Hydraulic system contamination left unchecked can result in operating failure, expensive equipment damage and major downtime. There are many sources for possible contamination, from both outside and inside the system. Often, hydraulic system contamination can be prevented before it starts if the system is designed correctly to minimize and prevent contamination, according to Lih Fang Chew, global VP marketing for Quadion LLC.
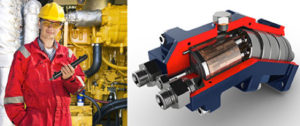
Uninterrupted, contaminant-free hydraulic system operation often requires a robust sealing solution. Using Minnesota Rubber and Plastics’ new Quniton elastomer material, sealing assemblies like that pictured is ensured due to the low CoE (<0.25µ).
“The goal of every designer should include consideration of ways to avert 90% of the sources that cause contamination,” Chew said. ”According to numerous widely published studies, these major contaminants include: water (condensation), dirt, debris and wear particles. The question for the designer is how to best prevent these materials from entering and mixing with hydraulic fluids.”
Identify potential contamination issues
It is important to start first with the requirements for the system’s sealing design and the materials needed to do the job properly.
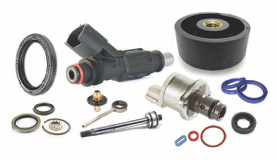
Seals molded of Quniton are designed to have a low CoF, and resist bonding or sticking to a wide range of materials in the newest, heavy-duty hydraulic systems. Lower CoF has many benefits, including enhanced product lifespan due to reduced wear and abrasion. Also, in manufacturing assembly operations, this material has unique properties, meaning less surface preparation requirements and faster assembly.
“Getting that right will prevent all kinds of downstream problems,” said Chew. “Because hydraulic fluid contamination from outside debris is often caused by the breakdown of materials used to seal the system, the material used is critically important. Wear particles (from elastomers of mating components, for example) can result from a bad hydraulic system design using inferior materials and poor manufacturing tolerances. Similarly, contamination may occur internally in the system because of sealing material incompatibility with the heat, pressures and chemical makeup of the hydraulic fluids.”
Other factors to consider in contamination are the demands of new hydraulic system designs that put a greater burden on the hydraulic mechanisms that drive and control these new products.
“Hydraulic system designs continue to be tweaked, redesigned and improved,” Chew said. “Often, the design itself has come to the point where the sealing materials used are just as important as the design when establishing reliability in an industry leading product such as a new off-highway construction vehicle. Even though hydraulic technology has existed for hundreds of years, new product designs in which hydraulic systems are used require improvement as well. Note how construction vehicles have increased in size and complexity over the years. With those changes have come the need for more complex and robust hydraulic systems to drive and control their operation. So the material used for sealing—its design formulation, configuration and manufacture—will have a major impact on eliminating contaminated hydraulic fluid.”
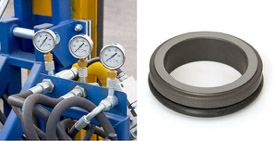
Many hydraulic systems have a unique design that requires customized seal formulation and manufacture.
Seals and sealing
While durable elastomer seals and sealing devices have been used for more than 100 years, over time the molding of these materials has become highly specialized, precise and automated. But providing an efficiently made, molded component or assembly is not always enough for the demands of hydraulic system users. For that reason, elastomer researchers and processors have designed elastomer formulas with inherent characteristics built into the polymers. These characteristics include strength, durability and flexibility.
“Over time, many of these advancements still are not enough—quality, in-field performance, liability and other concerns can also dominate,” said Chew. As a result, the manufacturing technology pushes the limits on material design including these factors:
• Characteristics of the elastomers.
• How these elastomers interact with hydraulic fluids as well as chemicals in their environment.
• Temperature tolerance in extreme heat and cold conditions while maintaining all inherent characteristics.
• How the sealed hydraulics maintain integrity and performance during use.
By Joyce Laird
The post Can fluid contamination cause components to fail? appeared first on Sealing & Contamination Control Tips.
Filed Under: Filtration/Contamination Control, Sealing, Sealing & Contamination Control Tips