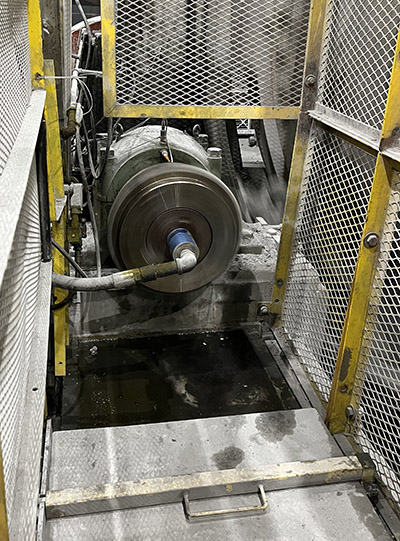
A compressed air auditor recently performed an energy audit at a mineral processing facility. Plant personnel were constantly complaining about production outages due to low pressure. The problem was that when the pressure dips down below 80 psi, the drive clutches on the large ball mills — that grind the processed down minerals to powder — will drop out, causing production to stop. These were found to be the most pressure critical applications in this plant.
Typically, the plant pressure holds at around 110 psi, but some transient demands operating at random cause the demand to exceed the capacity of the compressor, pulling down the plant pressure. A thorough analysis of the plant compressed air system determined that a number of uncontrolled ½-in. blow wands were consuming significant extra compressed air flow during cleaning operation and causing transient pressure dips lasting as long as 10 minutes.
The auditor noticed that the clutch compressed air supply had a large 240-gal receiver already installed, but it was lacking an important element. The clutches consume very little compressed air, so the existing tank has adequate to supply the clutches with stored air for many hours. However, whenever the main plant pressure went down, the general compressed air demand would steal the air out of the receiver to feed the deficit. A check valve was missing from the assembly — something that would have trapped compressed air with the storage receiver and protect the clutch supply from production outages.
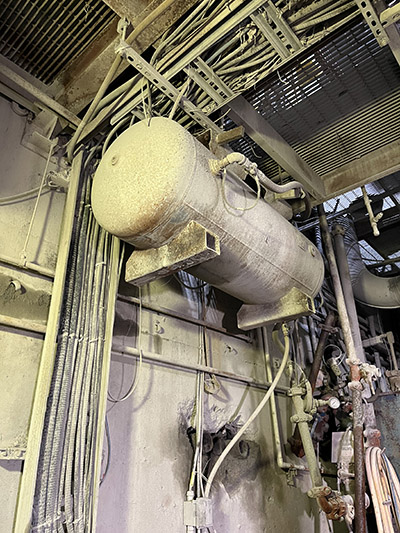
This strategy can be used for many pressure-critical applications that consume a small amount of compressed air. Use of this arrangement is discussed in the Compressed Air Challenge’s Advanced Management of Compressed air webinars.
Filed Under: Air Compressors, Air Preparation, Components Oil Coolers, Compressed Air Technologies, Pneumatic Tips