Various types of contamination occur in fluid power systems: gaseous (e.g. air), liquid (e.g. water) and solid contaminants. Focusing on water, this type of contamination can be caused by moisture from ambient air, leakage of cooling systems or process water, leakage of seals and chemical processes such as combustion, oxidation and neutralization.
“Water can be present in a dissolved state and a free state (when the saturation point of the fluid has been surpassed),” explained Dan Zoller, Group Product Manager Filter Systems for
Schroeder Industries. “Either form of water is harmful to both the fluid and the hydraulic system itself. Free water needs to be avoided and removed if present. The level of dissolved water needs to be kept as low as possible/ Always follow fluid supplier guidelines to avoid cooler fluid, e.g. in the reservoir, to shed fee water due to the lower ability to hold dissolved water at lower fluid temperature.”
In order to remove water, different methods are available. “However, there are both advantages and disadvantages to all methods that must be considered,” Zoller said.
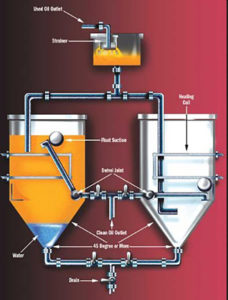
Example of gravity separation setup.
Gravity separation
Zoller said that because water generally has a higher specific gravity than hydraulic fluid (exceptions do exist e.g. HFD-R), it tends to settle at the bottom of the reservoir when given sufficient resident time in a still environment.
“In basic systems, opening the drain valve and allowing the water to drain off may be sufficient. Increasing the fluid’s temperature and employing a cone-shaped separating tank improve the effectiveness of gravity separation,” he said.
Advantage: Simple device, low cost of water removal.
Disadvantage: Only free water removed, high fluid viscosity /oxidation by-products and polar additives and impurities inhibit the effective separation of oil and water, some oils are designed to hold water in suspension rather than to allow it to separate out, takes time, need of usually two tanks and therefore double the space and oil, no gas removal (degassing).
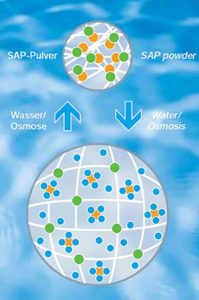
Example of super absorbent polymer (SAP).
Water absorbing elements
Super Absorbent polymer (SAP)
Conversion from free water to high viscosity gel with cross-linked polymer particles with integrated sodium ions. Osmotic pressure sucks ambient water into the polymer particles.
“Water absorption is limited by elastic memory forces of the polymer particles. The absorbed water cannot be taken out again by increasing pressure. The super absorber is not soluble in mineral oils and synthetic esters applications. A layered structure of the element prevents transfer of the polymer to the hydraulic system.”
Advantage: Can be used in standard filter housings, monitoring via differential pressure, water is not released even if pressure increases.
Disadvantage: Only free and some of the emulsified water removed, high element costs in applications with continuous water ingression, no gas removal (degassing).
Cellulose filter
Advantage: Removes some dissolved water, simple installation (like bypass filter).
Disadvantage: Limited capability for water removal per element, high element costs in applications with continuous water ingression, water is released when pressure or temperature increases, high stress on oil if continuous cooling and heating is applied, no gas removal (degassing).
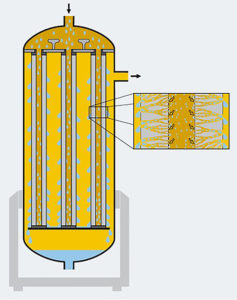
Example of a housing with coalescing elements from NYDAC/Schroeder Industries.
Coalescing elements
“Free water settles on the fibers of the coalescing element,” Zoller explained. “Droplets are transported deeper into the coalescing element by the fluid flow. Smaller drops unite to form larger ones at the fiber nodes during this process. Large water droplets are separated by gravity or with a special separation element/layer. Water is collected on the bottom of the housing (for phosphate esters on top) and it can be discharged by opening a valve.”
Advantage: High Dewatering Rates for high water contents (free water), suitable for hydraulic- and lubricating oils and diesel fuels, removes also particles in one element, high flow rates possible up to 2,000 gpm for diesel.
Disadvantage: Only free and emulsified water remove, no gas removal (degassing).
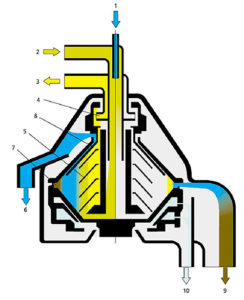
Example of a centrifuge system.
Centrifuge
“By spinning the fluid, the difference in specific gravity between the fluid and the water is magnified. Centrifugal separators remove free water faster than gravity separators. They also remove some emulsified water depending upon the relative strength of the emulsion vs. the centrifugal force of the separator. They are a good option for continuous decontamination of fluids with good demulsibility (water separating characteristics)”, Zoller said.
Advantage: High Dewatering Rates for high water contents (free water), removes larger particles due to gravity.
Disadvantage: Only free and some of the emulsified water removed, has to be adapted to viscosity range, oil viscosities of <30 cSt for good results, oil usually heated to above 90° C (could cause premature fluid aging), no gas removal (degassing).
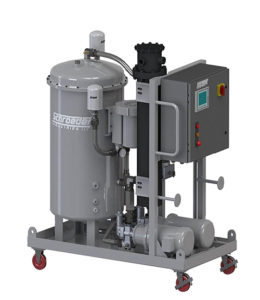
Example of a positive pressure dehydrator from HYDAC/Schroeder Industries.
Positive pressure dehydrators
“Positive pressure systems blow air through the operating fluid in a reaction chamber,” said Zoller. “Drying the air is achieved by increasing the temperature of the ambient air in a side channel blower and by getting it into contact with warmer oil. The air is introduced into the reaction chamber by a blower. The dry air takes up the water from the oil and is pushed out of the reaction chamber by the incoming air. The operating fluid is cycled through the reaction chamber by a system of two pumps.”
Advantage: Higher dewatering rates for free water compared to vacuum purifiers due to higher air flow rates, removes free and dissolved water, no expensive vacuum pump to service or replace.
Disadvantage: Less effective at high ambient humidity, less effective at high water contents compared to centrifugal or coalescing systems, no gas removal (degassing).
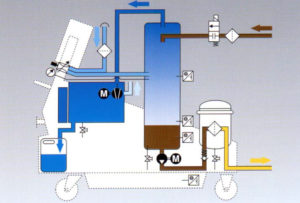
Example of a Vacuum dehydrator from HYDAC/Schroeder Industries).
Vacuum dehydrators
In vacuum based systems, a vacuum is created in a vacuum chamber by means of a vacuum pump. With the vacuum, ambient air is sucked into the vacuum chamber. The vacuum expands the ambient air and proportionately reduces the relative humidity of the air. The oil is distributing within the vacuum chamber over a large surface area, resulting in a large and thin fluid film.
“Due to the temperature increase when coming into contact with the warmer oil, the air is further dried and takes up the water from the oil. The humid air is evacuated via the vacuum pump. Depending on the applied vacuum and oil temperature, the water is evaporated (mass transfer) or boiled out (flash distillation) from the oil.”
Advantage: Removes water to very low levels even under high ambient humidity, suitable even for systems requiring lowest target levels of moisture, removes free and dissolved water, removes free and dissolved air (degassing – reduces air content in oil and therefore oxidation processes), works at relatively low oil temperature (between 40 to 60°C) that does not cause damage to the base oil or additives, will also remove other high vapor pressure contaminants like refrigerants, solvents and fuels (might require Explosion Proof unit), the dewatering requires no replacement elements.
Disadvantage: Less effective at high water contents (free water) compared to centrifugal or coalescing systems, higher initial cost and maintenance required.
Comparison of water removal methods:
Notes:
1. Absorbing Elements do have a micron rating as well that is relatively high for certain manufacturers (e.g. 40 microns), but the main purpose is for water removal. Ideally, absorbing elements should be used in conjunction with particulate elements (staged filtration)
2. Some Coalescing Elements include a particulate filter portion (plea) for protection of the hydrophilic material. In order to prolong the coalescing element life time, a particulate filter can be added upstream.
3. The Centrifuge can remove some of the larger particulates as well
Conclusion
Water contamination is a continual issue. How to find the best way to eliminate or at least reduce the risk to a workable solution, truly depends on your type of system and the fluids passing through it. Rather than trial and error, he suggests that consulting an expert in the area is always the best first move to take.
By Joyce Laird
The post How do you remove water from hydraulic fluid? appeared first on Sealing & Contamination Control Tips.
Filed Under: Filtration/Contamination Control, Sealing & Contamination Control Tips