Hydraulic drives in agricultural machinery must demonstrate high precision, reliability and flexibility under the most adverse conditions, according to the engineers at Bucher Hydraulics, Klettgau, Germany. Valves are critical components in such systems, as they are key to high energy efficiency and machine availability, reduced installation costs, compact size and lower weight, together with resource conservation. To harness these advantages, agricultural OEMs need access to a wide range of valves to help meet users’ application-specific demands without compromising performance.
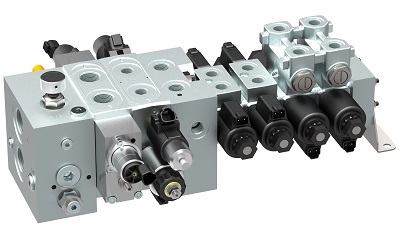
The LVS directional valve system from Bucher Hydraulics includes valves for actuator functions. A cost-optimized modular system of D-DS06 directional spool valves was developed to supplement SVH04 directional valves that feature bidirectional seat-type shut-off.
To meet current and future requirements, the valve specialists at Bucher Hydraulics — working in close cooperation with manufacturers of towed and self-propelled machines — have developed several new functions for the LVS series of proportional directional control valves. The compact LVS valves, with nominal flow rates up to 180 l/min and pressure ranges up to 350 bar, have been proven in the market for years. The expanded offerings include two-stage valves with electrohydraulic operation, direct-operated solenoid valves and more seat-valve combinations.
The new systems are configured to work seamlessly together within a LVS modular control block. OEM engineers can specify selected capabilities for a respective task, and the valve block can be expanded as needed, so machine manufacturers can install the exact configuration required at any time.
Valve blocks with up to 35 functions can be integrated for controlling highly complex machines. For example, in addition to single-acting hitch control (for towed and self-propelled machines), a double-acting hitch control is also available for towed machines such as slurry wagons with trailing-shoe applicators. With a double-acting LVS hitch-control valve, the trailing shoes can always be kept on the ground with proper contact pressure, regardless of hard or soft ground. This optimizes ground pressure distribution as well as depth control.
Complementing technically demanding proportional control via LVS valves, Bucher Hydraulics now offers valves for simple on/off actuator actions requiring only low flow rates. They are available in spool or seat versions. They supplement the well-known SVH04 directional valve that features bidirectional seat-type shut-off. The new directional spool valves can be complemented by hydraulically actuated or electrically switchable seat valves, which lets machine manufacturers economically perform simple on/off functions.
Special functions
High harvesting performance in self-propelled machines was also key in the design of an innovative expansion section with a split spool in terms of space, weight and cost savings. The product features two spools in one valve body with one spool bore. This means that two actuators can be controlled independently of one another – and in conjunction with a flow control valve that handles 180 l/min at 350 bar. The large oil galleries reduce pressure losses, increase energy efficiency and reduce diesel fuel consumption.
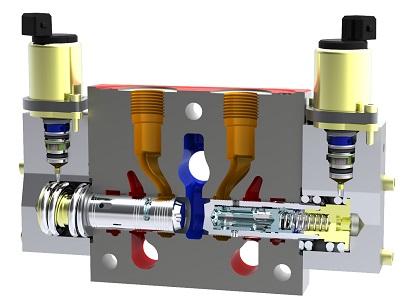
The LVS12 dual-flow control valve is used for pressure-independent, parallel operation of two single-acting actuators and saves both installation space and weight.
The split-spool technology enables a wide range of functions such as dual-flow control, and a lift/lower module in flow/return or return/return. The dual-flow control feature saves installation space and weight and, for example, is suitable for pressure-independent, parallel operation of two single-acting motor drives.
The lift/lower module provides load-compensated lifting and lowering. To ensure stability, the system uses highly dynamic valves that accurately implement control signals even at a high command frequency with signal durations of just 10 msec. The flow and return function corresponds to an adjustable pressure support in that flow and return spools can be actuated and positioned independently of each other. By varying the ratio of the flow and return openings, any required pressure can be created at the actuator outlet.
Auxiliary systems
The company’s EPOM program (Externally Propelled Off-Highway Machines), developed specifically for towed machines, includes a full range of adaptable electrohydraulic systems. All hydraulic and electronic components are characterized by their high reliability in the field: they deliver optimum service even with fluctuating temperatures, high mechanical loading and electromagnetic interference. Users can choose between two control units for the analog-proportional control of up to 8 or 11 valve sections via toggle switches and rotary potentiometers, and it includes a wiring harness. The components have a tank-line pressure rating of 210 bar, so that eve a misconnected hose will not damage the hydraulic system. Thanks to the low off-load and block head-losses, up to 150 l/min at the actuator ports is possible with a pressure difference of only 9 bar.
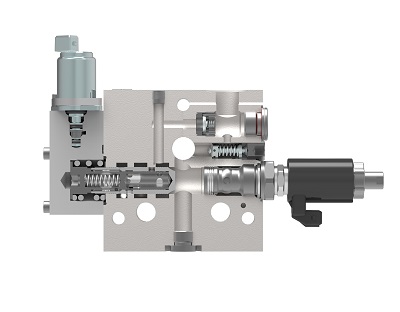
The LVS12 hitch-control valve is a highly dynamic lift/lower module for load-compensated lifting and lowering in systems requiring up to 150 l/min and 350 bar.
The EPOM program includes specially designed auxiliary-function sections aimed primarily at improved travel comfort: the top cylinder, undercarriage and drawbar suspension sections facilitate increased traction, maintain a constant level, and absorb travel shocks. An axle-lift section reduces tire wear and diesel fuel consumption, and the axle-suspension section enables weight-dependent control.
Driving safety in agricultural machinery is, of course, critical too. In the case of towed machines, the systems are predominantly based on castor steering. These only work in forward gear and are otherwise locked by seat valves. With an additional, special electrical steering system, Bucher Hydraulics offers a component to increase safety, as this additional steering system is also active when reversing and is used for the speed-adjusted steering of one or two axles.
Electrohydraulic steering systems from the EPOM program are also available. With these systems, users benefit from special steering valves featuring a downstream pressure compensator. These steering valves can be integrated directly into the valve block without the need for the otherwise standard additional priority function, which saves cost and space. Other highly responsive valves suited for the harvesting process provide automatic steering, which ensures ongoing corrections as well as row-sensing. Another special feature is that Bucher Hydraulics equips its steering valves with self-compensating spools: after a displacement, the restoring force back to the neutral position is independent of the load.
The Bucher systems are readily adapted to the tractor. For instance, valve operation can easily be set for either fixed-displacement or load-sensing supply systems. Using an adjustable pressure compensator in the inlet section, which can be changed from 2-way to 3-way operation, users can employ the same valves for both open- and closed-center systems, thus ensuring that a constant flow rate is always available for the valve block in the towed machine regardless of the type of pump in the tractor. Even when there are sizeable pressure drops in the lines, sufficient pressure is always available for control functions in this application, which saves energy.
Bucher Hydraulics
www.bucherhydraulics.com
Filed Under: Mobile Hydraulic Tips, News, Valves & Manifolds