Lightweight robots with pneumatic drives working in collaboration with humans, and a gripper modeled on the octopus’s tentacles: the engineers from the Bionic Learning Network of Festo are presenting three future-oriented concepts at the Hannover Messe 2017 trade fair. While the BionicCobot is inspired by the natural movement of the human arm, the BionicMotionRobot is based on the elephant’s trunk and the octopus’s tentacles from the animal kingdom. A new bionic grasping device, the OctopusGripper, is likewise derived from the octopus. All three projects show what hazard-free, direct human-robot collaboration could look like in future.
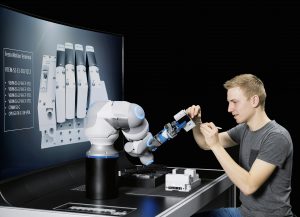
BionicCobot: a pneumatic lightweight robot with human movement patterns as a sensitive helper in human-robot collaboration (Photos: Festo AG & Co. KG)
Robots could be used as assistance systems for relieving the human operator above all in monotonous or dangerous work processes. The strict separation between the tasks of humans and those of robots is now increasingly making way for a collaborative working space. The bionic lightweight robots exhibited by Festo at the Hannover Messe are ideally suited for safe human-robot collaboration by reason of their natural movement patterns and their inherently flexible pneumatics. They can be a cost-efficient alternative to classic robot concepts in future.
BionicCobot – a pneumatic lightweight robot with human movement dynamics
The movement patterns of the BionicCobot are modeled on those of the human arm, from the shoulder via the upper arm, elbow, radius and ulna down to its gripping hand. Each of its seven joints makes use of the natural operating mechanism of the biceps and triceps – the efficient interplay of flexor and extensor muscles. It can thus execute very delicate movements, just like its biological model.
The movements of the BionicCobot can be finely regulated so as to be either powerful and dynamic, or sensitive and readily yielding; the system, therefore, cannot endanger humans even in the case of a collision. This is made possible by the “Festo Motion Terminal”, a pneumatic automation platform that unites high-precision mechanics, sensors and complex control and measuring technology within a very small space.
Depending on the task to be carried out, the BionicCobot can be fitted with different gripping systems. It is intuitively operated by means of a specially developed graphic user interface: the user can teach the BionicCobot the actions to be performed and parametrize them. The defined work steps can then be transferred by drag-and-drop to a sequencer track for implementation in any desired order. The entire movement sequence is virtually depicted and simultaneously simulated. The interface between the tablet and the Festo Motion Terminal is the ROS (robot operating system) platform, on which the kinematic path planning is calculated.
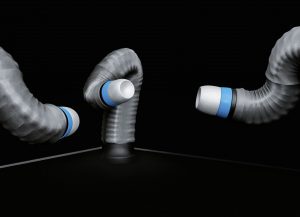
The movement patterns and function of the BionicMotionRobot were inspired by the elephant’s trunk and the octopus’s tentacles (Photos: Festo AG & Co. KG)
BionicMotionRobot – a lightweight robot with natural forms of movement
The elephant’s trunk and the octopus’s tentacles can move in a highly flexible way. The BionicMotionRobot effortlessly emulates these fluent movement patterns with its flexible pneumatic bellows structure and corresponding valve and control technology. The concept of inherently flexible kinematics is derived from the Bionic Handling Assistant from 2010, which received the German Future Award. A new type of outer skin made from a 3D textile knitted fabric now enables the BionicMotionRobot to fully deploy the great force potential of the entire kinematic system. The bionic robot arm thus has a load bearing capacity of almost three kilograms – with around the same net weight.
OctopusGripper – gripping modelled on the octopus’s tentacles
With the OctopusGripper, Festo is presenting a bionic gripper based on the octopus’s tentacles. It consists of a soft silicone structure that can be pneumatically controlled. If compressed air is applied to it, the tentacle bends inwards and can wrap around the object being gripped in a form-fitting and gentle manner. Just as with its natural model, two rows of actively and passively controlled suction cups are arranged on the inside of the silicone tentacle. This enables the OctopusGripper to pick up and hold a large number of differently shaped objects. The flexible gripper demonstrates its wide range of possible applications in combination with the BionicMotionRobot and the BionicCobot; the Festo Motion Terminal controls and regulates both the robot arm and the gripper. Thanks to its soft, inherently flexible structure, the OctopusGripper has great potential for use in collaborative working spaces in the future.
The Bionic Learning Network
Over ten years ago Festo initiated the Bionic Learning Network, which is closely linked with the processes of innovation within the company. In cooperation with students, renowned universities, institutes and development companies, Festo sponsors projects, testbeds and technology platforms. The objective is to benefit from bionics as a source of inspiration for new technologies and to realize these in industrial automation.
FESTO
www.festo.com/bionics
Filed Under: News