A sawmill maintenance department requested a compressed air assessment to determine the efficiency of its system and to find out if any improvements could be made to reduce their compressed air system operating costs. They called in an auditor who placed data logging equipment to measure pressure, flow, and power.
From these measurements, the auditor was able to do an analysis of the system and calculate system efficiency, in kilowatts per 100 cfm produced. One of the first things that is done in analyzing a system is to view how the pressure, flow, and power change in relation to each other. When the auditor took an initial look at the data, he found a surprising pattern to the pressure and flow readings.
In looking closely at the flow profile, and matching it up with the time base, the auditor observed that there were two distinct plateaus on the flow profile, and these were occurring regularly exactly every 5 minutes. The cause of this becomes obvious when we realize that this system has a heatless desiccant air dryer installed.
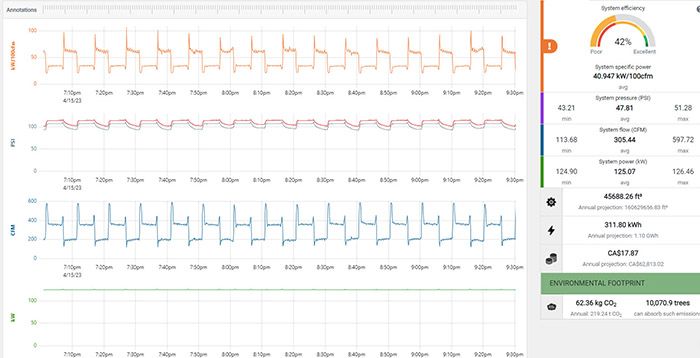
This style of air dryer has twin towers filled with desiccant; while one tower is drying, the air the other side is purging. This purge drives off the moisture that the desiccant beads collect when the tower is actively drying. Every 5 minutes, a system of valves changes position and swaps out the towers to change the active side. The purge flow is set at a constant 15% of the rating of the dryer. However, sometimes the valves within the dryer can stick open, causing an extreme amount of air to leak into the side being regenerated. This was what was happening and was the cause of the strange 5-minute cycle detected by the data loggers.
This dryer is rated at 750 cfm which, if working properly, needs a purge flow of 112 cfm. Yet, due to incorrect adjustment of the purge flow valve, and a faulty check valve, the dryer was actually consuming 270 cfm, more than double the rated flow, wasting about $28,000 per year in equivalent energy costs! Further to this, the flow of wet air into the side being regenerated was causing poor air quality and a resulting freeze-up of compressed air lines in winter.
These findings show, yet again, the value of having regular compressed air assessments done on compressed air systems. The correction of this problem returned this system to normal operation, saving much more than the cost of the audit in energy and maintenance costs.
Filed Under: Components Oil Coolers, Compressed Air Technologies, Pneumatic Tips