By Ron Marshall
Improving the efficiency of your air compressor system doesn’t always require a large investment. Small, cost-effective changes can lead to significant energy savings, reduced operational costs, and a longer system lifespan. Here are five practical and low-cost strategies to boost the efficiency of your air compressor.
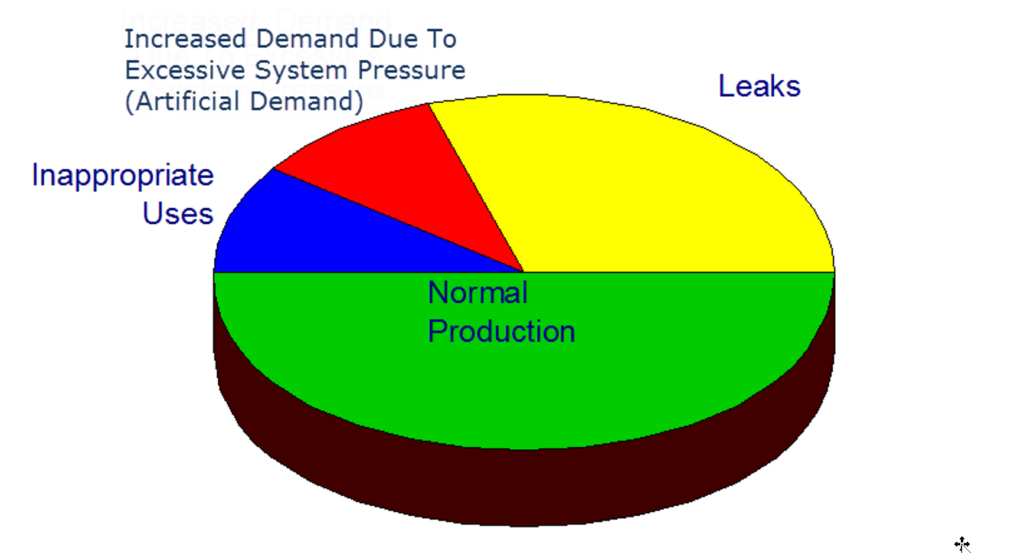
- Fix leaks
Air leaks are one of the biggest culprits of wasted energy in compressed air systems. Even a small leak can cost hundreds of dollars annually in energy loss. Conduct regular inspections using tools like ultrasonic leak detectors or simple soap bubble testing to identify leaks in pipes, fittings, and connections. Promptly repairing these leaks can dramatically improve system efficiency and reduce operating costs. - Lower system pressure
Many systems operate at unnecessarily high pressures, wasting energy. Reducing the system pressure to the lowest level required for your processes can save up to 1% of energy for every 2 psi of reduction. Evaluate your equipment’s actual pressure needs and adjust settings accordingly, ensuring you avoid over pressurization without sacrificing performance.
- Perform regular maintenance
Basic maintenance tasks — like replacing clogged filters, cleaning intake vents, and checking lubrication levels — can make a big difference in efficiency. Dirty filters force the compressor to work harder, increasing energy consumption and wear. Scheduling regular maintenance helps ensure your compressor runs smoothly and efficiently.
- Eliminate misuses of compressed air
Compressed air is often used for tasks like cleaning or cooling, which can be accomplished more efficiently with alternative methods such as blowers or electric tools. Identifying and eliminating these non-essential uses reduces demand on the system, saving energy and reducing unnecessary strain on the compressor.
- Optimize air storage
Proper air storage can stabilize your system by handling fluctuations in demand without overworking the compressor. Adding or upgrading an air receiver tank can minimize pressure drops and reduce compressor cycling, leading to smoother operations and lower energy use.
By implementing these simple and affordable strategies, you can make your air compressor system more energy-efficient, cost-effective, and reliable. These small changes can have a big impact on your bottom line while promoting sustainable industrial practices. If you would like to know more about low cost/no-cost solutions that can gain between 10% and 30% energy savings, then consider one of Compressed Air Challenge’s training sessions. A link to our course calendar is here.
Filed Under: Air Compressors, Air Preparation, Components Oil Coolers, Compressed Air Technologies, Engineering Basics, Pneumatic Tips