Manufacturers across all industries seek ways to electrify, digitize, and automate their systems to decrease costs and increase efficiency. Electro-pneumatic pressure regulators and valves enable such efforts while improving pressure and flow rate accuracy.
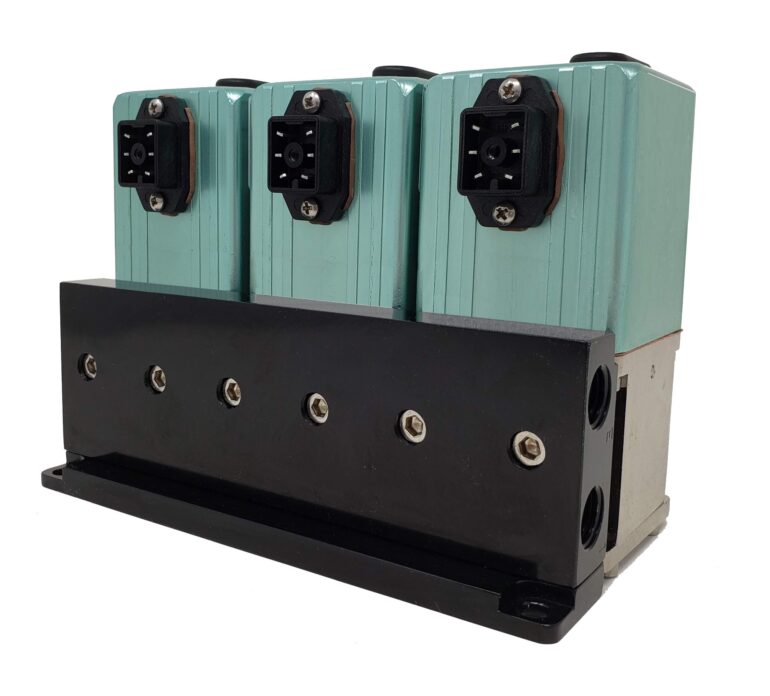
Back in the day, there were only manual pressure regulators that relied on the skill and precision of the human hand. With a delicate touch and some trial and error, the correct setting was found and never to be adjusted again. Then came electricity, which prompted I/P and E/P regulators that converted current and voltage to pneumatic pressure to achieve more control within a system. But in time, engineers recognized that not all systems had consistent supply pressure and that complex applications required variable pressure ranges. As such, the electro-pneumatic pressure regulator was born to provide real-time feedback and more accurate, automated control.
Here are five applications in which electro-pneumatic pressure regulators and valves improve accuracy and control in pneumatic systems.
Leak testing for quality control
Pneumatic testing is used to ensure functionality and determine the limitations of equipment, such as pipelines. It can also be used for quality control to check for leaks in closed-system devices. Whether using pressure decay, vacuum decay, pressure cracking, chamber, burst, or bubble testing methods, pressure regulators are essential to control the amount of pressure applied to the system or device being tested.
For instance, in medical manufacturing, IV bags must undergo accurate leak testing, especially around the seams and ports, to ensure the fluid inside is contained. Manufacturers often use two devices for this process: one for positive pressure and one for vacuum. However, pressure regulators such as Proportion Air’s QB3 are designed as a single unit that performs both functions.
As shown in Figure 1, the controller sends a signal to the QB3 to command the air pressure applied to the bag. Then, the regulator applies positive pressure to fill the bag with test gas. A small valve isolates the bag, and the system monitors pressure for a set period to verify that no leaks exist. Once the test is complete, the controller sends a signal to the QB3 to apply a vacuum, and the gas is voided. This same principle can apply to any leak test where an item needs to be filled and then fully exhausted.
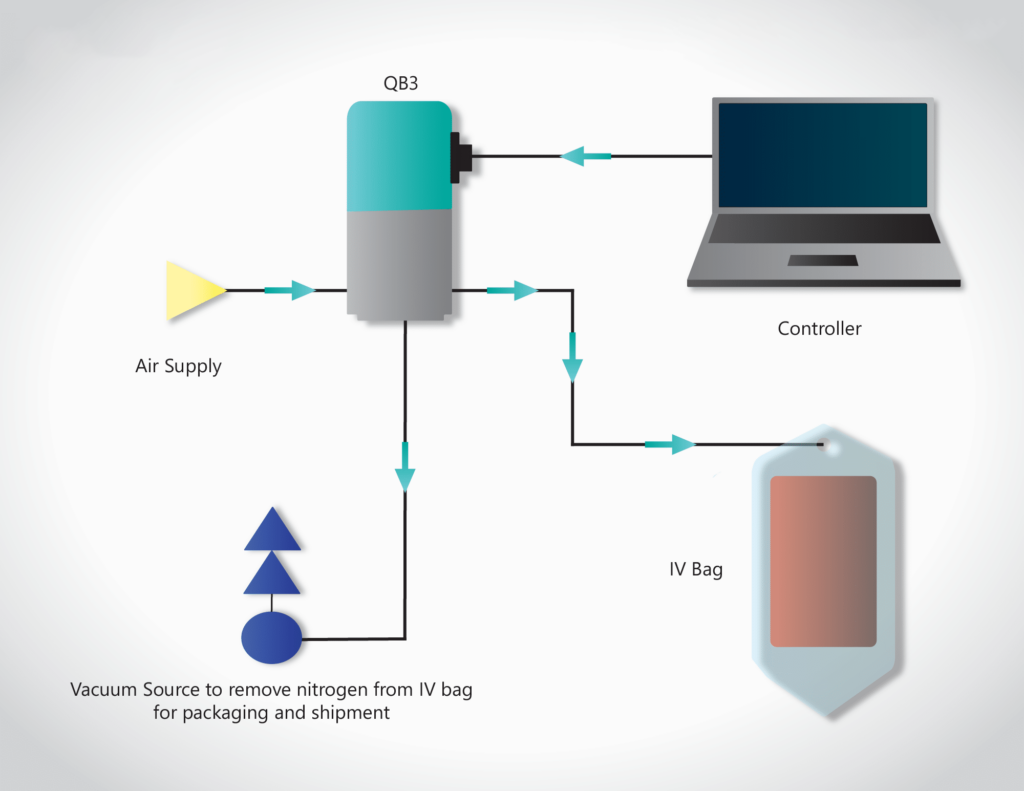
“Filling the bag to an accurate pressure and evacuating to an accurate flow is important,” said James Spence, business development manager at Proportion Air. “A separate pressure sensor is not required to verify pressure when using a proportional electronic pressure controller for applications with extremely tight tolerances. Pressure is held at the necessary level and actively measured by a flow transducer.”
Hollowing injection molded parts
Gas-assisted injection molding is another example that works similarly for glass or plastic parts. The process partially fills a mold with material, then injects an inert gas to push the material into the mold’s voids and create hollow areas in the part, reducing part weight without compromising strength. This application benefits from a double-loop pressure control assembly, where output pressure measurements can be returned to the regulator to ensure the correct pressure.
For example, in Figure 2, the double-loop assembly consists of a QB2X electronic pressure regulator, air volume booster, and DSTY pressure transducer to ensure tight regulation. The QB2X regulator pilots the air volume booster, allowing additional gas flow to the application. The DSTY transducer measures the output pressure of the air volume booster and delivers second-loop feedback to the QB2X, which adjusts the air volume booster pressure accordingly.
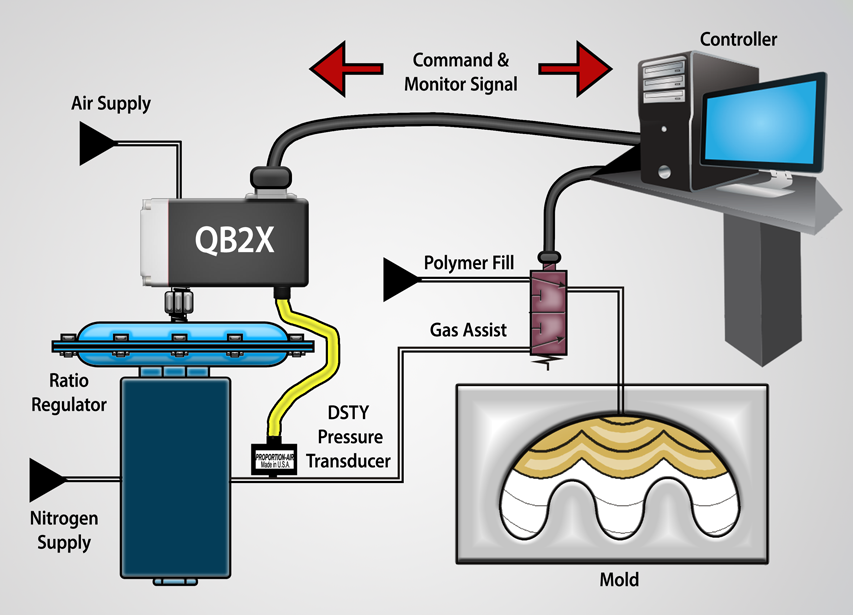
“While an assembly may look complicated, they’re basically plug and play,” said Spence. “Ours are closed-loop devices with no PID loop required. The units come from the factory calibrated and ready to hook into a system without complicated programming. They also aren’t prone to drift. If you see drift, check the system for plumbing leaks, wiring, and electronic signal levels. Always verify measuring equipment before recalibrating.”
Preventing over-pressure and instability
An electro-pneumatic regulator’s output pressure is easier to control when its supply pressure is close to its desired output. When there is a high-pressure differential between supply and output, the inlet valve may not operate fast enough to prevent significant setpoint overshoot and instability. And repeated or sustained over-pressure can lead to sensor damage.
Over-pressure is a concern in sensitive applications that require precise pressure regulation to fill small volumes. Such applications benefit from an additional miniature regulator that controls the supply air before it reaches the electro-pneumatic pressure regulator. This is especially true when dealing with inches of water column or other small values.
Figure 3 illustrates the SaveAir miniature regulator lowering the air pressure into the QB1X electro-pneumatic regulator to a preset limit, protecting the internal sensor from over-pressurization and reducing overshoot or instability.
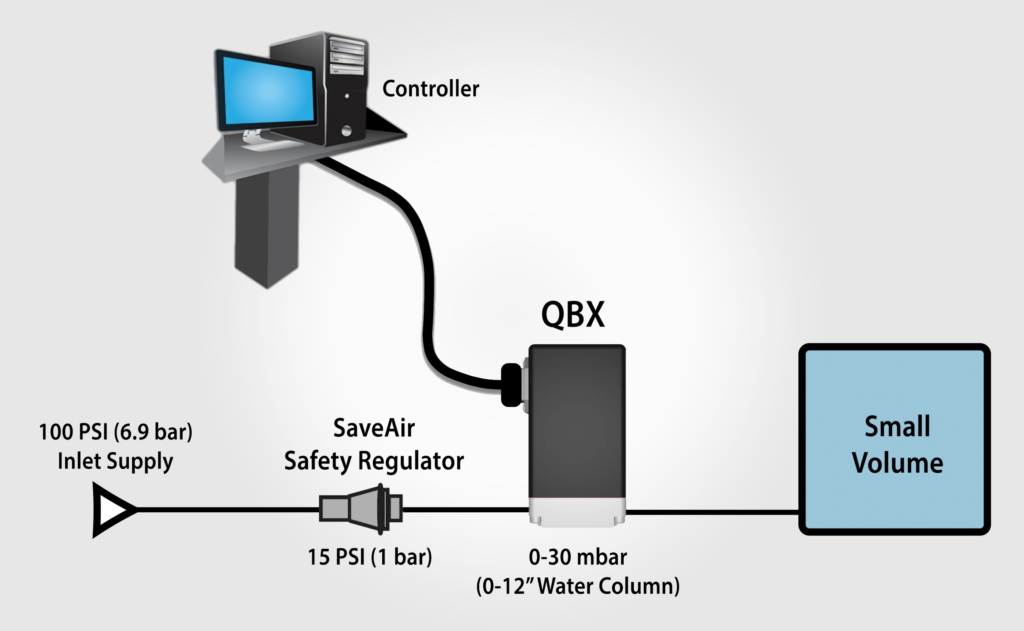
Miniature regulators are also helpful for compact and mobile systems. As the trend for smaller-but-stronger equipment persists, design engineers seek solutions that ensure accuracy while decreasing the equipment’s footprint.
Improving resolution in microfluidics
Pressure resolution is the smallest change in command that will result in a change in output pressure. It can also be described as the ability of the transducer to resolve an output signal in the units of the output device scale. High resolution means that a finer scale is used, and the amplitude of the full scale is divided into smaller increments.
“When you have smaller increments to work against, it becomes easier to offer specific and even minute results or work at the cellular level,” said Ron Hibbler, applications manager at Proportion Air. “We achieved this high-resolution pressure control using a true proportional solenoid valve coupled to a unique analog PID control circuit. The true proportional valve eliminates digital stepping.”
A common use for high-resolution devices is microfluidic applications, where small amounts of gas must move through tiny channels. Highly accurate and high-resolution devices provide stable and repeatable pressure control, which results in stable and repeatable flow through the microfluidic channel. Industrial groups and researchers find microfluidics attractive because it dramatically reduces sample and reagent consumption, shortens experiment time, and allows multiple tests to run simultaneously.
“The need for a fast response isn’t only for microfluidic applications,” said Hibbler. “Products in our electronic regulator category offer a pneumatic response of less than 1 sec and an electronic response in under 10 msec.”
Controlling differential pressure
Many applications require differential pressure control, which requires precise pressure control relative to a different pressure in the same process. For example, Figure 4 shows a dispensing application where two QPV high-resolution pressure regulators work in tandem to dispense a sample-solution combination. A counting sensor gathers information at the dispensing point and sends it to the PLC, which calculates the required pressure and sends corresponding signals to both QPVs.
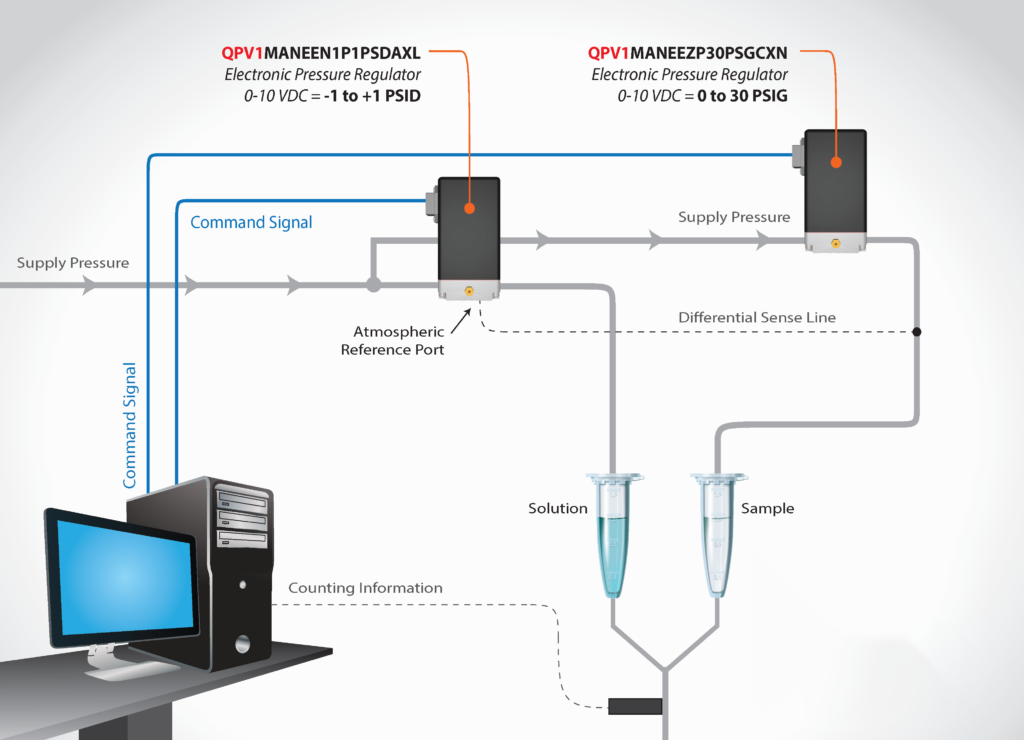
Each QPV is calibrated with respect to an atmospheric reference point to constantly maintain a specific differential pressure from solution to sample. The solution-dispensing QPV’s atmospheric reference point port is tied to the output of the sample-dispensing QPV through the differential sense line. This means that the solution-dispensing QPV will use the pressure controlled by the sample-dispensing QPV as the baseline, ±1 psi. For instance, if the sample-dispensing QPV is set at 15 psi, the solution-dispensing QPV will be 14 to 16 psi.
“The SPV is another product that trims all unnecessary size and weight while maintaining the high performance of the larger, more rugged QPV series,” said Hibbler. “This compact high-resolution valve does not exhaust downstream pressure, only fill and control during constant flow conditions.”
Learn even more about pneumatics in this Fluid Power Webinar: (Nearly) Everything You Wanted to Know About Pneumatic Control
Proportion Air
proportionair.com
Filed Under: Air Preparation & Regulation, Components Oil Coolers, Pneumatic Tips