In this blog post, we will discuss the third of five industrial compressor capacity control modes. A moderately efficient method of controlling a compressor at part load uses load/unload mode with adequately sized storage receiver capacity. (Find part 1 start/stop mode and part 2 modulating mode in this series here now)
With this mode, a pressure switch, or electronic control, is used to provide load and unload signals to the compressor. When the pressure hits the load setting, the compressor inlet valve opens and the compressor goes to full load, its most efficient point. The added capacity will push the system pressure up until the unload setpoint is reached. When unloading, the inlet valve closes and the compressor lubricant sump is blown down, producing zero flow but keeping the compressor running at about 30% of full load power.
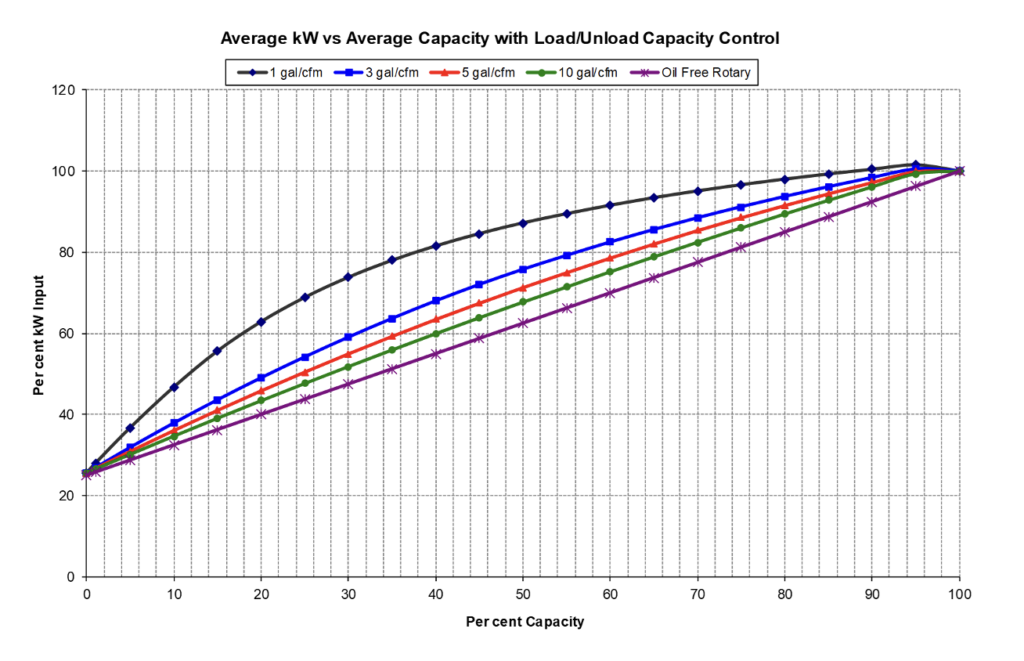
For lubricant free compressors, there is no sump to blow down, so the unload operation is quite quick and efficient. For lubricated compressors, the blowdown takes time to avoid foaming the lubricant, and while blowing down slowly to the final level, the compressor consumes more than desired power. For this reason, large storage should be installed to reduce the load/unload cycles, reducing the frequency of blowdowns. We can see from the graphic if only 1 gal per cfm compressor capacity worth of storage is installed, the compressor consumes more than 80% of its rated power when at an example load of 40%. If the storage capacity is 10 gal per cfm, the resulting cycles will be 10 times less, so the average power consumption would reduce to 60%, saving considerable power.
Typical recommended storage size is between 3 to 5 gal times the rated cfm capacity of the largest compressor in the system. With larger sized storage, the use of load/unload with start/stop control using unload timers can save even more power.
If you are running load/unload control using lubricated screw compressors with small storage, consider upsizing your system storage to reduce compressor cycles. A good way of detecting lack of storage is to time your compressor cycles. If the load/unload cycle time is less than 2 minutes, your storage is likely too small. Lubricant free compressors do not need such large storage to run efficiently, however there is still a maintenance benefit in reducing the number of cycles.
The five different capacity control modes for lubricated screw compressors are:
- Start/stop — simply starting and stopping the compressor using pressure switch control. Very efficient but can only be used on small compressors.
- Modulation — choking of the inlet flow of air using an inlet valve. Very inefficient at part loads.
- Load/unload — Loading and unloading a compressor using inlet valve control and sump blowdown. Moderately efficient if the compressor has access to large storage.
- Variable displacement — Opening up ports in the screw to bypass the compression element. Good efficiency if set up correctly.
- Variable speed drive — Speeding up or slowing down the compressor to vary its output flow. Most efficient operation at part load if applied properly.
In the next blog post, we will discuss the variable displacement control mode.
Filed Under: Air Compressors, Air Preparation, Components Oil Coolers, Compressed Air Technologies, Engineering Basics, Pneumatic Tips, Technologies