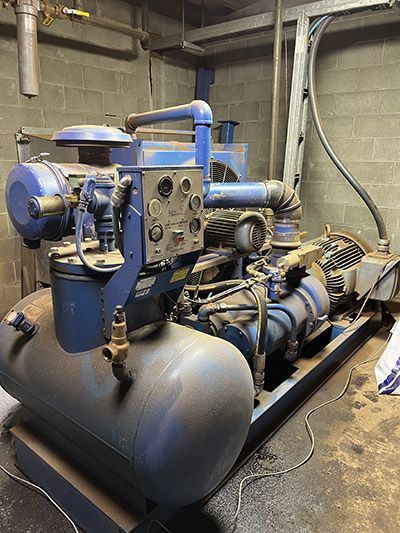
When is it time to retire a compressor? Your old unit may have served you very well over the last few decades, reliably providing a seemingly endless supply of compressed air. Some units, like the unit in Fig. 1, have been around so long that they have almost become part the family.
This design is extremely hardy and tough — they last a long time and were well designed for longevity. In fact, this unit could well last another 10 to 15 years if maintenance is kept up. However, there are hidden costs that must be defined by measuring the compressor’s performance. The unit in the picture, while efficient at full load, has a tough time supplying part loads. And this is a problem at this site because the average loading is only about 30% of the compressor’s capacity.
This 150-hp unit, and many like it, is running in a mode called “straight modulation,” the least efficient way to control lubricated screw compressors at part load. When the pressure rises above the compressor setpoint, a control signal causes the inlet valve to start to choke off the flow. Typical energy reduction for this type of control is about 3% for every 10% reduction in flow, which becomes problematic if the compressor is lightly loaded.
This particular compressor does not follow the typical curve; its energy reduction is almost zero for any reduction in flow output. It constantly consumes power of about 125 kW when running at 190 cfm or at 650 cfm. Its specific power (kilowatts per 100 cfm) is often near 70 kW/100 (normal is about 18 kW/100 cfm for a well-controlled compressor).
If left running the way it is, its annual operating cost would be about $100,000 per year in supplying about 200 cfm of average compressed air flow. But should a new compressor with better part load control (called load/unload) be installed in its place, the operating costs would be reduced to about $50,000 per year. And if a new VSD compressor was purchased, the electrical cost would reduce to about $29,000 per annum!
For this plant, the operating staff must decide: waste more than $710,000 in electricity over the next 10 years or replace the unit with a new more efficient unit? The choice seems clear once we bring out the hidden energy costs.
Are you keeping an old unit running that should be retired? How much could you save if the compressor was replaced?
Filed Under: Components Oil Coolers, Compressed Air Technologies, Pneumatic Tips