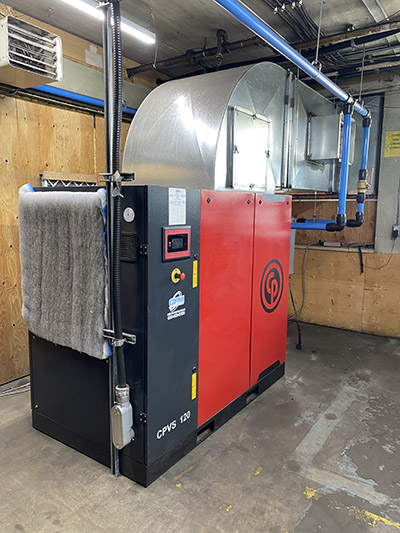
A local food company was resizing its compressed air system while renewing its plant operations. To get the sizing correct, the plant maintenance foreman purchased a flow meter to measure the output of the compressors.
The meter was installed with a data logger to capture the flow profile of the plant. The readings showed that the peak flows were 450 cfm, and the average was 300 cfm — so a main compressor sized at 90 kW was purchased and installed.
Shortly after installation, the maintenance foreman was surprised to see low pressure was occurring, indicating the compressor was too small. The compressor was rated at 500 cfm, yet the flow meter still showed peaks of no more than 450 cfm during the highest production times.
A compressed air auditor was called in to investigate and immediately recognized a problem. The plant was using a heatless desiccant dryer to dry the air — and it was consuming purge flow. The flow meter, being of thermal mass design, was installed after the dryer, so did not capture the 150 cfm of purge in either the peak or average reading.
The auditor examined the flow meter records and found that the system flow during non-production times was a steady 150 cfm, indicating a high level of leakage. He also tested the air dryer and found the purge flow was 60 cfm higher than normal. With some adjustments and leakage repair, the peak plant loading was reduced enough to ride out plant peaks with the new compressor.
Things are not always what they seem when using thermal mass flow meters. It is important to ensure you have a good grasp of the flow requirements upstream of the meter before sizing compressors.
Filed Under: Air Preparation & Regulation, Pneumatic Tips