Increase efficiency and effectiveness by choosing the right pneumatic control or regulation product for accurate, repeatable results.
By Mindy Schoeff, Marketing Communications Manager, Proportion-Air
Facilities that manufacture packaging products, or those that do the actual packaging, are no strangers to pneumatic control. Whether pressing a product, filling it, conveying or moving materials, testing or sealing, pneumatics can be an effective solution with advantages for many applications, especially those where cleanliness and safety are paramount.
Because pressure is the force applied over a specific area, it’s not uncommon for force to be the specific variable that manufacturers wish to control. Many packaging applications fall into this category. Controlling multiple forces using a pneumatic cylinder is a common automation requirement. Force can be precisely calculated by knowing the cylinder’s effective area and the pressure being exerted on the cylinder to achieve repeatable force control.
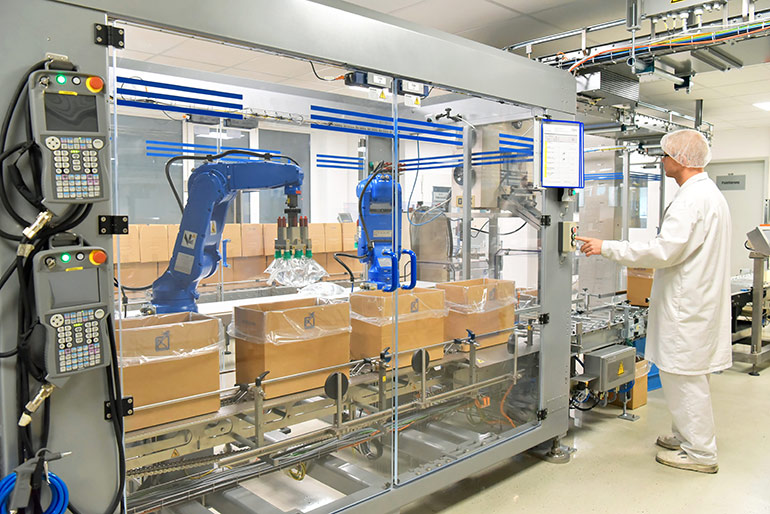
All images courtesy of Proportion-Air
Cylinders aren’t the only feedback device in force applications. Depending on the application, springs, brakes or actuators may play a role. Some applications require that a load cell be used for closed-loop force control. Proper regulation of the compressed air or gas in the process is always essential.
Applications of force in packaging
From manufacturing packaging materials to sealing the final product, regulating the force applied to the process is key for a successful result. Providing accurate, repeatable force ensures consistent product volume when filling packages. Underfilling and overfilling packages present problems with customers at any step of the manufacturing process. An overfilled package wastes product and can interfere with packaging material integrity. Underfilled packages are a waste of packaging material, process time, and can lead to customer dissatisfaction.
Packaging volume is regulated in many circumstances, especially in food and pharmaceutical industries. Ensuring that the amount of product in the package matches the label is critical.
Regulators also come into play when transporting products on conveyor belts throughout a facility. Accurate pneumatic regulation can ensure product stability and prevent damage during transport. The regulator’s role is to control pressure to provide a gentle, but firm, grip on products as they move along the conveyor.
Pneumatics can also shine in sealing applications by controlling force to create a secure, leak-proof seal. An accurate, repeatable regulator ensures even and consistent pressure on sealing surfaces.
Press machine force
Press machines are common in many packaging facilities. They can function in many ways, from forming and shaping materials to embossing and impressing.
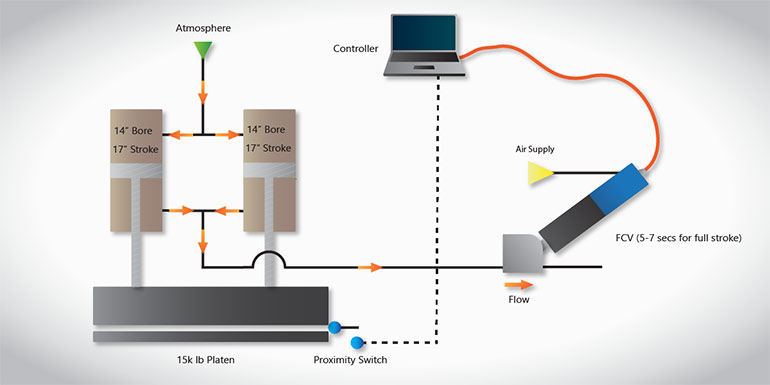
In the press machine force control application pictured in Figure 1, a Proportion-Air FCV flow control valve determines the deceleration of two cylinders with a 15,000 lb platen attached. As the platen is lowered, the proximity switch sends a signal to a controller, which then controls the FCV. The FCV meters the air flow during the last 3 in. of stroke to eliminate platen bounce.
Numerous industries employ press control force applications and require the use of pneumatics. Presses using pneumatics are suited for food-grade processes, where a hydraulic solution may run the risk of contamination, speed or safety concerns. Pneumatic presses are generally faster and cleaner than their hydraulic counterparts.
Using a cylinder to control force for indexing
Another example of pneumatic control in packaging is bag indexing, Figure 2. This sketch shows a Proportion-Air electro-pneumatic pressure controller being used to control force on a bread bag indexing cylinder. A single-loop electronic regulator maintains just the right amount of force so the bags come off the stack, one-at-a-time.
Because regulators like these constantly sense downstream pressure, they react very quickly to any changes in load to relieve or add pressure (force) to the process.
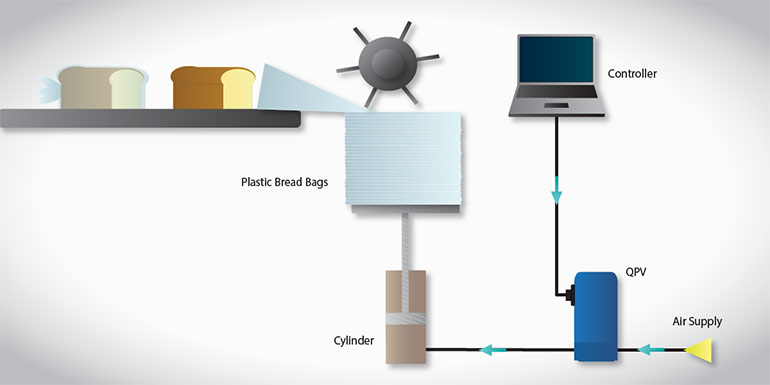
If faster and more accurate control is required, a double-loop regulator can accept direct feedback from a load cell. This allows direct control of the force in a process without the need for additional PID tuning, making it basically a “plug and play” application.
Advantages of electronic pneumatic control
Engineers have many options for controlling or regulating pressure, or more specifically force, in packaging applications. When high force is required, a hydraulic solution is likely. The requirements of packaging processes often give pneumatic options an edge. Pneumatics is often cleaner and faster for short distances than hydraulics. Because compressed air is usually the medium, safety concerns regarding leaks are limited.
Electronic pneumatic control offers several advantages over manual pneumatic or hydraulics. Automating a process and having near real-time pressure and force data enhances process control and monitoring. The accurate, repeatable performance of proportional electronic regulators can help improve and maintain product quality and consistency. Increased production efficiency and reduced waste are possible by minimizing product damage or rework.
Closed-loop electronic regulators can also simplify the entire process. When a load cell is required, the load cell’s output can be sent directly into a dual-loop proportional regulator as second loop feedback. A regulator with second loop feedback does the loop closing for the application — it compares the controller’s command signal input with the signal output from the load cell.
The benefit to the user is that PID loops no longer need to be tuned and response is real-time. The analog monitor signal from the regulator comes from the customer-supplied load cell and can be used for data acquisition.
Selecting the right electro-pneumatic regulator for precise control
While many packaging processes appear simple, several factors go into the selection process for proper pneumatic regulation. Knowing the incoming media pressure as well as the desired pressure is critical, as is knowing if the system is static or under flow, and what the flow rate is. Providing target accuracy and response times also gives a supplier information needed to choose the most suitable product.
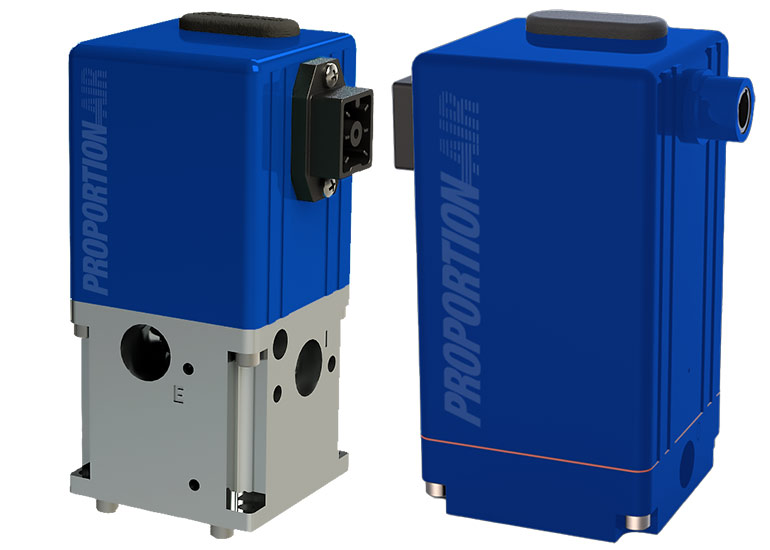
For electronic control, sharing information about the input, or command, and output, or monitor, signals being used in the system is also important. In addition to standard 4-20 mA or 0-10 Vdc signals, options like RS232, RS485 or proprietary protocols are available.
Proportion-Air offers several smart parts for regulators or flow control devices that provide accurate, repeatable force control. With the QBX, a standard electronic proportional pressure regulator, an accuracy of ±0.2 percent of full scale and a repeatability of ±0.02 percent of full-scale calibration provides very precise force control. For high flow requirements, the QB3 and QB4 have integral volume boosters, handling flows up to 30 scfm and 200 scfm respectively.
Using closed-loop proportional regulators with electronic control provide accurate, repeatable results for packaging applications. Combining the clean, safe and fast characteristics of pneumatics with the ease of automation of closed-loop electronic regulation offers a winning solution when controlling force is required.
Proportion-Air
proportionair.com
Filed Under: Air Preparation, Air Preparation & Regulation, Components, Components Oil Coolers, Pneumatic Tips