When working with desiccant-style compressed air dryers, there are several factors to consider, to ensure optimal performance and efficiency. Desiccant dryers rely on two towers filled with desiccant material that alternately dry the air and regenerate, to maintain continuous operation. The regenerative purge is essential to removing the moisture collected by the desiccant, but it also impacts energy consumption, system pressure, and maintenance needs.
Regenerative desiccant dryers typically consume between 15-20% of the dryer’s rating to regenerate the saturated desiccant. This purge air loss can significantly affect overall system efficiency, especially if things are not working correctly.
Proper cycle control ensures that the desiccant is sufficiently regenerated without wasting energy or air. Traditional dryers operate on fixed cycles, switching between towers at set intervals, whether or not the desiccant is fully saturated. This is wasteful. Demand-based control systems, on the other hand, monitoring the dew point and initiate regeneration only when necessary. As in Fig. 1, this can improve energy efficiency by reducing unnecessary purge air use. The dryer shows it has saved millions of cubic feet of compressed air over its life.
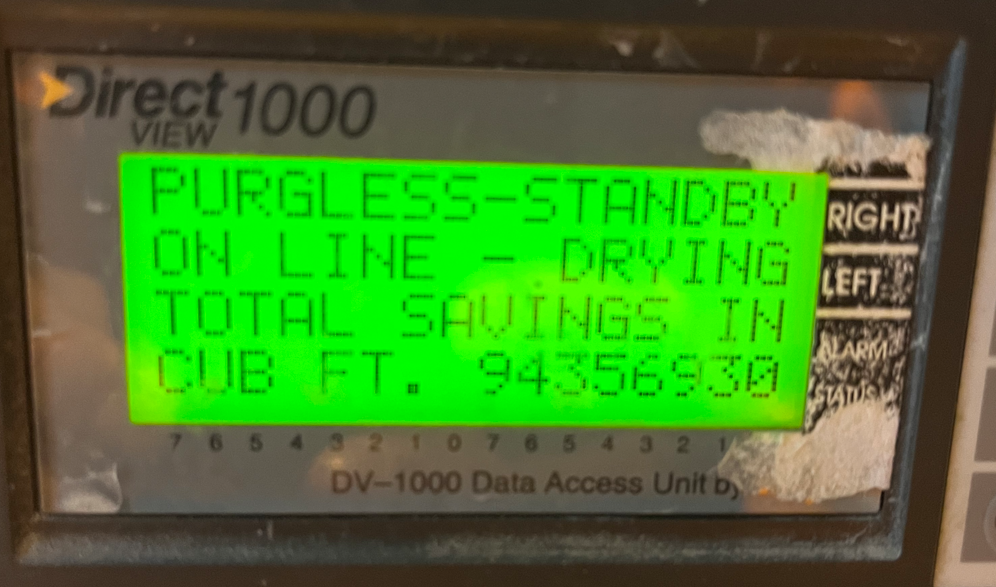
The goal of the desiccant dryer is to deliver air with a dew point low enough to prevent moisture condensation. However, an improperly managed purge cycle can cause fluctuations in dew point, compromising air quality. Monitoring and adjusting the purge cycle ensures that the air remains dry, particularly in environments requiring very low dew points (e.g., -40° F/-40° C). Consistent dew point control protects downstream equipment and helps maintain high product quality in sensitive applications.
The efficiency of the regenerative purge process depends on the health of the desiccant material. Over time, contaminants such as oil or particulate matter can degrade the desiccant, reducing its capacity to adsorb moisture and requiring more frequent regeneration. Regular maintenance, including replacing spent desiccant and cleaning filters, is essential to maintaining dryer performance. Monitoring purge cycles for irregularities can also help detect early signs of desiccant deterioration or system issues.
By carefully managing purge air loss, controlling dew point, and maintaining the desiccant material, plant maintenance personnel can ensure the efficient operation of their desiccant-style compressed air dryers.
Filed Under: Air Compressors, Air Preparation, Components Oil Coolers, Compressed Air Technologies, Engineering Basics, Pneumatic Tips