From their humble hand-operated beginnings to IoT-enabled machines, hydraulic hose crimpers are a critical piece of equipment that any fluid power user should understand.
By Josh Cosford, Contributing Editor
You’d be hard-pressed to find anyone in this hydraulic industry who has never made a hydraulic hose assembly. Hydraulic technicians make their livings fabricating plumbing of various configurations. Still, even designers and engineers likely got their hands dirty in school as part of an intro class on the subject. More often than not, fluid power professionals cut their teeth in the local hose shop before moving through the ranks of a distributor or manufacturer. Nevertheless, many of you now reading this are familiar with the techniques used to crimp a hydraulic hose.
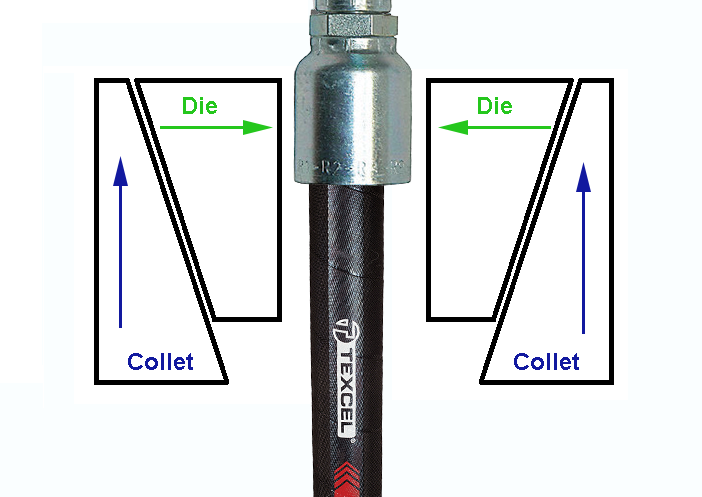
As you’d expect, hose crimping equipment originated with humble beginnings. Any machine capable of exerting radial force upon the outside diameter of a hose-end ferrule would do the trick. Early on in their designs, engineers took advantage of the cone and seat arrangement for the crimping dies, a system still most popular today. The collet acts as a seat, and when it pushes against the cone shape of the dies, the dies are forced inward (see figure 1).
Hand-swagers came first
So long as you could push either the dies or collets to achieve the desired inward force vector, the conical shape offers a mechanical advantage to aid in the compression of the hose end ferrule. The first hose crimping technology used good old-fashioned human power to achieve the desired result. Early swaging presses operated by turning a large T-handle, rotating a machine screw through a fixed head, forcing the end against the two-piece die set.
In the case of these portable hand swagers, the dies move downward against the fixed collet, and as the dies move downward, they also compress inward. The technician must hold the hose end carefully with one hand as they spin the handle with the opposite hand. Once the dies grasp the fitting firmly enough, the technician then uses both hands to muscle the crimper until it bottoms out. It’s essential to use only the matching dies and hose ends specific to the application.
These portable hand-operated units don’t offer the same automatic crimp diameter technology as new systems employing micrometers. You simply clamp the unit until the two-piece dies bottom out and hope you achieve your crimp spec. Measuring the crimp still offers the technician confirmation that the crimp resides within specification, but they need to count on their experience with the device to produce consistently accurate results. I should also mention, many technicians still use portable hand-swaging machines today.
Hydraulics add speed and power
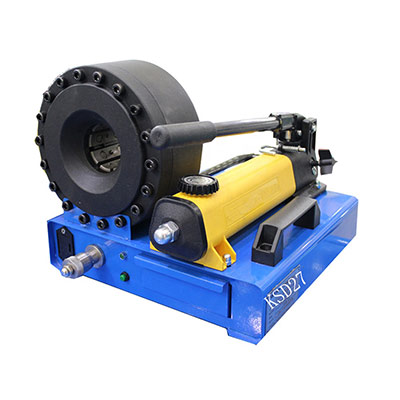
Something is satisfying about a hydraulically powered hose crimping machine. An all-electric machine just doesn’t feel right, like a meatless burger or a Mazda Miata with an automatic transmission. The addition of hydraulic power density to the crimping machine offered the technician a quicker and more powerful method of crimping hose ends. The collet on the hydraulic crimper is essentially an annular hydraulic cylinder. In some cases, two cylinders push on such an annular ring. The force created from the cylinders pushes either the collets or dies, forcing the latter to close upon the hose end with high force.
The primary difficulty with early crimping machines was their lack of versatility. The dies used were specific to the hose end, encouraging the technician or hose shop to use only products sourced from the same manufacturer. If a shop wished to use various hoses and ends, a method to vary the crimp diameter had to offer variability in the crimp OD while still offering accuracy down to the thousandths of an inch.
Rather than limit the technician to fixed diameter dies, instead offering dies capable of a range of internal diameters brought in that variability to allow multiple types and sizes of assemblies. Instead of an exact diameter of, say, 0.733 in., the dies now offer a range from 0.700-0.788 in. for example. What could previously only crimp a ½ in. hose end may now crimp 1- and 2-wire hose from 3/8 to ½ in.
Dies designed for variable diameter applications present the challenge of accuracy, of course. The dies can only bottom out on their smallest setting, which may not always be helpful for any hose or fitting the shop offers. Crimp machine designers had to engineer a method to stop the crimping procedure at the desired size accurately. No technician is skilled enough to stop the hydraulic pump by feel with 0.002 in. accuracy or better.
Accurate and repeatable
Installing an adjustable limit switch offered the most accurate and repeatable solution to the variable die set. An adjustable micrometer attached to the limit switch allows the technician to set the depth of the limit switch to within a thousandth of an inch or less. When the crimp actuator contacts the limit switch, the pump stops automatically. So long as the micrometer has been calibrated, the crimp diameter is both accurate and precise for every single operation.
Hydraulic crimpers using the micrometer were the standard for decades, offering precise control to make hose assembly quick and straightforward. Much of the advancement, until recently, has been improvements to the practicality of the machine. Dual-stage hydraulic pumps provided the technician with rapid die travel until the clamping pressure was met, where the stages switched to the smaller, high-pressure pump for maximum force.
Convenient die storage systems to offer rapid and precise tooling changes also sped up the pace for busy hose shops changing between sizes. A die-set loader offered the technician ease of pulling dies from their holder where they’re inserted into the crimper before being clamped in place. The tidy die storage and replacement systems so widespread today beat the old habit of sifting through drawers or bins where every die of every size mingled with no organization.
Electronic control
Just as the rest of the industry moved towards electronic control, so too did the hose crimping machine. Some technicians found the traditional dial-micrometer hard to read and adjust, and often found itself out of calibration. Linear position sensors replaced the limit switches, and then the adjustment option went digital. A small LCD screen shows the crimp setting, which increased accuracy and reduced the chance for error. The precision of the linear transducer all but guarantees perfect, repeatable crimps.
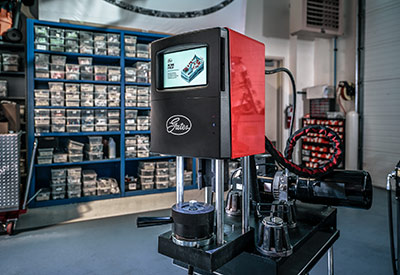
Some hydraulic hose assembly equipment manufacturers have produced semi-automated hose assembly stations. One such machine requires only that the operator load the parts into the machine. The operator loads the stems and ferrules separately, two at a time, and then inserts the hose ends into the machine. The operator starts the sequence that inserts the stems into the pre-cut hose ends along with the ferrules.
The operator unclamps the hose assembly, and if it’s long enough, simultaneously inserts each end into the automatic crimper. A moment later, the technician pulls out a complete hose assembly. If the hose length isn’t long enough to span the gap and into the two openings, the ends are done individually but in parallel. The insertion and crimping functions are completed while the technician works on the opposing operation. Capable of two hundred complete hose assemblies per hour, this machine quickly offers a return on its investment.
Crimpers get smart
The industrial world continues to find new and creative ways to utilize Industry 4.0 concepts, and hose crimping technology is no different. Busy hose shops require speed and versatility, leaving little time for thumbing through catalogues looking for crimp specs. Many top crimp manufacturers offer high-end machines with touch screen HMIs employing wireless links to the manufacturer database.
This system might not be impressive for the technician who has memorized the crimp specs for their standard 100R1 or 100R2 assemblies. But when they’re asked to crimp various assemblies of stainless wrapped thermoplastic hose, they’ll be elated to know the required die information pulls up on the touchscreen. A quick selection of hose, dash size and stem results in readily available crimp specs populated right into the crimper settings.
Just like the fluid power industry at large, crimping technology will continue to advance. Expect to see augmented reality identify the hose and fittings visually, such as with QR codes, then automatically populate crimp specifications. Expect hydraulic hose crimping technology to become more versatile, more productive and more easily maintained.
Filed Under: Hose & Tubing, Hose Assembly Tips