A compressed air auditor regularly flow-tested the compressors under his study. This generally would be done if the air compressor was drawing low amps — a telltale sign that the unit is producing low flow output — or if the compressor has excessive hours. Often times, internal wear due to age will reduce output capacity.
To do the test, an apparatus with various calibrated orifices (called an LP-07) is hooked to the compressor discharge and the compressor is isolated from the load. For example, if the 200 cfm plus 100 cfm plus 50 cfm ports are opened up, and the pressure is pulled down to 100 psi, the compressor output is simply found by adding everything together for a total of 350 cfm.
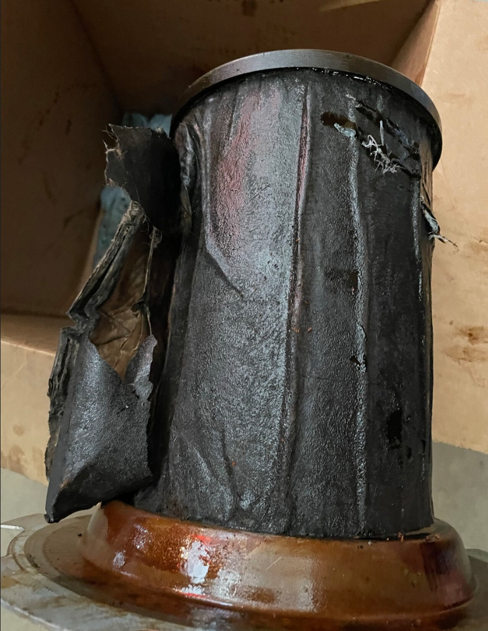
One fine morning, the auditor was testing a very old compressor. The unit was filled with ATF lubricant, which makes a red sticky mess if it leaks out of the compressor. The auditor was in the middle of his testing when the compressor air/oil separator unexpectedly failed, releasing all the compressor’s lubricant in a torrent. The flow tester had mufflers attached to each orifice, which suddenly acted like shower nozzles. This totally drenched the surrounding area and the auditor himself, who ended up looking like a drowned rat. Lesson learned about testing old compressors!
The failure of separators in lubricant injected screw compressors is infrequent, but when it happens, it can completely contaminate downstream compressed air filters and air dryers. The lubricant can also fill downstream piping with compressor oil, causing an expensive to clean mess in the system.
It is important to keep an eye on the separator condition to avoid system disaster. Signs of impending failure might be high separator differential pressure or an increase in lubricant carryover. Manufacturer’s maintenance specifications for the number of operating hours should be followed to the letter to avoid separator failure disaster.
The compressed air auditor in question was horrified this happened, especially when he tried to drive home in his nice clean truck. He had no change of clothes, but the silver lining was that the spent lubricant ended up in the compressor room and not in the system piping. Not much of a consolation, but worth something!
Filed Under: Air Compressors, Air Preparation, Components Oil Coolers, Compressed Air Technologies, Pneumatic Tips, Technologies