SMC recently updated the pneumatic system on the Boilermaker Special VII, the official mascot of Purdue University. According to the Reamer Club that cares for the train, the Boilermaker Special is the world’s largest, fastest, heaviest, and loudest collegiate mascot. Some of these accolades can be attributed to the train’s extensive pneumatic system, which controls the horns, bells, whistles, smokestack, and cowcatcher.
The previous system was installed 20 years ago and needed an update. It was dirty and grimy, and the filter was covered in oil, which decreased the lifespan of the equipment. Therefore, the Reamer Club contacted SMC for help. SMC donated all new products and sent a team of four engineers, including Purdue University alumni, to collaborate with the Reamer Club and design a new system.
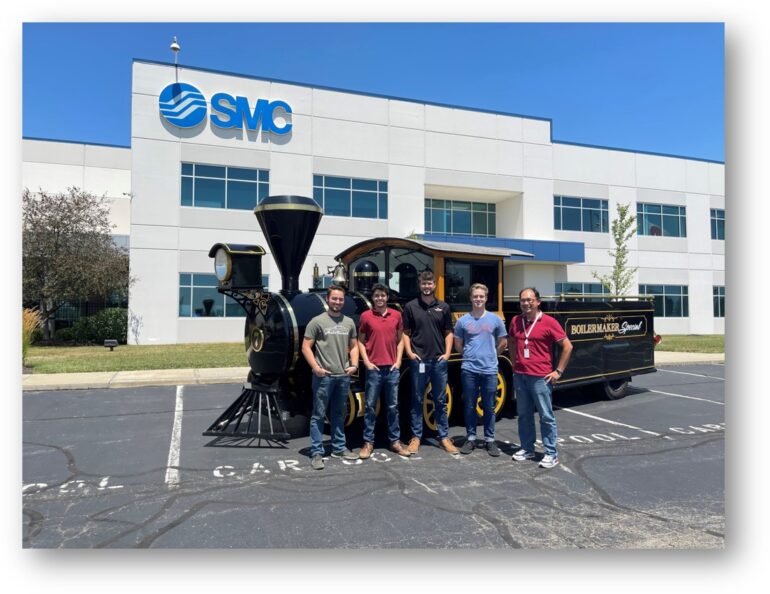
The engineering team examined the existing pneumatics to understand and scope new design requirements. The system included cylinders and valves that supported the horns, cowcatcher, floating axle, and CO2 for the smokestack. The team measured cylinder lengths and space constraints for the air preparation system and valves, performed flow testing, and assessed electrical needs. They also considered the outdoor environment that the system would need to withstand during home and away sporting events, as the train was often exposed to rain, snow, road salt, and harsh conditions.
While researching the horn’s required flow for maximum performance, the team was conscientious so that the horn’s sound would not cause hearing damage to nearby ears. “We were able to specify the flow rate to be about 100 lpm higher than what the system was currently, which allowed the horns to be just below the threshold of pain,” said Michael Spicklemire, project lead and design engineer in SMC’s United States Technical Center.
The new air preparation system installed in the coal car behind the cab is SMC’s AC-D series modular air preparation unit for filtration, water separation, and lubrication. It includes a safety dump ball valve controlled by a switch on the cab’s control panel and a VHS series manual shutoff valve. The VHS series provides a convenient means of isolating supplied pressure in a pneumatic system and exhausting downstream pressure for maintenance purposes. The units can be locked in the exhaust position and are an integral part of an energy isolation system.
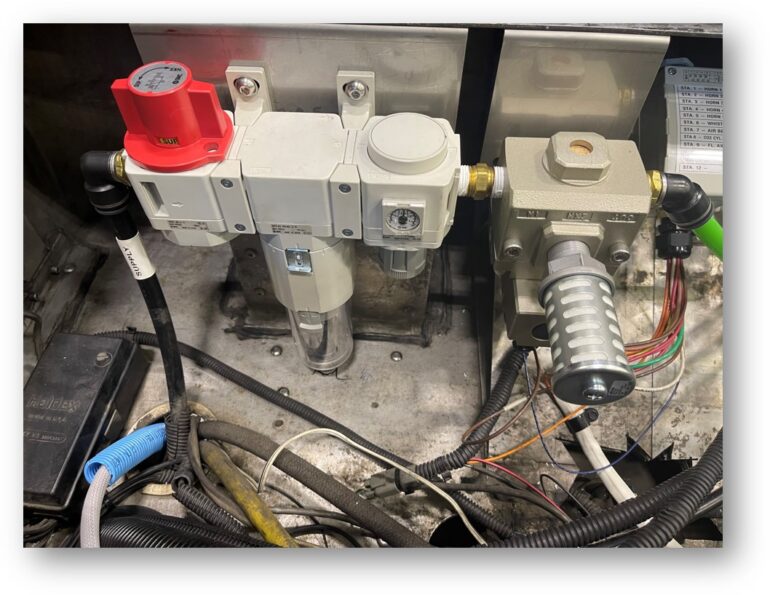
A 12-station VQC 4000 series valve manifold directs the air to the horns, bell, whistle, and two air cylinders. One air cylinder at the front of the train raises the cowcatcher when pressurized, and the cowcatcher lowers by gravity when unpressurized. Another cylinder located in the coal car actuates a lever that releases CO2 from two tanks and exhausts it through the smokestack.

A control panel inside the cab includes light-up switches and buttons for each horn, the CO2, and the safety dump valve, allowing the driver to stop all air pressure immediately.
SMC also provided new tubing, wiring, fittings, and updated schematics for the Reamer Club’s operator manual.
“Many SMC engineers graduated from Purdue, so this project feels very full circle for us,” said Aaron Pfeiffer, an engineer in SMC’s United States Technical Center. “It has also been a great way to connect with the next generation of engineers at Purdue.”
SMC
smcusa.com
Filed Under: Pneumatic Tips, Trending