Several important trends are affecting the world of fluid power and, specifically, hydraulic power units. According to Axel Schwerdtfeger, CTO of HAWE Hydraulik, based in Munich, Germany, one important area involves digitalization and connectivity in systems. Also, electrification of mobile machines is on the rise, and thus miniaturization and decentralization of power packs — bringing force capabilities right to where it is needed — is a growing trend. And energy efficiency has become critical, not only in the mobile market but also in industrial settings, he said.
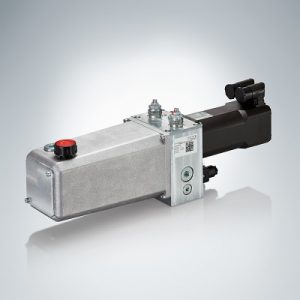
The HAWE Hydraulik HS 120 servo power unit is compact, efficient and highly dynamic. It provides volume flow rate of 8.9 lpm at pressures to 150 bar.
When a machine’s hydraulic system must fit into a limited installation space and provide quiet operation, highly dynamic and precise control of position or pressure to the actuators, along with energy efficient operation, design engineers are increasingly turning to compact, servohydraulic power units (HPUs) as the preferred option, said Ahmed Wasel, a HAWE application engineer.
For example, consider a servo HPU such as the HAWE HS 120, a compact power unit with maximum volume flow rate of 8.9 lpm and pressure capability of up to 150 bar. According to Wasel, a conventional HPU with comparable ratings needs a 750 W asynchronous motor that measures 160 × 269 mm and weighs 10 kg. In contrast, the HS 120 has an 820 W servo-synchronous motor that measures 90 × 196 mm and weighs only 4 kg — resulting in almost a 70% volume reduction and 60% weight savings.
And because of the type and size of the motor, the system is also more dynamic, said Wasel. To understand why that is important, consider a quick comparison between the different types of hydraulic power units. A classical system with an asynchronous motor running at constant speed is for systems where actuation is controlled solely via a valve block. No motor dynamics are required. The next step up is units with an asynchronous motor and a frequency converter that permit variable-speed operation. Actuation is realized through the valve block and the motor/pump unit. This system offers mid-range dynamic characteristics, said Wasel.
Finally, units with a servomotor driving the pump at variable speeds offer the most dynamic characteristics of the three, as actuation is via the motor-pump combination. In the HS 120, “That means we can reach the highest speed of the motor, and hence the maximum volume flow rate, in only 100 milliseconds. And we can change the flow direction between the different ports in 150 milliseconds. Even sport cars cannot reach these speeds,” said Wasel.
That also plays a significant role in terms of energy efficiency, he continued. In a conventional hydraulic power unit, the valves have just one mission: to throttle the volume flow rate and deliver only the required amount to the actuator. “The rest will go to the tank through the pressure relief valve, generating heat and energy losses,” he explained.
Compare that to the HS 120. “Operating dynamically, the servo motor-pump unit delivers oil to the cylinder only when it’s needed, which means we don’t have major losses through the valves and thus no big increase in the oil temperature, like in conventional hydraulic power units. This also means that we can install smaller tanks.
“So, energy efficiency is realized through three advantages. We don’t have valves between the motor pump unit and the cylinder and therefore no flow losses. We deliver oil with the exact required volume flow rate so there are no heat losses through throttling. And finally, the hydraulic power unit delivers volume flow rate only when it’s needed, which we call ‘power-on-demand,’” he said.
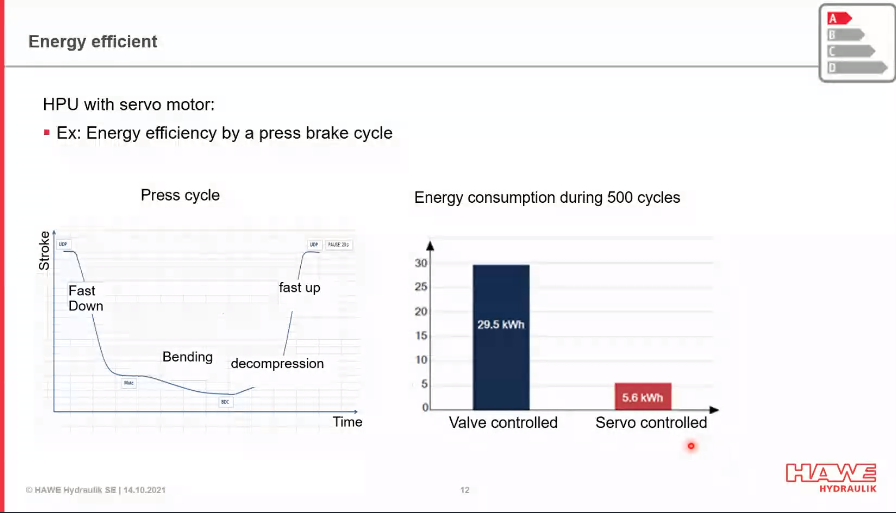
In a press-brake application, a conventional valve-controlled hydraulic system consumed about 29.5 kWh over 500 cycles. The HS 120 servo system needed only 5.6 kWh, an 80% energy reduction. The latter also ran up to 15 decibels quieter.
How much energy can a servo HPU system save? In one typical case, HAWE engineers compared two nearly identical press-brake machines, except one relied on throttle or valve control; and the other had servo control. The valve control system consumed about 29.5 kWh over 500 cycles, while the servo system needed only 5.6 kWh, which meant an 80% energy reduction. The same holds for noise reduction in the press-brake application, where the servo system operated up to 15 decibels quieter.
Various options let users tailor the HS 120 to fit specific application requirements. For instance, measurement connectors allow for pressure sensors and switches; servomotors are available in two different power ratings; seated valves can lock pressure in one or both ports; and a connecting block for pipe connections can be ordered separately. The reversible, external gear pump located inside the tank comes in six different sizes. And the HS 120 has a one-liter compact tank with oil level and temperature monitoring. The HS 120 power unit can be delivered as a complete product. Or it can be shipped without a motor for customers who prefer to specify their own servomotor and driver.
The HS 120 is a proven workhorse in numerous applications. For instance, in machines where textile sheets with warps or deformation must be straightened by passing through sets of rollers, the hydraulic unit applies the requisite force to the product while controlling reactions speeds on the rollers at up to four meters per second and supplying pressure within 100 to 150 milliseconds. In injection molding machines, the HS 120 can operate parallel cylinders at different speeds to satisfy tasks like fast closing, clamping or working speed. This lets each injection molding machine perform specific and different processes according to customer requirements.
The HS 120 is compact, highly dynamic and has a simple design, and the robust unit has exceeded more than 10 million cycles in applications like injection molding. It also requires no additional cooling thanks to power-on-demand and excellent energy efficiency.
HAWE
www.hawe.com
Filed Under: News, Pumps & Motors