A routine audit of a wood products company has turned up some surprising results on a system that was thought to be very efficient. The system is simple — one compressor, a 100-hp variable speed drive controlled (VSD) screw compressor, and a heatless desiccant air dryer. Data loggers were placed on the system by a compressed air auditor to measure pressure, power, and flow and found that, in reality, the system is running quite inefficiently compared to a normal optimized configuration, with system specific power (kilowatts consumed per 100 cfm produced) reaching very high levels during light system loading.
We can see from the system profile, Fig. 1, that at higher system loads, the specific power drops to 22 kW per 100 cfm. However, during the weekend, the efficiency is very poor, hitting highs of greater than 42 kW/100 cfm. The auditor verified that this compressor is producing air at normal specific power of about 18 kW/100 cfm, so the question is: what is going wrong?
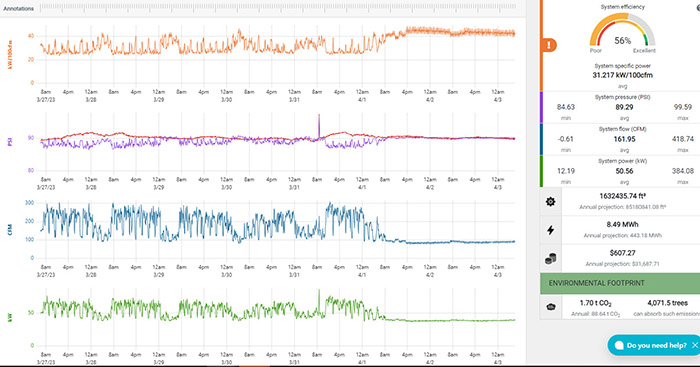
The answer lies in the placement of the flow meter in this system. It is located after the desiccant dryer because it is a thermal mass style that can only measure dry air. The purge flow into the dryer is therefore not measured and causes the reported system efficiency to be low. The dryer is an uncontrolled heatless desiccant style that consumes the same 80 cfm of rated purge flow constantly — even though the average flow through the dryer is about 160 cfm, much lower than its 500-cfm rating. The air dryer purge is the problem here. To add to the challenge, desiccant dried air is not required at this plant as there are no pipes that are exposed to freezing temperatures (and no special requirement for super-dry air in the production processes).
The solution to this efficiency problem is the replacement of the dryer with a more efficient style. The best solution would be to dry the air with a cycling refrigerated unit and save about 12 kW equivalent in purge flow. Savings for this would be roughly $9,000 per year. And if in turns out a desiccant dryer must be used, purchase of a new one that has dewpoint control and uses an external heater — rather than straight compressed air to regenerate the desiccant — would save an estimated $5,000 per year.
It is best not to let an uncontrolled desiccant air dryer rob the system of its efficiency!
Filed Under: Components Oil Coolers, Compressed Air Technologies, Pneumatic Tips