When performing leakage detection on your compressed air system with your ultrasonic leak detector (if you don’t have one, good grief, run out and get one!), you will run across various leaks in piping and equipment. Many of these are small, so roughly less than $100 value per year.
But quite often, you will find some significant leakage and perhaps compressed air system waste, such as uncontrolled blowing or cooling with compressed air. When you locate a big, wasted flow, the question will be: how much compressed air is it consuming and what is the cost?
You can compare the flow measured by a main flow meter before and after a change, in order to help you estimate leakage — but in big plant, this is not an option. So, with a little creative thinking, we can come up with a very accurate, inexpensive, and portable leak measuring assembly for you to use in measuring compressed air consuming devices and leakage.
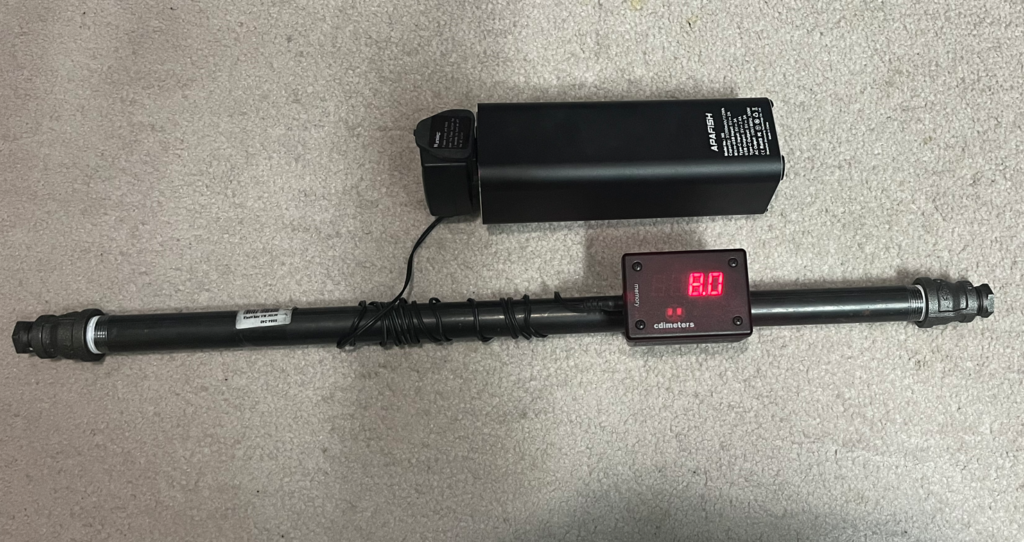
All it takes is to purchase a small insertion flow meter, a length of pipe, some fittings and as an added option, a battery power bank (example shown in Fig. 1).
The use of this measurement assembly is simple: install it in-line with the device to be tested and read the number. Then take the flow reading, multiply by about 0.2 (the number of kW per cfm in a typical system), then times the number of annual hours the device is operating. This gives you the kilowatt hours per year. Multiply this by the cost of electricity from the electrical bill and you have an estimate of annual cost.
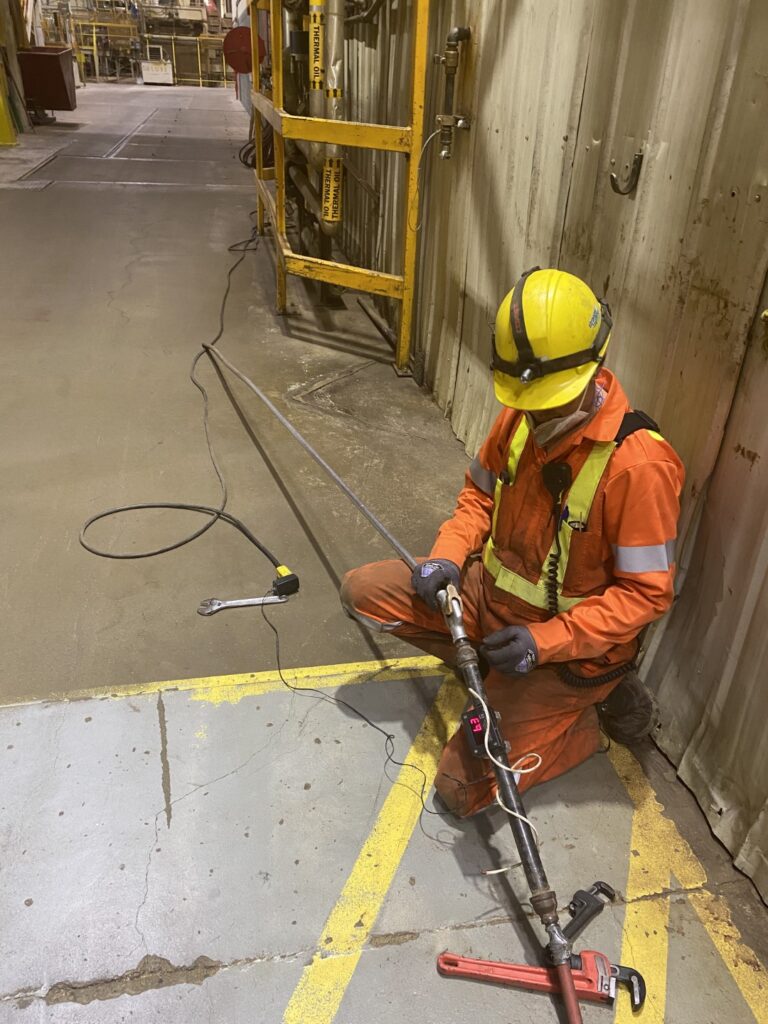
Here is an example calculation from Fig. 2:
83 cfm x 0.2 kW per cfm x 1000 hours per year x $0.1 per kWh = $1,660 per year
Sometimes this device cannot be installed inline. If so, no problem — hook it up to any handy port and back feed the leak with an alternate source of compressed air to get the measurement.
Measure your waste, and you may be surprised by the result!
Filed Under: Air Compressors, Air Preparation, Components Oil Coolers, Compressed Air Technologies, Engineering Basics, Pneumatic Tips