By Josh Cosford, Contributing Editor
Hydraulics is a venerable technology as mature as any competing force transfer system outside of straight mechanical conveyance. Most recent hydraulic advancements aren’t from any fundamental changes in the pump, valves and actuators used in hydraulic systems but rather from the implementation of increasingly advanced electronic technology.
Early fluid power technology
The early days of fluid power technology were strictly limited to manual operation of valves with limited versatility. Joseph Bramah’s first hydraulic press was as simple a circuit imaginable. It was equipped with a single hand pump aided by two check valves, as is typical of current technology. It extended the cylinder upwards for printing and seed oil processes.
This single-acting press design used a ball screw as the return valve, which, when screwed open, would allow the press to lower. As circuits became more complex, bespoke solutions such as cast iron housings with machined internals and custom spools rose in popularity. With no industry standards, machine builders created unique solutions that suited their application only, but such designs were bulky, complex and expensive.
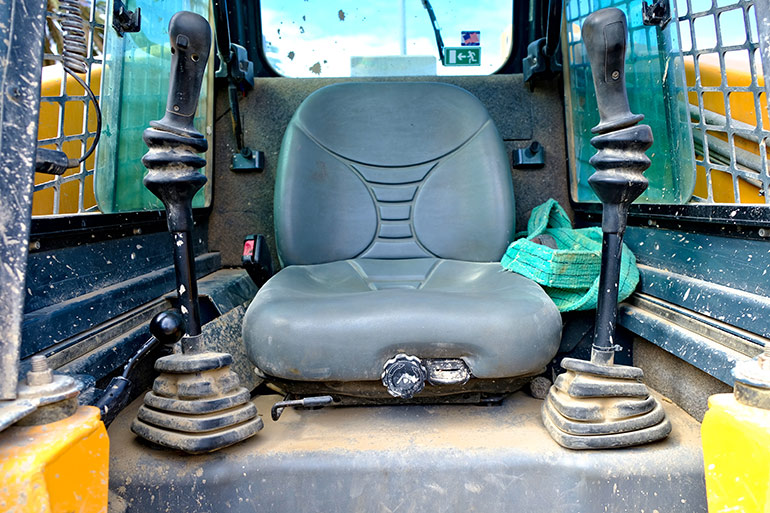
In the late 1800s, the Industrial Revolution changed the nature of manufacturing, and companies began using machines to make machines. The flurry of creative ideas and subsequent patents led to an explosion of designs as engineers and entrepreneurs searched for the “better mousetrap.” When the dust settled, the spool valve replaced ball and gate valves, especially after the switch to mineral oil from water in the early 1900s. Mineral oil provided the stable viscosity and lubrication properties a spool valve needs to work effectively, but these valves were still manually operated.
Any hydraulic circuit was either plumbed with pipe or machined into casting, and despite this, circuits were increasingly complex. Any type of automation required the installation of separately installed and plumbed cam, plunger or roller valves in addition to various pressure valves, which, of course, had to be separately plumbed using pipe if they weren’t installed into the castings mentioned earlier.
The downside to these old technologies was not just in the complexity of design and manufacture but also in the lack of ergonomic consideration for their operation. Any lever that operated a function couldn’t always be located in a single, convenient location, so functions would have required inconvenient personnel movement to activate subsequent functions.
For mobile machinery especially, a lack of convenient control location made work difficult until spool valves with inline bodies allowed designers to locate levers within reach of a single operator. Clever engineering alongside the switch to hose and tube plumbing provided more versatile control systems that could be installed in a single workstation. Although centralized plumbing provided a leap in ergonomics, any hose or fitting leak resulted in a bad day at the office.
Increasing flow rates forced changed designs
Searching for ways to move valves outside the cab became a priority when flow rates increased alongside machine size. We could simply no longer pack the cab, Figure 1, with control valves grown to use 1 in. NPT ports and larger. The implementation of cable-operated valves led the way to hydraulic pilot control, as flow forces at high pressure and flow made operation difficult with strictly mechanical control.
Still, pilot control of directional valves added a level of complexity above and beyond what were already increasingly complex hydraulic systems. All the advanced features of modern excavators, for example, such as load sensing and horsepower control, are now operated with complicated directional valve packages. As ingenious as many of these hydraulic controls were, there had to be a better way to maintain or improve performance while reducing complexity. Enter electrification.
Early electronic controls
The first electrically operated valves were created in 1905 by ASCO (the very same “Red Hat” company now merged with Numatics). These were process valves meant for everyday fluids, like water, but the concept of electrically operated valves was proven, and other manufacturers followed suit.
Solenoid-operated valves, Figure 2, became popular in hydraulics over the post-Depression era, although they didn’t proliferate widely until the Second World War. Industrial manufacturing perfectly suited the switch to electrification, as the valves operated remotely were better suited to be installed near the actuators or power unit. Mobile hydraulics took longer to adopt the switch to electronic control since many functions required proportional control, which, at the time, was more expensive than simply using lever valves that were already easy to modulate by hand.
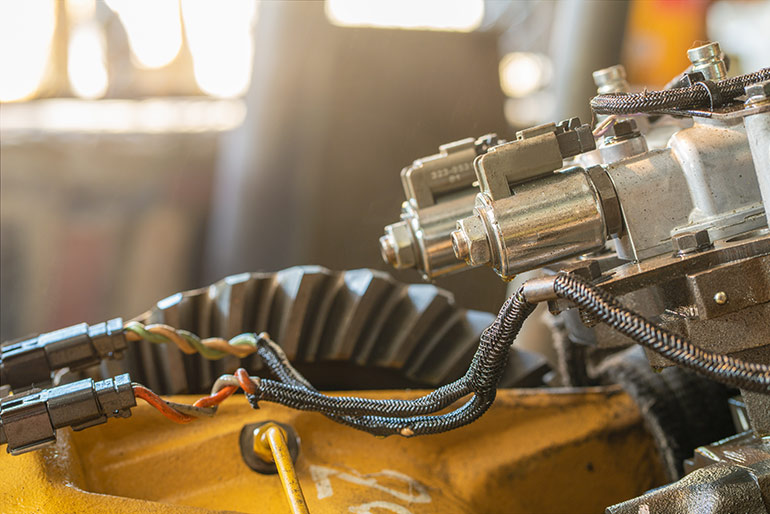
Once the widespread switch to electrified controls through the second half of the 20th century occurred, the naysayers and late adopters had little defense over lever-actuated valves. The usual complaints about what to do during blackouts or electrical failures became few and far between, and now electrified controls are the norm across many industries using fluid power, and for good reason.
Electrified controls provide more precise control over hydraulic actuators, leading to improved positioning, force, and speed accuracy, especially when combined intelligently with position and pressure feedback. This precision is crucial in applications requiring tight tolerances or accurate velocity and force. Simple PLCs with closed-loop control of such actuators provide the simplest method to achieve accurate force and velocity.
Additionally, electrified controls allow for easier machine automation integration, enabling complex operations sequences, feedback loops, and advanced control strategies like proportional-integral-derivative (pid) control. Machines can be programmed to perform tasks autonomously with minimal human intervention. Previous machine automation tactics in fluid power required myriad mechanical valves, miles of hydraulic plumbing, and sequence valves to achieve what a controller is capable of using grade-school-level machine logic.
Simplifying designs
Electrified systems reduce the need for complex mechanical and hydraulic control systems, such as cable linkages and pilot-operated levers. Instead of multiple hydraulic valves and levers, a single electronic controller can manage multiple functions, reducing system complexity. What previously took a dozen levers to achieve with hydraulic joysticks (Figure 1) can now be achieved with a couple of analog joysticks with auxiliary control switchgear mounted atop.
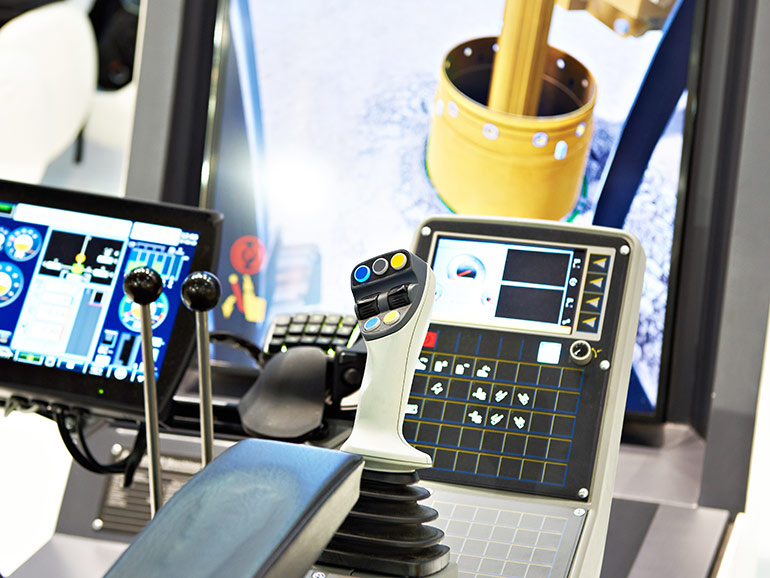
Even analog joysticks may have smaller thumb-actuated analog joysticks mounted to the upper portion alongside various possible rockers, toggles or pushbuttons, as seen in Figure 3. If you’ve played a console game system such as X-Box or Playstation, you’ll know just the types of control options available to today’s modern machines. As well, electronic controls reduce energy consumption by reducing the peak demand of the hydraulic system. For example, an older, complex machine will use power to supply the pilot circuit, which is essentially a mini hydraulic system within a hydraulic system.
Also, electronic control of hydraulics offers a more precise method to control flow and pressure. Old, human-adjusted pump and valve settings counted on the technician’s expertise in handling them, which could lead to errors or oversight, especially when inexperience plays a part. I’ve seen many circumstances where components were poorly adjusted to increase performance yet resulted in wasted energy, such as raising the pump’s compensator setting above the relief valve setting.
One of the most productive benefits of electrified systems is that they can be controlled remotely and connected to networks, allowing for remote monitoring, diagnostics, and even control from a distance. This is useful in hazardous environments or where access is limited, or the operator is better suited to operate outside the machine.
Cranes, stone slingers, tow trucks, forestry equipment, concrete pumps and mining equipment all benefit from the proliferation of wireless remote-control technologies. Stone slingers, for example, use a belly-box style wireless remote control, Figure 4, to operate conveyor velocity, boom position and even vehicle creep speed. Imagine the truck parked outside a fence preventing easy access for dumping. The stone slinger operator can position their machine on the side opposite of the fence and precisely apply gravel, sand or dirt where needed.
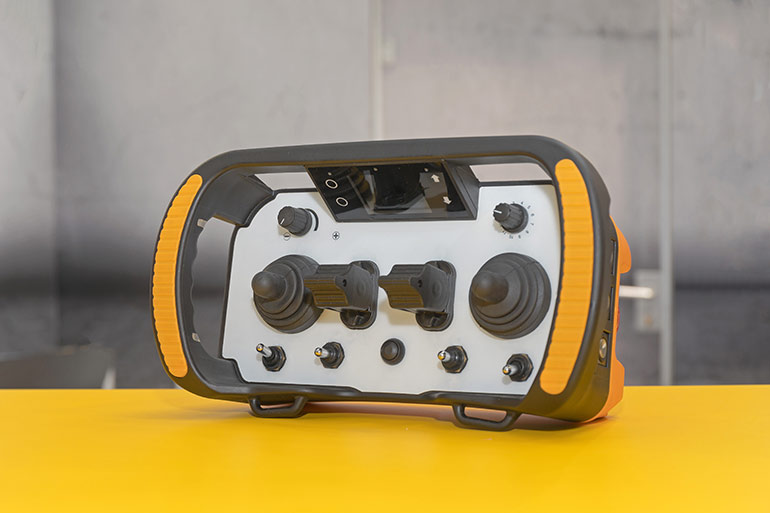
Belly box controls come in various designs, from simple switch-based layouts to complex joystick configurations. They must take into consideration operator ergonomics and machine complexity so that the operator can intuitively interact with the controls and the machine.
Electrified controls often result in fewer moving parts and reduced wear and tear compared to purely hydraulic systems. This can simplify maintenance routines and extend lifespan. There used to be concern over electronics in mobile machinery, particularly over the lack of backup systems should electronics fail. Many manufacturers select sandwich-style mobile valves using levers as backup control. Most designs come with proportional control, accessory valve ports, or even load sense circuits.
It used to be that electro-proportional control of mobile hydraulics required technical training to program and set up components and controllers. With the growth of inexpensive electronics, mobile devices, and workers who coded from the cradle, it’s easier than ever to adopt electronic control.
Filed Under: Components Oil Coolers, Controls, Engineering Basics, EV Engineering, Featured, Mobile Hydraulic Tips