Thanks to higher operating pressures, power density in many hydraulic systems has increased significantly in recent years. That can mean higher performance, smaller and lighter components and better efficiency, although it can also increase the susceptibility to wear and premature failures. Newer pumps and motors are built to handle higher loads and still offer long life. However, the same isn’t always true for many hydraulic fluids. That’s because the type and quality of oil has a significant impact on component wear characteristics and, with it, an ever-increasing effect on the service life and reliability of hydraulic systems.
The problem is that higher pressures put greater stress on hydraulic oils. Unfortunately, as fluid-power components and systems have rapidly evolved to meet tougher operating conditions, the standards for rating fluids have not kept pace. According to engineers at Bosch Rexroth, while pressures, temperatures and oil circulation rates have risen sharply, the minimum requirements of relevant standards like ISO 15380 and ISO 12922 do not reflect today’s higher demands for hydraulic fluids.
The result is that a high-performance circuit may run trouble-free with one fluid but quickly fail with another— even though both fluids meet the same standard.
Until now, machine manufacturers could only rely on arduous and expensive trial-and-error tests to find suitable fluids that meet their application requirements. To address that, Bosch Rexroth recently developed a new evaluation method for rating hydraulic fluids that realistically reflects higher performance demands.
The procedure examines the behavior of lubricants and the interplay in key components—the hydraulic pump and motor—under realistic working conditions, said Roland Schmidt, director of business development for construction and industry at fluids manufacturer Liqui Moly, based in Ulm, Germany. “The pump test introduced by Bosch Rexroth goes far beyond that which the current DIN and ISO standards require. Conventional tests work with 350 bar; the new standard up to 500 bar,” explained Schmidt.
As described in Rexroth data sheet RDE 90235, technicians assess the behavior of fluids and their interactions with core components under real-life conditions. The standardized procedure was initially developed and validated for A4VG series axial-piston hydraulic pumps as well as A6VM series hydraulic motors in closed circuits, as in hydrostatic drives.
The process begins with an initial break-in period, then components are subjected to high-pressure dynamic cycling where the pump and motor continuously swivel in and out. This regimen runs for 300 hours at 450 bar pressure, speeds of 4,000 rpm, and a temperature of 100°C. Next, a corner-power test gages the load capacity of components at maximum pressure and speed. It runs for 200 hours at 500 bar, 4,000 rpm and 100°C. For both segments, technicians examine shear-strain behavior, wear-protection properties and material compatibility, among other characteristics.
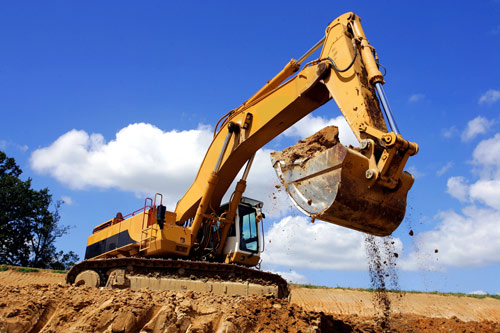
HyPER fluids are suited for demanding applications
Rating criteria are based on component weight and dimensional changes before and after the tests; material compatibility, including visual inspection of components and component surfaces; and oil analysis at the beginning, during and end of the test. From this, technicians report conclusions on the long-term running behavior of the components based on the fluid. The evaluation procedure is suited for all mineral-oil-based hydraulic media, environmentally acceptable media, as well as water-based and water-free fire-resistant hydraulic fluids. Rexroth’s RDE 90245 document shows fluids that meet all the requirements. Currently, only four fluid manufacturers make the list: Fuchs, Liqui Moly, Shell, and SRS.
HyPER oils
Liqui Moly’s HyPER products are among the first, worldwide, to meet the standard. Bosch Rexroth is a leader in hydraulic pumps and motors, and their new RDE 90235 is the toughest test available for hydraulic oils, said Roland Schmidt. “If an oil passes this test, it has proven its superiority,” he said.
“All Liqui Moly HyPER hydraulic oils are based on Group II base oils paired with a superior additive package,” he explained. “These base oils are quite new in the hydraulic area but they provide much higher cleanliness and oxidation stability compared to standard hydraulic fluids. And the additive package had to be completely redesigned as available formulations were not capable to meet the unprecedented high requirements.”
This results in long-life characteristics that, in turn, help extend equipment service life. “HyPER hydraulic oils are a great example of how you save a lot of money in the long run by investing a little more money in the beginning,” said Schmidt. For example, they reduce wear to the nonferrous metals and the nitrate layer of pistons and bores. Intervals between oil changes significantly increase. The new additive package offers better elastomer compatibility compared to other standard hydraulic fluids, which means less leakage. “Last but not least, we improved the cleanliness levels of our HyPER hydraulic oils. This will ensure from the beginning less wear and less failures of sensitive components like valves and pumps,” noted Schmidt.
Demanding applications will benefit most, he continued, but HyPER hydraulic oils are also cost-effective in standard applications. Bosch Rexroth explicitly requires hydraulic fluids that meet the new RDE 90235 for all their pumps, as the old standards are obsolete, said Schmidt. HyPER SG1 also meets Parker Denison, Eaton, and other manufacturers’ specifications.
Shell Tellus
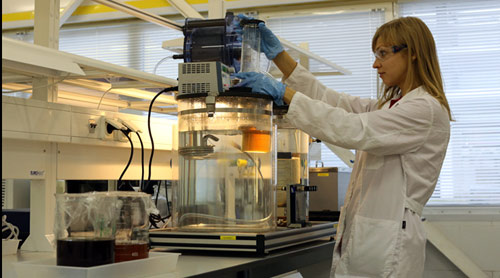
Shell testing laboratory
Shell’s new Tellus S2 MX hydraulic oils also meet RDE 90235. “Shell is always striving to help our customers lower their total cost of ownership,” explained Rob Profilet, the company’s product application specialist for industrial products in the Americas region. Bosch Rexroth developed this new approval procedure to meet the trend toward equipment operating at higher pressures and higher speeds, he said. “There are a lot of good specifications out there, but this one moves the envelope in terms of severity. It’s a difficult test to pass and we’re one of the first with the approval,” he stressed.
The fluids are designed for higher load-carrying capacity and excellent wear protection, even under severe operating conditions. Tellus S2 MX uses a Group II base oil formulation that extends oxidation life compared with previous products based on Group I base oils, said Profilet. And significantly, to meet the rigorous pump-test criteria, the additive chemistry had to be specially designed for enhanced antiwear performance while, at the same time, balance other attributes such as water-separation ability and thermal and oxidation stability.
They’re priced competitively with other typical hydraulic fluids, he said, but designed to last longer. In terms of total cost of ownership, users can extend oil-drain intervals, use and dispose of less oil over the longer term and, thanks to enhanced antiwear performance, better protect components and likely replace them less often.
“And it’s not just for demanding applications. It’s for use really across the board in hydraulic systems, anywhere you would typically use a mineral-based hydraulic oil,” said Profilet. Equipment running on Tellus S2 MX fluids can have smaller reservoirs, operate at higher loads and temperatures, and offer longer change intervals, with less downtime and better efficiency. Shell also offers a multigrade version called Tellus S2 VX, he added. It includes a viscosity index improver for operation across a wider temperature range, such as in outdoor applications. It is currently in the process of meeting RDE 90235 approval.
The Rexroth test lets manufacturers of lubricants and additives have the performance of their hydraulic fluids rated independently, regardless of the application. Suitable fluids can substantially lengthen the service life of hydraulic components and significantly lower the odds of failure. As a result, machine manufacturers and operators can better select fluids that improve reliability which, in turn, reduces their maintenance and downtime costs.
Bosch Rexroth
www.boschrexroth.com
Liqui Moly
www.liqui-moly.com
Shell Oil
www.shell.us
The post Hydraulic fluid test matches real-world conditions appeared first on Sealing & Contamination Control Tips.
Filed Under: Filtration/Contamination Control, News, Sealing & Contamination Control Tips, Slider