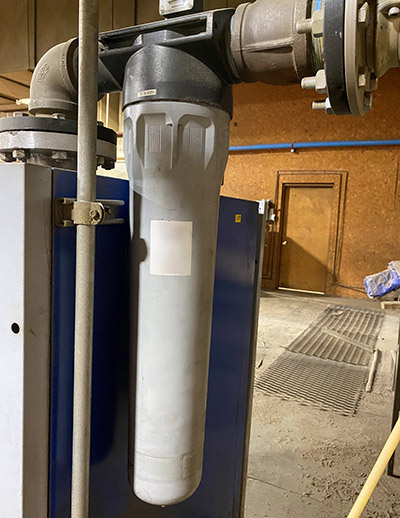
By Ron Marshall
A building products company had a compressed air system that featured one large 1,500-cfm compressor and three smaller ones. The compressed air flow had grown to a point where the large compressor could only be turned off during shutdown periods; when it was turned off, the plant pressure would collapse.
The large compressor was installed with its own air dryer and filters, with the other compressors having a set of parallel filters and dryers. A compressed air auditor noticed during a plant assessment that while the smaller compressors ran at normal pressure of around 95 psi, the large compressor ran at elevated pressure above 105 psi. Because the compressor was only rated at 100 psi at full load, this was a concern.
More investigation revealed that an extra filter had been installed at the discharge of the large air dryer. The inlet filter was a very efficient mist eliminator design (1/2-psi rated), and the dryer was properly sized for the flow (3-psi rated), yet the pressure loss across the dryer/filter combination was 13 psi. It should be noted the filter differential gauge was showing no pressure drop (it was later found to be defective).
For some reason, this extra coalescing filter had been installed and then simply forgotten about. It was arranged where there was no bypass to enable changing the element, so it had never been maintained in its six-year existence! Nobody knew the reason for its existence because the other compressors had no such filtering.
The auditor calculated that the excessive pressure loss across this filter was costing about $7,000 per year in extra electricity costs. And making matters worse, it was contributing to accelerating aging of the associated air compressor, due to the overheating.
Filed Under: Air Preparation & Regulation, Compressed Air Technologies, Pneumatic Tips