Normally when measuring the pressure gradient of a compressed air system in an industrial site, the pressure at the compressor discharge is the highest of all locations. Once the compressed air travels through piping, filters, air dryers, and other components — each causing restriction to flow — the pressure at the far end of the plant will be lower.
But this is not always the case! In a handful of compressed air audits, the air pressure at the far end of the piping was found to be higher than at the compressor discharge. This effect happens when the end of the line is very deep in a mine. Fig. 1 shows this effect.
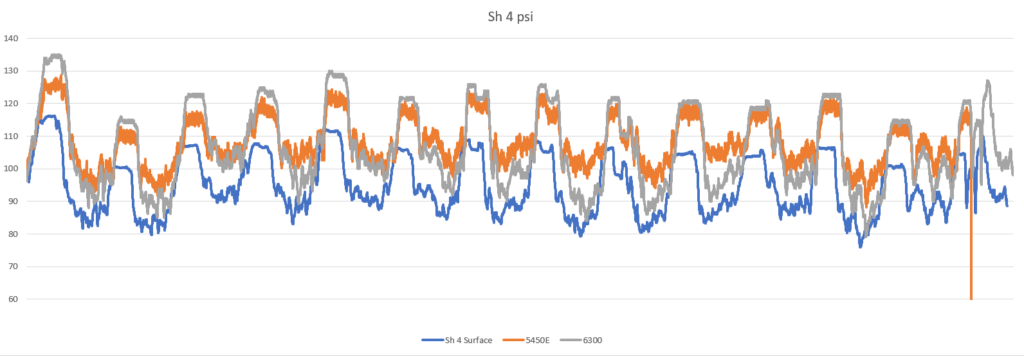
The compression effect is similar to the pressures that develop in the bottom of a swimming pool, where the weight of the column of water creates higher pressure. In a mine, the weight of the column of air in the shaft piping creates about 10 psi of extra pressure for every 3,000 feet in depth. The effect and the mathematics behind it can be viewed at this link.
This self-compression effect needs to be considered when designing equipment in a mine so as not to exceed pressure ratings. The higher pressure causes all unregulated uses, including leakage to consume about 1% more compressed air for every 1 psi in excessive pressure.
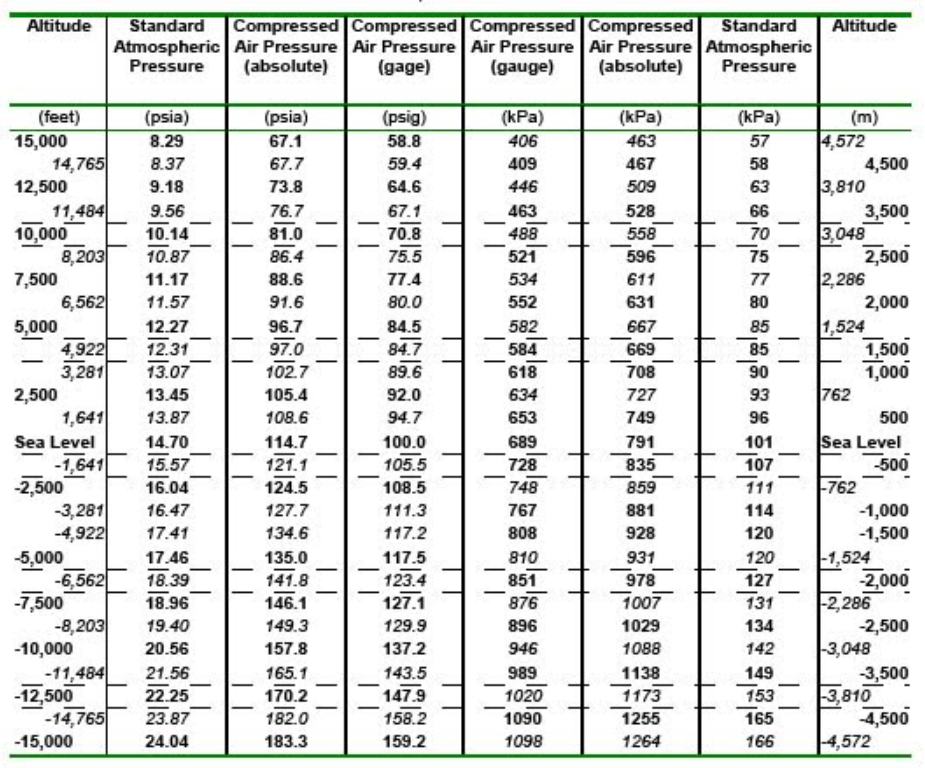
Another effect of this compression it the retention of water vapor. Air that is on surface at lower pressure can hold more water than air that is compressed at the bottom of the shaft. So if the air is not dried, there will be moisture dropping out in the piping. This water must then be pumped back up to surface for disposal — an expensive operation in a deep mine.
Filed Under: Air Compressors, Air Preparation, Components, Components Oil Coolers, Compressed Air Technologies, Pneumatic Tips, Technologies