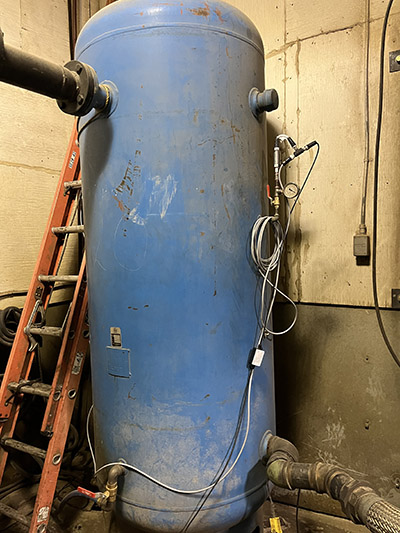
Compressed air receivers have become more important in modern compressed air systems. Having an adequately sized main receiver in the compressor room is quite important for the health and efficiency of your air compressors, especially if you have switched from small reciprocating compressors to lubricated screw type.
Years ago, the rule of thumb for use in sizing receiver tanks was to install one gallon of storage capacity for each cfm output capacity of the trim compressor (trim it the one taking partial loads in multiple compressor systems). But energy studies have shown that lubricated screw compressors with this small volume capacity will rapid cycle, causing additional energy consumption due to the unique characteristics of the lubricated screw compressor type. We have learned from this mistake and have found the best practice is to install between 3 and 5 gallons of storage per cfm of the trim compressor, with a stress on sizing on the high side of this range.
For small reciprocating compressors, often sitting on tanks, the size of the storage receiver capacity, and the width of the pressure band affects only the frequency of start cycle of the compressor. To prevent too many starts per hour, the pressure band is usually wide — say 35 psi between start and stop. The energy efficiency of a reciprocating compressor is not affected by storage size. The operating costs versus flow are usually linear for reciprocating compressors, a unit that is only 20% loaded will cost 20% of the full load energy, because the compressor stops between cycles.
For a lubricated screw compressor, a type that often replaces old reciprocating units, the storage size matters a lot. Internal to the screw compressor is an oil sump, this sump must be blown down slowly or there will be high lubricant carryover, this slow blowdown makes the compressor very inefficient when cycling rapidly as a result of small storage. Screw compressors can only be started 6 to 10 times per hour, often requiring them to run constantly and when they run do they consume t least 25% of full load kilowatts, even when no air is being produced.
A small 25-hp reciprocating compressor loaded at 20% would cost about $1,600 to run on an active system pressurized for 4,000 hours per year running at 10 cents per kWh. A 25-hp lubricated screw compressor with small storage would consume about $5,000 per year in electricity. The same compressor with large storage 3-5 gallon per cfm might consume $3,400 per year, double the reciprocating cost. A screw compressor with very large storage, sized to allow only 6 starts per hour would consume about $1,500 per year.
Receiver tanks can make a big difference!
Filed Under: Components Oil Coolers, Compressed Air Technologies, Pneumatic Tips