David Marlowe • Owner/CEO • DMAR Technical Training and DMAR Business Centers USA
Approximately 80% of all hydraulic component failures are attributed to surface degradation caused by contamination and corrosion. Proper filter selection and sizing will provide years of reliable equipment operation and save money that is lost in fighting contamination-related failures. The cost of installing and
maintaining suitable filtration is estimated to be 3% of the cost associated with contamination related issues.
Let’s start with pump suction strainers. Contrary to what some people think, pumps do not suck liquids through the inlet or suction piping, but rather create a differential pressure (dp) at the suction nozzle. The fluid is then pushed into the suction nozzle in an attempt to equalize pressure.
Anything that restricts or reduces the fluid flow affects its efficiency. This results in less liquid being transferred, and thus reduces system efficiency (horsepower in compared to horsepower out). Any suction pipe that encourages the introduction of entrained gas or affects hydraulic flow instabilities in the liquid will result in a less efficient pumping operation. In addition to poor performance, truly bad suction piping will result in physical damage to the pump or its parts.
Pump suction system configurations are broken down into two parts:
1. Suction piping (proper diameter and spacing)—proper suction piping consists of pipe and pipe fittings, their relationship, quantity and relative location to the pump suction nozzle.
2. Suction source (NPSHA) design factors include:
• geometry of the source
• relative location of the suction entrance point(s) to suction liquid surface
• source enclosure boundaries
• other suction entrance points
Every pump’s successful operation and useful life expectancy is dependent on a properly designed and installed suction arrangement.
Some would contend that a true state of absolute suction is impossible (except in the perfect vacuum of
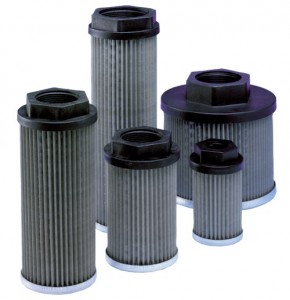
While many pump manufacturers caution against the use of suction strainers because of the damage they can cause, some designs, like Parker’s magnetic suction strainers, offer dual protection to the pump inlet without risk of cavitation.
space) and that only varying degrees of flow-causing differential pressure exist.
The term suction refers to the fluid acceleration toward the source (the pump). Pumps create a differential pressure, letting atmospheric pressure push liquid into a lower pressure area of the pump. Any impedance to unrestricted flow induced in this action will create instabilities in the fluid flow. The single most important function of a pump suction system is to supply an unrestricted, evenly distributed laminar flow to the pump. The pump suction system should not promote the introduction (or internal creation) of air, vapors or gas bubbles.
Improper designs of the suction piping, sump and/or inadequate pipe support exterior to the pump will create hydraulic instabilities in the fluid flow that result in destructive vibrations. In general, suction strainers do not contribute to system cleanliness.
Internal pump problems such as bearing failures, seal failures, excessive noise and vibration can often be accredited to sources outside the pump itself and the connected piping. The troubles created from poor suction conditions and poor piping practices will create unbalanced hydraulic flow.
To promote hydraulic stability and maintain a hydraulic balance on the pump’s rotating element, avoid direct connection of any type of pipe fitting to the pump suction nozzle. Pipe fittings cause pressure drops and turbulent flow patterns. Direct connection of elbows should always be avoided, as should 90° elbows. The only thing worse than a 90° elbow installed in the suction line would be having two of them!
It is important to select a filter that improves reliability of the hydraulic system to eliminate failures due to contamination. Let us look at the various options for the location of a filter. It is up to the system designer to locate a filter to support system operation, and location is subjective. The accompanying figure shows basic locations where filters are located in a lube or a hydraulic system.
The purpose of a suction filter screen is to protect the pump from large particles found in the reservoir. A filter screen is located on a suction port of the pump or attached to the suction pipe leading to the pump.
The filter screen is usually a coarse mesh filter. Inline filters are usually not placed on the suction side as high differential pressure can cause pump failure.
The micron rating of a fluid filter is a generalized way of indicating the ability of the filter to remove contaminants by the size of the particles, as seen below:
• 1 micron = 1 millionth of a meter
• 1 micron = 1 thousandth of a millimeter
• 1 micron = 39 millionth of an inch (0.000039)
• 25.4 micron = 1 thousandth of an inch (0.001)
• 40 microns = visible with magnification
• 40 to 90 microns = diameter of a human hair
A fine filter on a pump suction side would require a massive filter to handle the flow and have a low pressure drop. Fine filters load more quickly than coarse filters to allow the majority of small particles to pass. Improperly sized suction filters will cause pump failure due to cavitation. Many pump OEMs discourage the use of suction filters and suction strainers because of the inherent risk of pump hydraulic flow instabilities leading to cavitation.
Proper return filtration, transfer unit filtration and proper control of particulate ingression with high-efficiency breathers often make suction filtration unnecessary.
DMAR Technical Training
dmartechtraining.biz
Filed Under: Fluid Power World Magazine Articles, Pumps & Motors