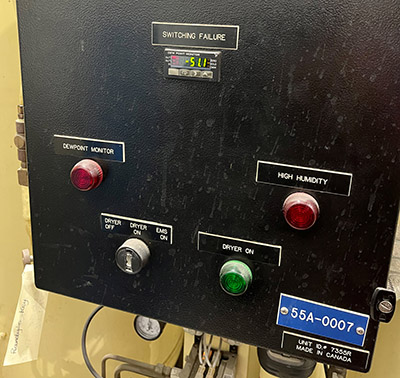
A meat processing company air upgraded its compressed air system to increase capacity and reduce energy consumption. They installed large, premium efficiency VSD compressors, a smart compressor controller, efficient filters, large storage, and heated blower desiccant dryers connected with oversized compressor room piping — all in an effort to reduce pressure loss.
The maintenance workers showed off the system with great pride. It was saving significant energy, so they should definitely be proud. However, a compressed air auditor looking over the system quickly pointed out that they forgot one thing, and it was costing them thousands of dollars.
Lurking in the plant was a heatless desiccant dryer, part of the old system. It was installed remotely because the old compressor room had limited space.
There were areas of the plant that operated at near 45° F temperatures. Because of this, they found refrigerated air dryers did not produce dry enough air to prevent water from condensing in the cold compressed air lines. Compressed air contacted the product, so it had to be desiccant dried to avoid contamination.
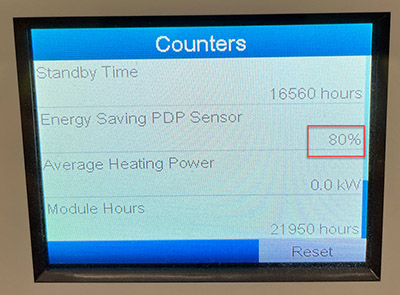
The old heatless dryer was rated at 1,060 cfml; a dryer of this size in uncontrolled mode will constantly consume 150 cfm of purge air. The new system compressors produced air at 18 kW per 100 cfm specific power, so the energy consumption was about 237,000 kWh costing about $24,000 per year in energy. The sad part of this story is that this old dryer was equipped with an energy management system, but it wasn’t turned on. The plant operators never activated it, even after it was in service for 15 years. For the past two years, the old dryer was drying already dried air, a flow that was already processed by the new, more efficient heated blower dryers.
It took only a few minutes for the powerhouse chief to decide to remove the dryer from service and reduce the waste. Be sure to assess your system after an upgrade to ensure there are no areas of forgotten excess waste!
Filed Under: Components Oil Coolers, Compressed Air Technologies, Pneumatic Tips