A new hydraulic powertrain may pave the way for reliable and economical wind turbines.
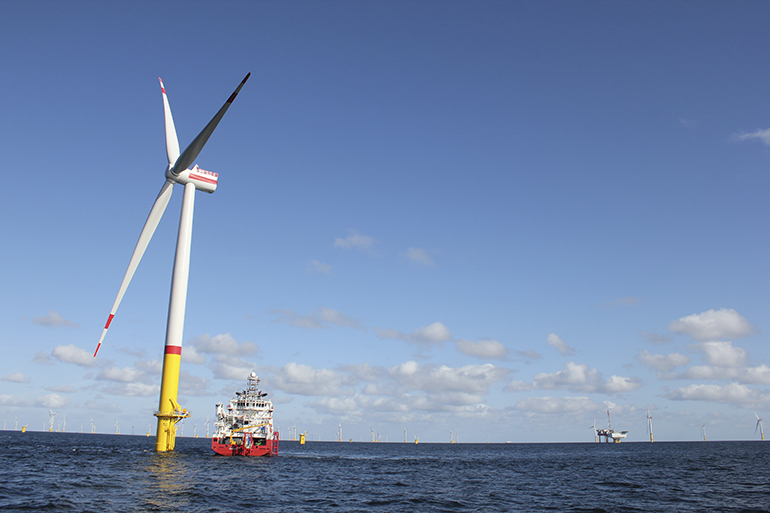
Conventional mechanical and electrical direct-drive transmissions are plagued by serious shortcomings in large wind turbines. A new hydraulic transmission offers a smaller, lighter and more-reliable alternative.
Offshore wind electricity generation has seen annual growth above 25% in recent years, as global consumers increasingly embrace renewable energy. The U.S. National Renewable Energy Laboratory predicts accelerated market growth in the next decade, with cumulative capacity rising to nearly 200 GW by 2030 and over 500 GW by 2050.
To help reach these ambitious goals, wind-turbine specialist Hydrautrans BV, based in Utrecht, The Netherlands, is looking to tap the proven benefits of hydraulics. It is developing a 12+ MW mechanical-hydraulic drive train that is said to be ideally suited for next-generation offshore windfarms.
Size matters
The rapidly expanding offshore wind market has spurred demand for larger and more powerful turbines. Ocean-based wind platforms tend to be more efficient as they get bigger, making offshore wind a more cost-effective and competitive source of clean energy. As size increases, however, it puts traditional mechanical and direct-drive electrical transmissions under serious pressure, said Hydrautrans CEO Ernst van Zuijlen.
There are major shortcomings in offshore turbines that exceed 10 MW, he explained. At these power levels conventional mechanical gearboxes are prone to breakdowns and have high maintenance requirements. That’s why the offshore industry increasingly opts for direct-drive generators. These units slowly rotate at the same speed as the rotor. But as direct-driven generators get bigger, they also bring with it an exponential increase in weight.
That makes deployment increasingly difficult. At a rated power of 12 MW, for example, the generator itself weighs around 450 tons and, with ancillary connected systems, the entire unit tops the scale at about 600 tons. In addition, the rotor and blades also weigh over 200 tons.
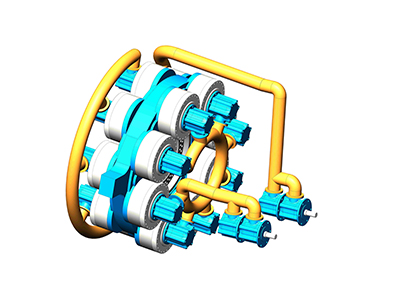
The Hydrautrans Drive Train includes eight planetary gearboxes on either side of the ring gear. Each planetary drives a hydraulic pump, and four pumps supply one hydraulic motor.
A package this heavy complicates transport logistics and installation. It requires a ship with the crane capacity to lift the entire 600-ton drive to a height of 140 m or more — all while being subjected to waves and wind forces. Successful installation is only possible with an extremely large and expensive jack-up vessel that costs about $500,000 per day.
Alternative approach
The hybrid Hydrautrans Drive Train (HDT) overcomes these challenges, said van Zuijlen. The HDT will have a capacity that exceeds 12 MW and which can be increased by adding modular units. Yet with a higher power-to-weight ratio and comparable cost per kg, it is designed to be significantly smaller, lighter and more reliable compared to mechanical and direct-drive options.
In the HDT transmission, the turbine rotor turns at about 8 rpm on the main shaft. Producing electricity efficiently means the rotational speed has to be increased to more than 1,200 rpm, he said. To accomplish this, the rotor directly drives a large ring gear that meshes with 16 planetary gearboxes. Every gearbox drives a hydraulic pump. Four pumps supply high-pressure fluid to one hydraulic motor of identical design; hence, the speed ratio is 1:4. These four motors are directly coupled to two 6+ MW generators that produce electricity. Thus, the Hydrautrans Drive Train consists of mechanical power-split and modular hydraulic systems that drive lighter, high-speed generators, compared to those in direct-drive electrical systems.
Innovative hydraulics
While hydraulics has long been renowned for its high power density, the technology hasn’t previously been used successfully in large wind turbines because traditional hydraulic pumps and motors are inefficient, said van Zuijlen. Also, metal-to-metal contact between moving parts causes friction, resistance and wear that limit performance and life.
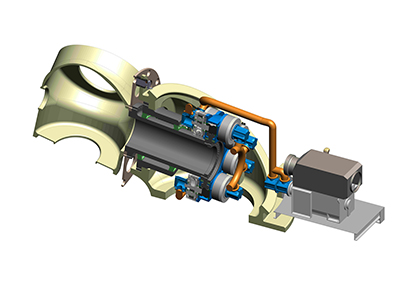
Cutaway view of the nacelle shows gearing, pumps and hydraulic motors connected to the electric generators on the right.
Now, in a breakthrough for economical renewable power generations, the Hydrautrans Drive Train takes advantage of patented Floating Cup Technology (FCT) developed by INNAS BV, Breda, The Netherlands. The FCT transmits power transmission through hydraulic forces without metal-to-metal contact. This virtually eliminates friction and wear and enables an efficiency of over 98% per pump and motor.
FCT technology is proven in smaller systems. The hydraulic pumps and motors Hydrautrans plans to use in the HDT are approximately 100 times larger in terms of volume/displacement per rotation. “That should result in even higher efficiency than FCT pumps already on the market,” said van Zuijlen.
According to Peter Achten of INNAS, the HDT’s pumps and motors have a displacement of 4,920 cc per revolution, and they are designed for a peak pressure of 350 bar. In the wind turbine application the load is mainly around 270 bar. Pumps have a nominal rotational speed of 375 rpm, which results in a peak power level of 1.1 MW. The motors run four times faster (1,500 rpm) and have a peak power of 4.3 MW. Four pumps will supply each motor, and two motors will mount in series to drive one generator. Each has two parallel low-pressure ports and two high-pressure ports.
The hydraulic units are designed with 28 pistons (2 x 14). Pistons on the left side of the rotor are positioned in line with pistons on the right side. There is no phase shift like in INNAS’s current pumps and motors. “This has a disadvantage for the noise of the units, which is not the biggest concern for large offshore wind turbines. The most important advantage is that it completely eliminates the axial load on the bearing, which makes it possible to increase the lifetime of the roller bearings to a few decades,” said Achten.
System benefits
“The high-efficiency mechanical-hydraulic system is a serious alternative to typical direct drives,” said van Zuijlen. “First of all, there’s the weight saving and related lower cost. Because of the high power density we can suffice with a lighter design. We have calculated that this can save up to 40% on weight.” Maximum hoisting weight, including the generators, is now in the 200 to 240 ton range. And the compact drive train reduces overall nacelle dimensions.
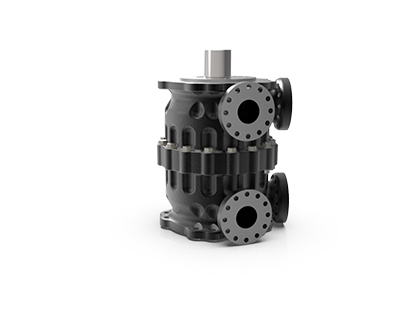
The HDT’s INNAS floating-cup pump supplies 4,920 cc per revolution of flow at a peak pressure of 350 bar.
“In addition, our drive train is modular. You can split the system in components that can be installed using cranes of 250 ton capacity. And as a result, the foundations do not have to be as large and heavy. The modular design makes installation with existing, smaller vessels feasible, saving millions,” he continued. “During maintenance, an even smaller crane can exchange parts if you have to replace a pump, motor or gearbox. All that saves on costs.”
The mechanical-hydraulic system is expected to be less complex and highly reliable. Because the HDT ring gear is directly coupled to the shaft, there is no introduction of bending moments in the ring gear due to external loads or misalignment between components. The hydraulic transmission is flexible as well, damping peak loads and limiting cascade effects of one pump influencing the others.
No wear and tear is expected in the hydraulic components as there is no metal-to-metal contact. Because radial loads are absorbed in the main bearings — not in a mechanical gear box or generator — and fluctuations in wind-loading are partly damped in the hydraulic system, maintenance requirements are expected to be extremely low.
And properly engineered, the turbine would not need to shut down should a single pump or hose fail. “In principle, partial operation would be possible,” said van Zuijlen. The entire system is designed for a 30 year lifespan.
Future outlook
The pumps, motors and complete HDT drive train have been designed and conceptually engineered. To prove out the approach, Hydrautrans and INNAS have conducted tests in collaboration with TNO, the Netherlands Organization for Applied Scientific Research; and VDL ETG Precision Technology, a specialized manufacturer of ultraprecision parts and prototypes.
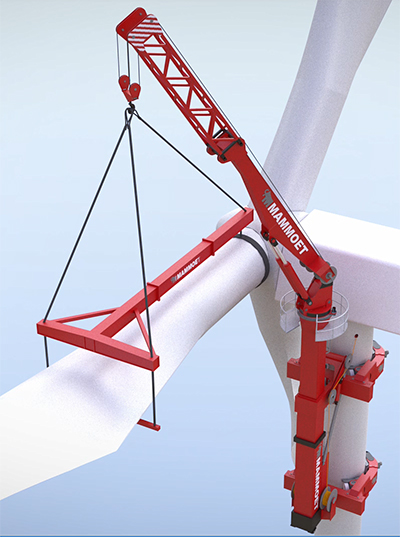
Heavy-lift engineering company Mammoet, in partnership with Hydrautrans, has developed a self-mounting crane system which can lift a load of 250 tons. It permits mounting of the 12 MW HDT without the need for a large and extremely expensive jack-up installation vessel.
The goals were to ensure the manufacturability of key components and validate performance and efficiency of the Floating Cup Technology in the HDT, which has already been demonstrated for smaller pumps operating on the same principle.
Bench tests with six sets of cups and pistons in an assembled housing running at 350 bar indicated negligible friction losses and absence of component wear and confirmed volumetric efficiency of about 99%. Further improvements are possible with additional optimization, said van Zuijlen. Testing also validated the high-precision manufacturing process.
Now that the Proof of Principle phase has been completed, VDL ETG will begin producing complete pumps and motors for prototype building and certification. “We hope to be able to have a first prototype of around 12 MW to be available in 2023,” he said.
Hydrautrans officials are currently discussing the potential implementation of HDT technology with wind-energy OEMs. The hurdle is to not only convince offshore wind turbine manufacturers of the viability of the HDT and the underlying economic benefits. Turbine builders are also reluctant to abandon their multi-million dollar investments in current direct-drive technology. “They are interested but also hesitant, because it means a major change in the approach of their design,” said van Zuijlen.
He expects similar to lower costs compared to traditional gearboxes as serial production begins, although no comparable gearboxes are available on the market. But taking into account all aspects of manufacturing, installation and maintenance, he predicts lifetime costs per kWh (LCoE) can be reduced by 4%.
“At the end of the day our system can push the boundaries of what is technically possible. The hybrid drive train has a modular design and can be scaled up relatively easily up to 15 to 20 MW. Then the drive train is not the limiting factor but, rather, other components like the rotor blades,” he said.
Hydrautrans
hydrautrans.nl
INNAS
innas.com
Filed Under: Fluid Power World Magazine Articles, Pumps & Motors