The AirFlowSaver from KTW Technology, Wehr, Germany, is an integrated system that reduces compressed air consumption while improving productivity in many industrial applications, including blow-off, drying, degreasing, cleaning, material handling and certain pneumatic control tasks. It works by converting continuous air flows into sharp and powerful pulses that increase output force. Thus, it cuts air use and operating costs while speeding process throughput.
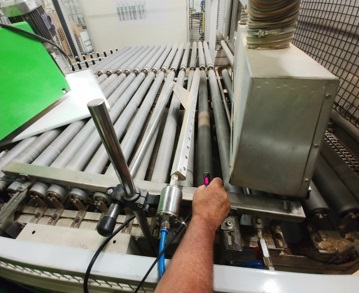
The AirFlowSaver (AFS) has three operating modes:
• Continuous pulsing at a predetermined frequency over a fixed time.
• Continuous pulsing with a frequency that varies over time.
• Event-controlled, for example initiated by a sensor signal.
Heart of the system is KTW’s SmartValve, a new type of flow-control valve that relies on a magnetized ball as the fluid-control element. When closed, a pressure differential between the valve inlet and outlet holds the ball on the valve seat. To actuate the valve, electric current energizes a solenoid coil in the valve housing. The resulting magnetic field force laterally pulls the ball off the seat — permitting flow. Shutting off power eliminates the magnetic field, so flow forces return the ball back to the seat and the valve closes. Extremely fast (1 msec) switching allows for real-time applications.
SmartValves typically operate with pressure differentials of between 1 and 10 bar (14.5 to 145 psi). AFS performance can be scaled as needed thanks to standard valves that offer maximum flow rates from about 14 m3/hr (8.24 cfm) to 85 m3/hr (50.03 cfm).
Other essential components include the valve controller, power supply, and sensors that initiate start/stop actions (trigger events). Also critical to overall system performance are application-specific output nozzles and air knives that come in numerous shapes, types and sizes. They optimize flow output, reduce noise and direct the pulsating compressed airstream to the desired target. All the components are functionally fine-tuned to match the system’s flow, force and efficiency strategy and offer maximum benefits in each specific application.
High-performance applications in terms of frequency and flow need closed-loop current control to ensure precise and repeatable valve behavior. KTW’s proprietary Controller Output Stage operates SmartValves at high speeds (reaction time from trigger input to switch of valve = 1 msec) and short switching cycles (from fully closed to fully open to fully closed within 1.5 to 2.0 msec). Depending on the size and media, customized valves can run at frequencies of up to 3,000 Hz. Communication with the system is via intuitive software (USB interface) or a CANbus network. Thus, users can manipulate valve/pulsing parameters in real time.
Experience at customer installations shows that the AFS reduces compressed air-consumption by 60% to 90% — resulting in significant energy savings. Just as important, it improves process quality, as the pulsed beam generates about 15 to 20% higher impulse force compared to a continuous flow. That, in turn, can speed processes and improve productivity.
Depending on the installation, it lets users downsize the compressed air system and avoid unnecessary capital spending. Long service life of the solenoid valve (>3 billion switching cycles), high reliability and a maintenance-friendly design equate to increased equipment and plant availability. And energy efficiency upgrades may qualify for tax benefits. All told, investments in the AFS show payback (ROI) in less than one year.
The AirFlowSaver can operate as a standalone unit or as part of an integrated system. The modular design permits distributed mounting of individual components and, thus, can be easily configured and adapted to almost any application and any orientation. And the system is readily scalable in throughput and force via the number and size of valves.
Specific applications where the new pulse system shows tremendous promise include:
• Drying packaged products or beverage containers. Because they are often discretely moving on conveying lines and spaced apart, an on-off system is of great benefit.
• Removing unwanted matter. The inherent scrubbing action can remove sticky material from parts with an oily residue. Or similarly, cleaning rough surfaces like wood, where pulsing action helps dislodge hard-to-remove debris.
• Part ejection. The amplified force action can move heavier parts on conveying systems.
• Cleaning parts. Combining the pulse system with air knives and static eliminators produces cleaner parts in the semiconductor industry. The same holds in painting operations, in particular those involving plastic auto bumpers, door panels and instrument clusters.
Engineers should consider the AirFlowSaver in any industry that is plagued by high consumption of compressed air. That includes metalworking, packaging and beverage bottling, electronics production, painting, and paper, wood and furniture manufacturing, just to name a few.
PHIR Technologies, Hartland, Wis., represents KTW Technology GmbH in North America.
KTW Technology
ktwsystems.com
Filed Under: Pneumatic Tips