Do you know how much air your compressed air system is consuming? How about the level of waste during non-production? If you don’t, it may be time to purchase a flowmeter to find out the answers to these questions.
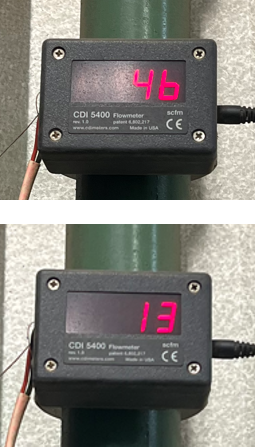
Recently during a leak assessment, a compressed air auditor was surprised to see 46 cfm flowing into a small plant when nobody was working. This flow kept the air compressor running 24 hours per day and 7 days per week — even though production was 8 hours per day, 5 days per week.
The auditor was performing ultrasonic leak detection with a sensitive detector and found about 10 cfm of leaks in the facility. He also detected a significant flow of air inside a critical machine. In inquiring about this demand, he was told that this flow of air was purge used to keep sensitive internal items clear of dust.
The auditor wanted to put a price tag on this application, and he noticed the plant had a thermal mass flow meter installed at the compressor. The flowmeter showed 46 cfm flow when there was no production. He arranged to have the air supply to the critical machine turned off — and the flowmeter reading dropped to 13 cfm. This one production machine was consuming 33 cfm of air for blowing purge to keep the machine clean, even when there was no production. A quick calculation revealed that the compressed air cost for this one device was $6,400 per year!
Some research was done, and it was concluded that the air supply on this machine could be shut down during non-production times, saving significant costs, in fact it was found that the whole plant could be turned off during non-production times, reducing the operating hours by 5,100 hours. This saved extra leakage costs and reduced the compressor maintenance hours.
It pays to measure your compressed air flow — and pay attention to the reading.
Filed Under: Air Compressors, Air Preparation, Components Oil Coolers, Compressed Air Technologies, Pneumatic Tips