. The good thing is that fluid power components have a very small carbon footprint, although we must bring that down even further. I think the carbon footprint will become a trademark of fluid power components. And perhaps there will be new business areas through certification processes to ensure components become more sustainable.
We need to think about materials currently used in fluid power components that are not good for the environment, for example, lead and lead-containing alloys. We need more research on new materials and component designs that are better for manufacturing workers and also eliminate hazards to the environment.
Another thing to think about is alternative production processes. For example, additive manufacturing offers good options for fluid power components. We should explore expanding its use to create highly integrated fluid power components that reduce losses and improve flow control.
We can improve the carbon footprint of our fluid power components, but this is only a very small part when we compare it with the energy that is used later on in operating fluid power systems. So we should focus more on the fluid power system energy efficiency.
There are some good options. When we look at a standard hydraulic system, there are lots of losses due to the valve control system. But other possibilities include decentralized systems, electrified hydraulic systems, displacement control systems and so on. This is not new, and has gained more attention for use in real machines.
A landmark research study at IFAS was the STEAM project completed in 2016. This was the first research project that was set up with the goal to research the ICE and the hydraulics together in an excavator. And this is, from my point of view, so obvious that we should look at the complete machine, and not only focus on the fluid power system or on the ICE.
Among other modifications, STEAM adapted the hydraulic system with a multi-pressure network, added accumulator energy storage and recuperation, and tuned the complete unit so the internal combustion engine runs mostly at its optimum point regardless of demand. The result was 27% less fuel consumption with no loss of productivity. This is a good example that shows we need to consider the whole machine, and not focus only on the fluid power system or the propulsion system.
In terms of energy efficiency, we have many new possibilities. There’s much talk about electrification of excavators and other mobile machinery. We still face many challenges, for example, cost effectiveness, system integration, energy storage and, of course, electric infrastructure. But we have a lot of new options now for system architectures, such as multiple degrees of freedom, decentralized systems, EHAS, high-speed drives, multi-pressure systems, and so on.
But we need to take a holistic view of the entire machine. What I see sometimes in the industry is that companies remove the ICE and install an electric drive, and leave the hydraulic system as it is. This of course makes no sense. We should not use the same hydraulic system that was optimized for the use of an ICE and now use it with electric drives. We should start over and think about the whole system.
When we talk about electrification, in recent years there has been a huge evolution in battery cost, size and capacity. And there will be more innovations and improvements in the future. But we have two options for electrified machines. We can wait for batteries to become cheaper and smaller and more available, or we could use the batteries that exist today and use less energy through more efficient hydraulic and drive systems. And I think we are in a very good position to think about the integration of hydraulics in electrified machines.
With electrification, it makes sense to also think about increasing the power density due to a speed increase. Electric motors get smaller or the power density gets higher when we increase the speed of rotation. And so at IFAS, we developed a new internal gear pump that mounts directly on a high speed electric motor and runs at 10,000 rpm. That’s just one example of how we can further increase the power density of hydraulic components on electrified machines.
Now when we talk about high speed and eliminating the ICE on an excavator, for example, we also need to think about noise pollution. The new pump design was pretty good in this regard and we can further refine it. But the human should be the focus in this discussion. We also need to talk about psycho acoustics, and how factors like loudness and sharpness affect operators and nearby workers.
When we talk about sustainability in hydraulics, we need to talk about fluids. This is a difficult discussion. Mineral oil is a very good fluid, the best that we know right now. And when we consider the carbon footprint, it makes sense to use mineral oil as producing synthetic fluids has a much higher carbon footprint. In the long term we need new fluids; for now, mineral oil remains a good option.
Thus, we need ways to make operations safer, improve productivity, and reduce energy and material consumption of machines and processes. Our vision at IFAS centers around autonomous construction processes, particularly as machines evolve and more digitalization comes to the construction site. Perhaps not in 10 years, but over the long term it will become a reality.
Right now we rely on manual operations to perform complex movements with only limited accuracy, and a lot of operator training is necessary. So assistance systems will help, especially with less-skilled workers, and ensure a safer working place toward the final goal of autonomous working machines.
Where are we right now in terms of automation? Cars already have capabilities like cruise control, lane assistant and parking assistant that can easily be put into mobile machines. There are a few more-advanced systems, like the Tesla autopilot, and research projects are moving well beyond that.
When we compare mobile machinery to cars, it’s much more difficult to detect the environment as the environment changes every minute, every hour, all the time. But we can use more sensors like radar, LiDAR and cameras to detect the surroundings, locate the machine, for example, with GPS, and then use this information to map and model our environment and the machine. And with this information, we can derive the needed action.
But, of course, complex integration and use of the data is not easy. We need to preprocess the data to combine the different signals from multiple sensors, filter them and significantly reduce the amount of data that must later be processed. Then we need to reference the data to the map. We need to localize where our machine is, and include correction signals from a reference station. And we must use simultaneous localization and mapping algorithms to constantly update for the changing topology, as well as detect objects moving about the site.
And when we talk about autonomous operation, we need to plan the tool trajectory. We have to define the starting and end points, and define boundary conditions depending on the tool and the topology, and the soil type and material. And in addition to the tool trajectory, we need to focus on the driving trajectory. It’s very complex and there are high safety requirements.
For motion control and trajectory generation, right now there are some 2D or 3D assistant functions. One example is configuration of depth and geometry by the driver with an autonomous grading assistant function. This is now widely used in practice, but it’s only a simple path control and grading control. Improvements are possible, such as trajectory adaption via environmental detection.
But of course we have a lot of challenges. We need controllers that have good accuracy and dynamics and also work with excavated materials that can be very different from rock and sand. We often use the basic PID controller, which is good for low density ground, but not suitable for, say, fragmented rocks. The advantage is it is easy to implement, but on the other hand, imperfections are possible. We can further improve controller design by, for example, compliance control and have feedback of pressure, force or both and get better results. Other ways include feed-forward controllers which give further improvements, but are more complex and could have the disadvantage of more inaccurate modeling.
What’s coming is the use of artificial intelligence methods and also reinforcement learning methods that are used right now for autonomous driving. These will evolve further and see more and more practical applications, for example, in excavating control. This is our vision of the autonomous construction process that will enable better production processes onsite while saving more energy in machinery operation.
I see enormous potential for future fluid power systems and applications. This is based on the digitalization possibilities that we have right now that we could further use in fluid power applications. Electrification will bring us new options for the driving of mobile machinery but also for stationary hydraulic applications. And we need to focus on a holistic view of the machine, and on the process that we want to develop and optimize. We should not only focus on the fluid power system, but on the overall machine. Or even better on the overall process that the machine has to fulfill.
Filed Under: News