By Walt Hessler
Edited by Mike Santora
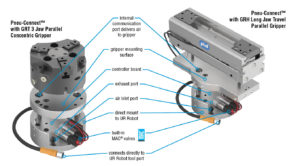
Pneumatic grippers provide a simple open and close jaw position verses the programmability of the electric grippers.
The simple definition of the word collaboration is: “The action of working with someone to produce or create something.” This is the exact purpose of a Collaborative Robot, or cobot. Cobots are typically power and force limiting. The robot can feel abnormal forces in its path and may be programmed to stop when it reads an overload in terms of force. The cobots are designed to dissipate forces in case of impact on a wide surface. As a result, the cobot may be used for direct collaboration with the worker for various tasks. The cobots can work alongside humans without any additional safety devices.
Typically, cobots are highly adaptable and virtually plug-and-play. This versatility means a user doesn’t need a great deal of experience to program and apply the device effectively. Some companies are using them because they can be placed alongside humans. Others are using cobots for ease of programming, quick uptime, and flexibility. As a result, these units are not always used in a collaborative environment.
Regardless of how and why a collaborative robot is used, the unit must have some type of end effector to perform a work function. These end effectors come in many forms including vacuum cups, grippers, and other specialty tooling.
Vacuum cups are suitable for picking up parts that are typically flat and require little to no precise registration. This is a relatively inexpensive method for grasping a part. The use of vacuum cups is limited by the weight of the part being handled and the acceleration and deceleration rate of the robot. Higher part weights and higher acceleration and deceleration rates can cause the part to slip. A mechanical gripper is better suited for heavier parts with higher acceleration and deceleration rates.
Mechanical grippers provide a positive precise part pick up and have placement when used as end effectors on the collaborative robot. These grippers are typically driven electrically or pneumatically.
Electric grippers are flexible with long jaw travel and have the ability to be programmed for various jaw travel lengths. These are well-suited for applications where the part size and shape change on a regular basis. Some electric gripper manufacturers offer an ‘app’ that installs into the teach pendant of the collaborative robots allowing the gripper to be programmed as part of the robot. Some of these electric grippers incorporate various types of tactile sensing, jaw force controls. Small motors are normally used to keep the weight of the gripper as low as possible. These small motors limit the jaw force produced by gripper. Higher forces may be achieved through gear reduction, which then limits the speed at which the jaws open and close. This will influence the overall cycle time of the cobot. The cost for these grippers can be as high as $15,000 depending on the sophistication of the unit.
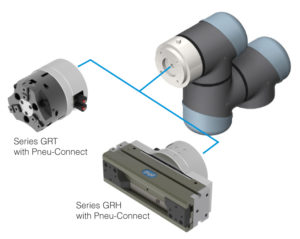
Pneu-Connect , a new accessory for seamless integration of pneumatic grippers on collaborative robots connects directly to the tool port on the robot arm making it easy to attach a PHD pneumatic gripper to a Universal Robot (UR) brand cobot.
Pneumatic grippers provide a simple open and close jaw position verses the programmability of the electric grippers. The pneumatic grippers for cobots are suitable in applications where the part size and shape stay relatively consistent. In most cases the pneumatic grippers are lighter since they do not incorporate an onboard motor.
Pneumatic grippers can also provide higher grip forces depending on the input air pressure provided. Most of these grippers are provided without the extended jaw tooling. This allows the user to create tooling to conform or encapsulate the shape of the part being handled. This jaw tooling is easy to create and can even be made using today’s modern 3D printers. By encapsulating the part with the jaw tooling the gripper can be operated at lower air pressures, suitable, if the cobot is being used in a human collaborative environment. The lower air pressures mean less force and less chance of injury. As stated earlier, many of the collaborative robots are applied because of their ease of use verses being used in a human collaborative environment. In these cases, the pneumatic gripper can be run at high pressures producing higher grip force and potentially allowing a smaller, lighter gripper to be used. This has a positive effect on the total payload of the cobot. The cost for a pneumatic gripper is also significantly less than the electric gripper.
Pneu-Connect , a new accessory for seamless integration of pneumatic grippers on collaborative robots from PHD, Inc., connects directly to the tool port on the robot arm making it easy to attach a PHD pneumatic gripper to a Universal Robot (UR) brand cobot. The Pneu-Connect incorporates a built-in pneumatic directional control valve for opening and closing the gripper. A connector is provided on the Pneu-Connect that plugs directly into the UR robot tool port. The Pneu-Connect comes with a “CAP” which is an application specific to the UR collaborative robot. The “CAP” runs inside of the UR control software and provides a graphical interface making the pneumatic gripper easy to use and integrate with the cobot.
There is a wide range of applications where a pneumatic gripper is the more cost effective end effector on a collaborative robot. One example would be a plastic manufacturer that produces high-volume injection molded products. The manufacturer prefers to pick and place the parts due to their high value verses ejecting them out of the mold and dropping onto a conveyor. This particular part has few variations with the sizes and shapes being very similar. A collaborative robot is chosen to perform this unload function due to the ease of programming and the ability to place the parts in rows to go on to the next process.
The plastic parts manufacturer is able to use a pneumatic gripper due to small variation in part size. The required jaw tooling to fit the part is able to be produced on a 3D printer and encapsulates the high value part ensuring it will not be dropped during the removal from the mold. In this case, the plastics manufacturer did not require tactile sensing or reprogrammable gripper jaw positioning or movement. The use of the pneumatic gripper on the cobot saved on the investment required to automate the process.
Be sure to weigh all the factors involved when selecting an end effector for a collaborative robot. Part weight, speed, required accuracy, and variance in part size and shape are all factors to consider. When the part size and shape have only small variances and there is a need for placement accuracy, a pneumatic gripper may be the most cost-effective choice.
PHD
www.phdinc.com
Filed Under: Pneumatic Tips