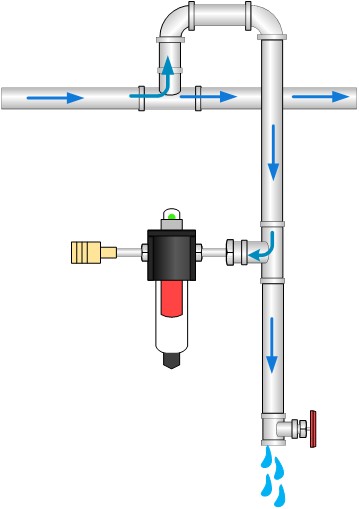
Are you spending your summer struggling with the quality of your compressed air, with stinky, rusty water pouring out of your pipes? When it comes to air quality, the hot summer months are the most challenging time for most compressed air systems, and to avoid problems, you need to plan for the worst-case scenario.
Typically, especially for air cooled compressors and dryers, the worst-case time will be during the hottest most humid day, after a rainstorm, when the air compressors are ingesting the most water vapor and outputting the hottest discharge temperatures. Heat is the enemy of compressed air systems, because during hot conditions, the 100% saturated discharge air from the compressors contains the most water.
Each 20° F increase in discharge temperature doubles the amount of water vapor. If you don’t plan for these conditions, the air dryer will be overwhelmed — and free water will find its way into your downstream plant piping system.
Some tips on solving these water problems include:
- Design your compressor room cooling system to pull the coolest possible air from outdoors, and exhaust hot compressor air through insulated ducts to outdoors.
- Install cross ventilation to remove radiated heat from the compressors and ducting. Realize the air dryers and any other compressor room equipment will generate heat that needs to be removed.
- Check with weather records, if you want a continuous supply of good quality air, you must anticipate maximum possible humidity and temperature levels.
- Follow the “three 100” sizing rule for air dryers. If conditions will cause inlet air temperatures above 100° F, inlet pressures below 100 psi, and ambient temperature above 100° F, you must upsize your air dryer to compensate. This means its capacity must be larger than the total compressor capacity.
- If the location of the compressor room makes it impossible to limit the compressor discharge temperatures to meet the abovementioned rule, then a secondary cooling method for the compressor discharge air is required. This can be a secondary air cooler, a cooler using water as a media, and/or a wet storage receiver.
- Plan for the eventual temporary failure of the air drying system by designing the piping system with a slight slope away from the compressors, installed to help any free water to drain away. Put in low points with condensate drains to trap water and install all supply taps for down-drops to come from the top of the main distribution piping to minimize water pick-up.
- Ensure the condensate drains at the air compressor air cooler separator (the most important location), wet tank drain, filters, and dryer drains are working. Maintain these well.
Hoping that as summer wears on, you experience dry conditions!
Filed Under: Components Oil Coolers, Compressed Air Technologies, Pneumatic Tips