Hydraulic hoses may appear clean upon arrival in your facility, but every step of the hose fabrication process creates internal contamination that needs to be removed.
For instance, they may have contamination from the manufacturer — residual mandrel lubrication may still be inside the hose. Additionally, unless they are sealed from manufacture to your shelves, hoses may have picked up dirt and debris during transport.
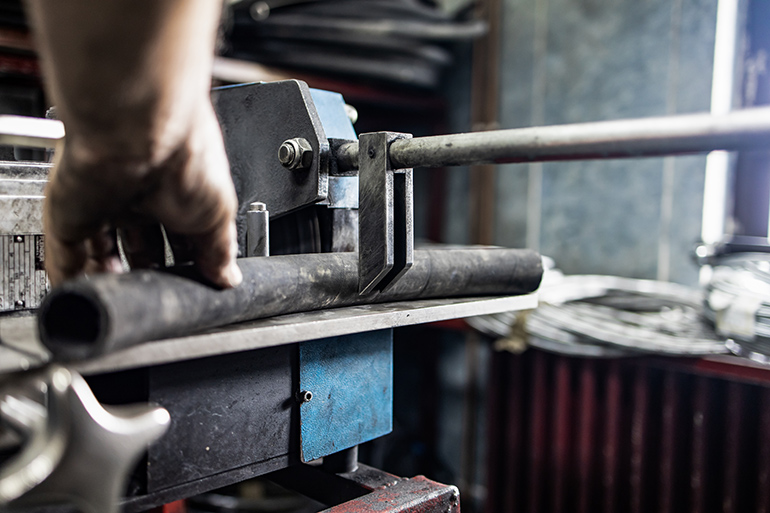
But once at your facility, three main reasons exist as to why you should clean your hydraulic hose assembly. This step is crucial more so today because hydraulic systems are more sophisticated than what they were in the past, featuring tighter clearances and running at higher pressures.
Although it is not recommended, many users will use an abrasive wheel or a metal scallop blade which will create internal contamination. It is better to use a production saw or one specifically designed to cut hose, because there will be less contamination and heat generated.
However, you should clean the hydraulic hose immediately after the cutting process and always before completing hose stem insertion. Note that as the blade cuts through the hose, it will generate heat. The rubber and metal particles that are sheared off during the cutting process will cool inside the tube, and these will have a tendency to stick or adhere to the tube. It is therefore important to clean the tube while it is still warm as contamination is easier to remove before it adheres to the inside. For example, if using projectile cleaning, you should fire the projectiles through immediately after the cut.
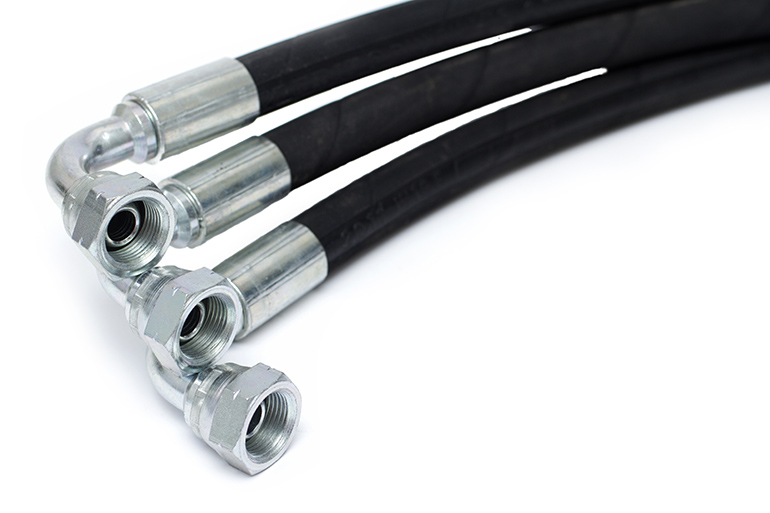
Secondly, cleaning makes hose stem insertion easier. Contamination can create friction when pushing the hose stems in. Cleaning the hose tube can create a somewhat lubricated or polished tube, making hose stem insertion easier. This also reduces the need for lubricating the hose stem, which can also introduce contamination into the hose assembly. Many lubricants are contaminated out of a brand-new container because they are not prefiltered. Another problem with lubricants is you never know whether they’re going to be compatible with the tube stock in the hose. If noncompatible lubricant is used, it could soften the tube and shorten the life of the hose assembly.
Finally, if contamination is left at both ends and hose stems are inserted, some of the contaminants will be pushed deeper into the hose, and other particles will get trapped between the O.D. of the stem and the I.D. the rubber tube. After the crimping process, the trapped contaminants — depending on the amount and the size of the particles — can create a leak path for the hydraulic fluid when the system is under pressure. That can basically be avoided by having a clean tube and doing the proper hose stem insertion.
Filed Under: Hose & Tubing, Hose Assembly Tips