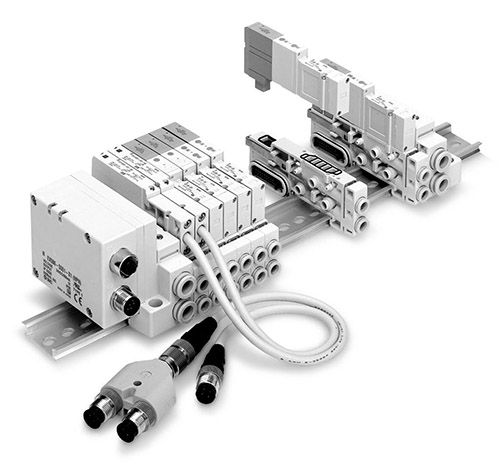
SMC’s VQZ line features a high-speed response time, long service life and built-in one-touch fittings.
Pneumatic valves are common in every industry, in applications from medical to chemical and automation to corrugation. Compressed air is readily available, clean and easy to use, so the number of markets taking advantage of this technology is no surprise. Two of the larger industries are automation—which uses cylinders and other actuators to produce or process goods at a blinding rate—and the food industry—which can take advantage of the same quick processing of goods without contaminating the final product, while being resistant to liquids or other food additives.
Before the proliferation of electronics, pneumatic valves were used to create automation cells. The vast combinations of valve configurations combined with myriad plungers, cams, rollers and pilots allowed compressed air alone to operate massive and complex automated machinery. Without a single electrical wire, an entire packaging machine, for example, would operate and cycle, coursing and flowing endlessly, requiring only a palm button to initiate.
Pneumatics is an old technology, and for years, there have been basic methods of design and construction. There are common configurations built with spool valves, poppets or other forms, and these configurations are based on the number of ports the valve has and the number of valve positions available. The ports are called ways, for some reason, but this adds clarity to the term “5-way, 3-position,” which describes a directional valve with a pressure, two work and two exhaust ports, that are moving between two energized and one neutral position. But this topic isn’t about those standard 5/3 valves.
For machinery or applications outside the standard apparatus, unique valves exist for specialized equipment and processes. There are industries needing attention, and with a market saturated with me-too products, manufacturers are increasingly applying their engineering and marketing capacity to niche products. These products fill gaps required by OEMs and machine builders, themselves trying to stand apart in a competitive world of commodity products.
Pneumatics provides cleanliness for medical applications
The medical industry is unique in its pneumatic applications. Often times, the system or machine is simply part of a process—such as cleaning instruments or testing samples. Equipment manufactured for the medical industry must meet stringent standards for quality, cleanliness and safety. Not only must pneumatic valves be reliable when lives are on the line, they must be manufactured with utmost attention to cleanliness. By-products of the manufacturing process cannot be left behind to be ingested or infected into a patient.
No greater importance for cleanliness can be found than with equipment designed to clean and sterilize surgical tools and equipment. Although the techniques for the process can vary, the goal is to efficiently destroy microbes existing on chisels and choppers or specula and strippers, which guarantees the surgical process isn’t a contributor to a patient’s ill health.
SMC is a pneumatic product manufacturer, and you wouldn’t be surprised to discover they have product lines suitable for surgical equipment sterilization. Their VQZ valve line has been approved and licensed by both the FDA and Heath Canada for a proprietary sterilization process. Using low temperature sterilization vastly hastens the sterilization process time from five hours down to one hour, using vaporized hydrogen peroxide and ozone to destroy pathogens.
Using various valves, the sterilization chamber is first subjected to a vacuum of 1 Torr before the vaporous hydrogen peroxide is injected at a fixed rate through micro-pulsation of the VQZ valve, which has rapid response time, especially with the metal seals required for this application. The pulsing of the hydrogen peroxide continues until the chamber pressure reaches 19 Torr, and then the reduction cycle begins. Ozone is now injected to react to the hydrogen peroxide to form hydroxyl radicals, further increasing lethality to the microbes. After the process is complete, and using a catalytic converter, the by-products of the process are oxygen and water, making the chamber safe to open and remove the surgical instruments.
It goes without saying, a standard, off-the-shelf valve wouldn’t work well in a high-performance, demanding application such as this. The VQZ valve is available with metal seals, high-powered solenoids, IP65 rating and CE certification. Some valves may be available with some of these options, but it’s the combination of these features that allows it to be used in such a demanding duty.
SMC also makes valves and components for blood analyzing equipment. If you’ve been to a medical lab recently to give blood, you know they process patients like concert goers in line at Wembley Stadium. The volume of blood samples, and the number of available tests to those samples, is extraordinary, and would be impossible using the old method of testing individual cartridges by a lab technician.
Modern laboratories use automated machinery to perform biochemical analysis. The process to analyze blood requires cuvettes (sample cups) to be placed into carousels via pneumatic robots. The valves and actuators used are too numerous to describe here, but nearly every function and process uses an SMC component. Even the chilling and handling of reagents is handled via their equipment, and once the process is complete, SMC’s LVM series pneumatic diaphragm valves process the saline and bleach for cleansing.
Using pneumatic components for these applications requires special materials, such as acrylic manifolds for fluidic circuits, similar in concept to those made for compact hydraulic manifolds using cartridge valves. Fluidics are used for the precision logical control of some of the components in the blood analyzer machine, and the special manifolds prevents leaks caused by tubes and fittings. The best way to describe fluidics is to imagine an electronic circuit—but instead of electrons, there are fluid molecules. Jets of fluid can create fluidic amplifiers, triodes and logic elements. This type of unique application of pneumatic valves ensures fluid power has a place in the modern world of technological advancements, and even nanotechnology considers fluidics as an important concept under its umbrella.
Safe, precise control for industry
The medical industry alone does not hold the monopoly on unique valve applications. Even though the typical domain of high-powered hydraulics has a pneumatic counterpart, the hydraulic press has long been the poster child of industrial power. But pneumatic presses are common for their rapid cycle rate, and are used for riveting, punching, crimping and swaging, for example. The challenge with presses closing at a rapid velocity is the potential for human interference as parts are loaded in and out of the machine. Also, the press must be safe during tooling changeover or maintenance.
Because of the potential for danger, regulations for press safety are stringent, and all precaution must be made to prevent unintentional movement of the press and its platen. If the press is mechanical, clutches and brakes are used to ensure the press doesn’t cycle when not intended, and often the clutch and brake are pneumatically controlled. The pneumatic circuit to control the movement of pneumatic pressure—or the clutch and brake of mechanical presses—should be inherently safe, but with redundant controls to prevent accidental operation, or prevent operation when there is a problem.

SERPAR Crossflow 35 Series valves from ROSS Controls can be integrated with external monitoring systems to provide for lockout—this inhibits further machine operation until the controls system is reset.
You could use two pneumatic valves in tandem to create a circuit requiring both valves to function simultaneously to allow press operation, but it just so happens ROSS Controls manufactures its Double Valve, itself a press safety valve operating two valve elements in one body.
The double valve contains two unique valve elements with combination shapes of pistons, poppets and spools, mounted abreast in a single valve body. The internal porting plumbs each element in series so that both are required to be energized simultaneously for airflow to occur. Should one valve element fail open or closed, the valve limits work port pressure to a fraction of inlet pressure, preventing the pneumatic press cylinder or clutch from engaging, or prevents the brake from releasing.
The valve works via pressure differential on each valve element, and the function is impossible to defeat since the plumbing is internal. On top of its inherently safe design, the valve is available with dual pressure switches to monitor the pressure at each valve element. When the valve is not actuated, a signal is present at the normally closed output line of each pressure switch. When the valve is actuated, the switch circuits are reversed and a signal is present at the normally open output lines. The redundant electrical safety provides an extra step of security should machine failure be imminent, and with these features, this safety valve has been popular for years.
In short, the realm of pneumatics is more vast, and specialized, than what can be found in off-the-shelf 5/2 valves and FRLs. As long as there is demand for a unique application, manufacturers will create it. As a result, pneumatics will continue to be a top choice for solving difficult applications.
SMC
smcusa.com
ROSS Controls
rosscontrols.com
Filed Under: Pneumatic Tips, Valves & Manifolds